Gravity Roller Conveyor Manufacturer
Home > Roller Conveyor > Gravity Roller Conveyor
Discover premium gravity roller conveyor solutions from a leading roller conveyor manufacturer. Our wide range of gravity & powered roller conveyor systems deliver exceptional efficiency for all logistics needs.
Our Gravity Roller Conveyor Products
525 mm
1500 mm
50 kg/m
Flat-bottomed Goods
Bagged Goods
485 mm
1700 mm
50 kg/m
Flat-bottomed Goods
Bagged Goods
Gravity roller conveyors represent one of the most cost-effective and energy-efficient material handling solutions available today. As a professional gravity roller conveyor manufacturer, we understand how these seemingly simple systems can dramatically transform warehouse operations, distribution centers, and manufacturing facilities. Operating without motors or electrical components, gravity roller conveyors utilize the natural force of gravity and minimal inclines to move products smoothly from one point to another.
These versatile conveying systems create an ideal balance of functionality, affordability, and reliability. Whether you’re managing a small warehouse operation or overseeing a large logistics facility, the right gravity conveyor solution can streamline your material handling processes while reducing operational costs and environmental impact.
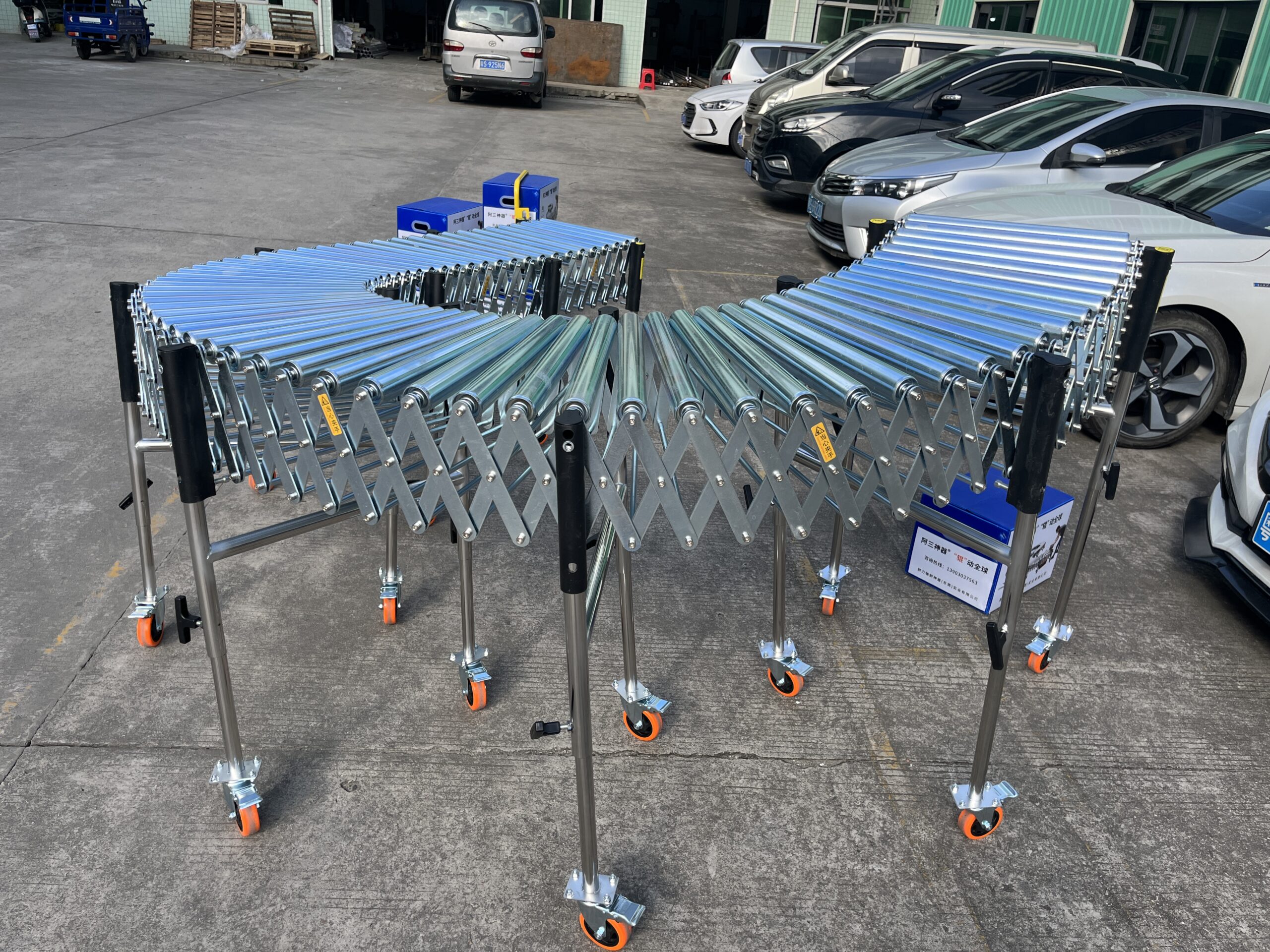
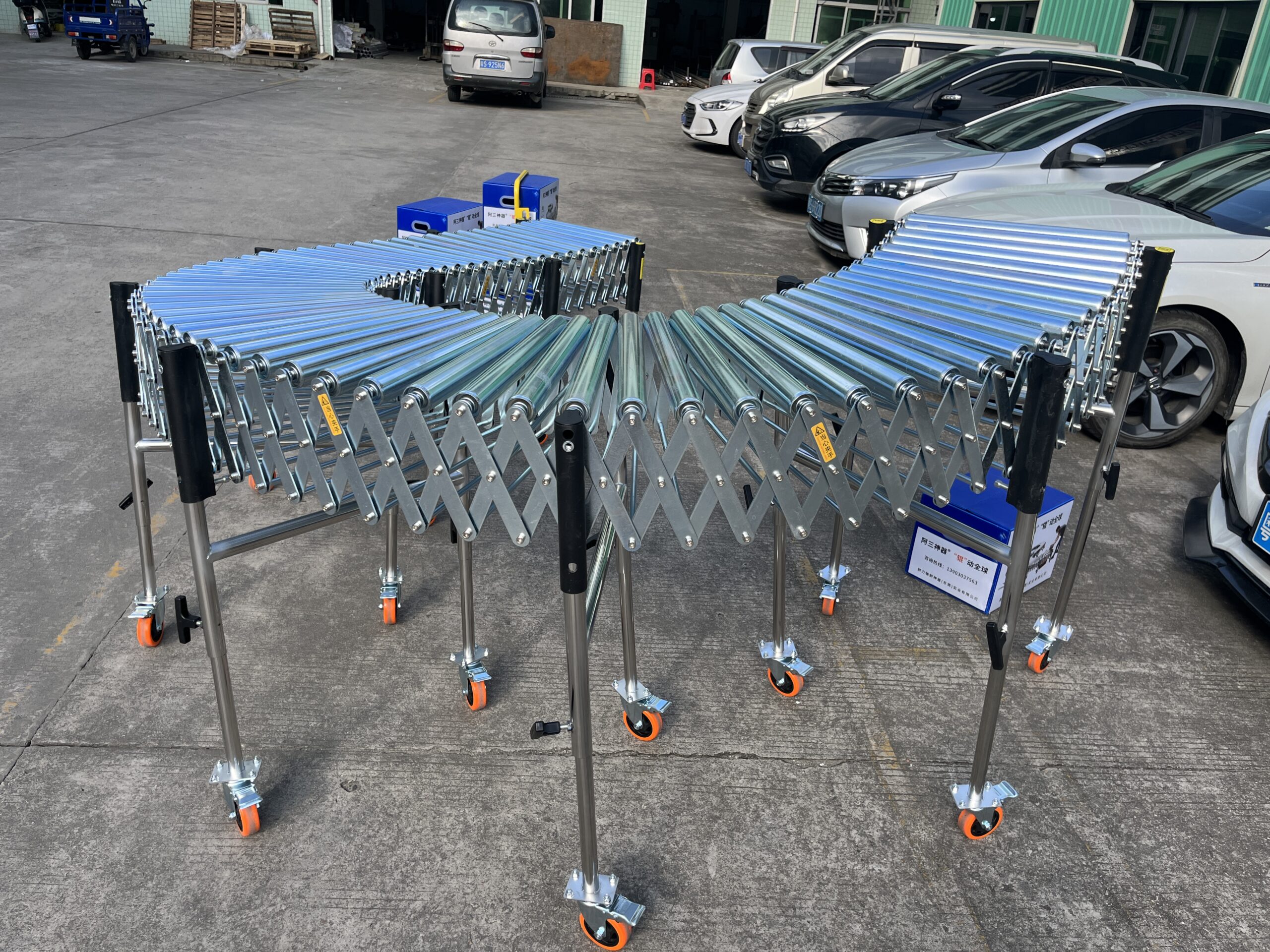
Types of Gravity Roller Conveyors
Our gravity roller conveyor product line features two distinct models, each designed to address specific material handling requirements:
50mm Diameter Roller Conveyor
The 50mm diameter roller conveyor represents our standard duty solution, featuring:
- Robust Design: 50mm diameter galvanized or stainless steel rollers with ≥1.5mm thickness
- Superior Extension: Extends from 525mm to 1500mm with a 1:3 extension ratio
- Strategic Spacing: 110mm roller spacing with 9-10 rollers per section
- Solid Framework: 35×35mm stainless steel H-frame construction
- Versatile Width Options: Available in 500mm, 600mm, and 800mm widths
- Reliable Capacity: 50 kg/m weight distribution capacity
This model is particularly well-suited for medium-weight packages and cartons with firm, flat bottom surfaces.
38mm Diameter Roller Conveyor
Our 38mm diameter roller conveyor offers a lighter alternative with:
- Lightweight Design: 38mm diameter galvanized or stainless steel rollers
- Greater Extension: Extends from 485mm to 1700mm with a 1:3 extension ratio
- Wider Spacing: 150mm roller spacing with 11-12 rollers per section
- Sturdy Framework: 38×38mm stainless steel H-frame construction
- Multiple Width Options: Available in 500mm, 600mm, and 800mm widths
- Consistent Capacity: 50 kg/m weight distribution capacity
This model is ideal for lighter packages and applications where weight reduction of the conveyor itself is beneficial.
Both models feature adjustable height support legs with options ranging from 450-680mm to 900-1500mm, accommodating various operational requirements.
Key Features and Benefits
As a leading gravity roller conveyor supplier, we’ve engineered our products to deliver exceptional value through these key features:
Energy-Efficient Operation
- Zero Power Requirements: Operates using gravity alone, eliminating electricity costs
- Environmental Sustainability: Reduces carbon footprint with no energy consumption
- Independence from Power Sources: Functions reliably even during power outages
Operational Advantages
- Low Maintenance: Minimal moving parts means reduced maintenance requirements
- Quiet Operation: Creates a more pleasant working environment without motor noise
- Simple Installation: No electrical connections or complex setup procedures
- Modular Design: Connect multiple sections to create customized conveyor paths
- Mobility: Equipped with caster wheels for easy repositioning as needs change
Economic Benefits
- Lower Initial Investment: Significantly more affordable than powered systems
- Reduced Operating Costs: No electricity consumption and minimal maintenance expenses
- Long Service Life: Durable construction ensures 5-10+ years of reliable operation
- Space Optimization: Utilize vertical space through inclined conveyor arrangements
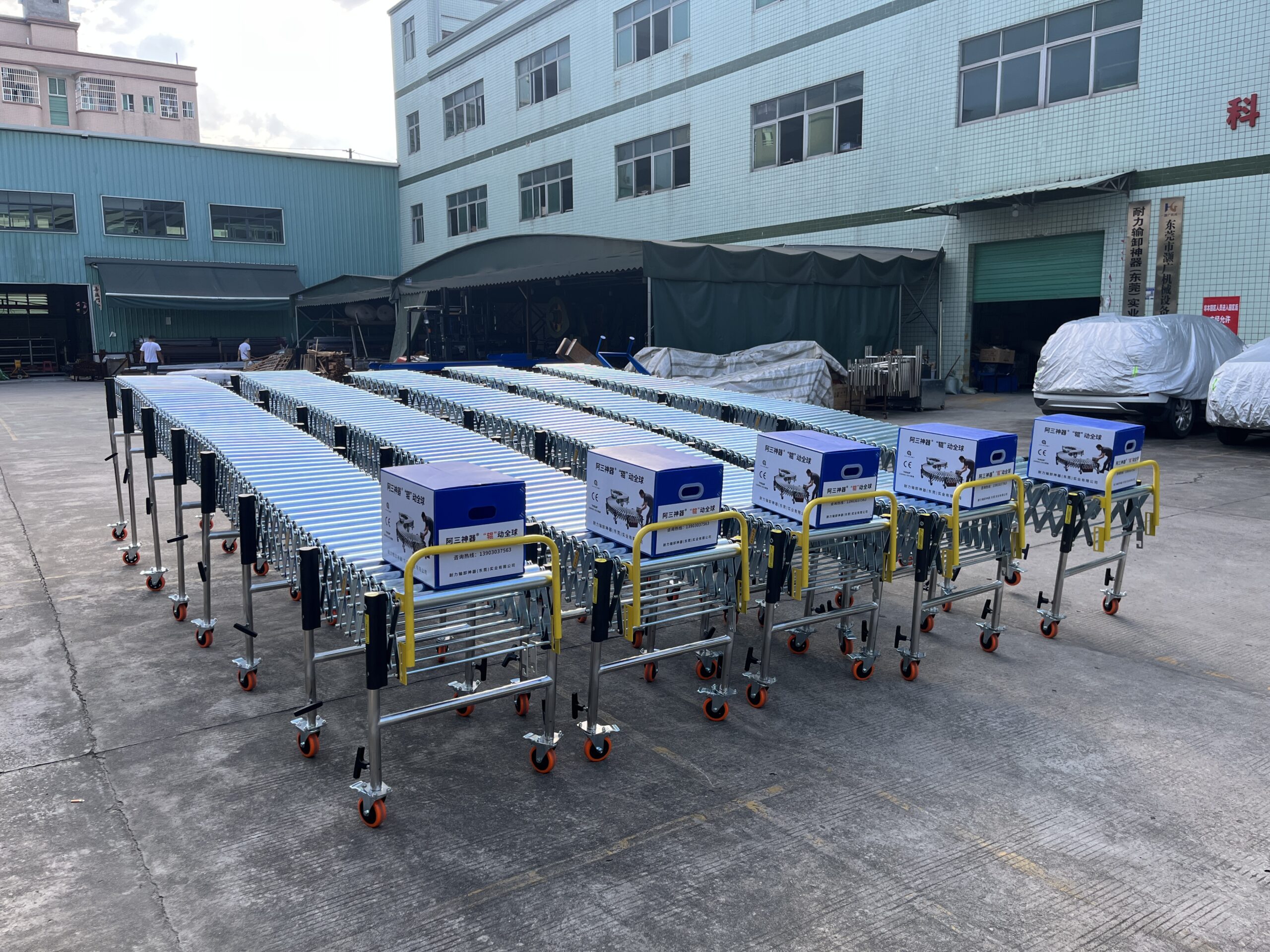
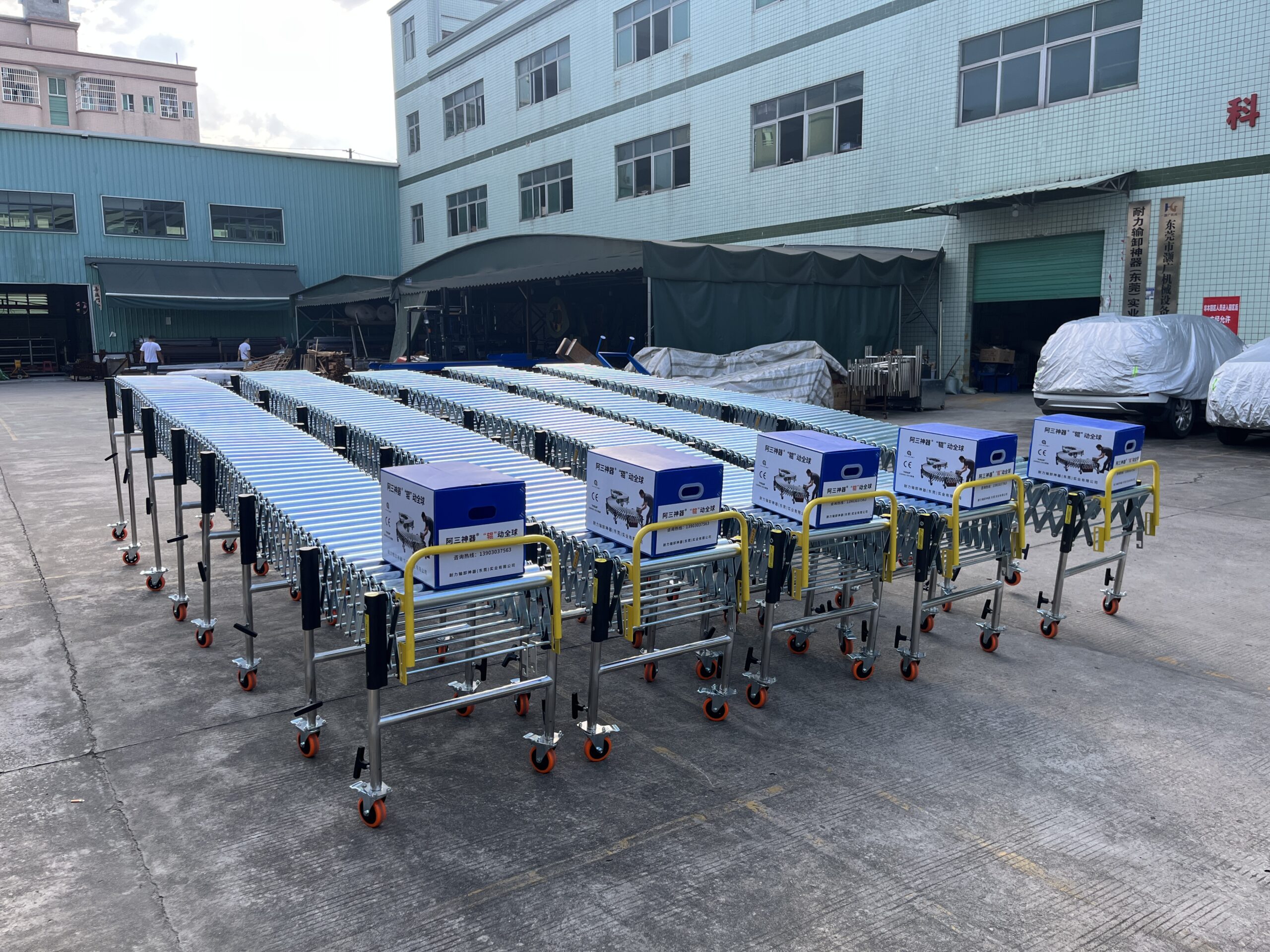
Applications and Industries
Our gravity roller conveyors excel in diverse applications across numerous industries:
Logistics and Distribution
- Package sorting and routing between workstations
- Order fulfillment pathways in e-commerce operations
- Loading/unloading zones for shipping and receiving
Manufacturing
- Component transport between assembly stations
- Connecting production areas with minimal elevation changes
- Temporary material routing during facility reconfiguration
Retail and Warehousing
- Stock movement from storage to picking areas
- Order consolidation zones
- Inventory transfer systems
Parcel Handling
- Express delivery sorting facilities
- Mail processing centers
- Package transfer between processing stations
Food and Beverage
- Packaging line routing
- Case handling between production and packaging
- Quality control inspection lines
The versatility of our gravity systems makes them ideal components of comprehensive material handling solutions, often connecting with other conveyor types to create complete systems.
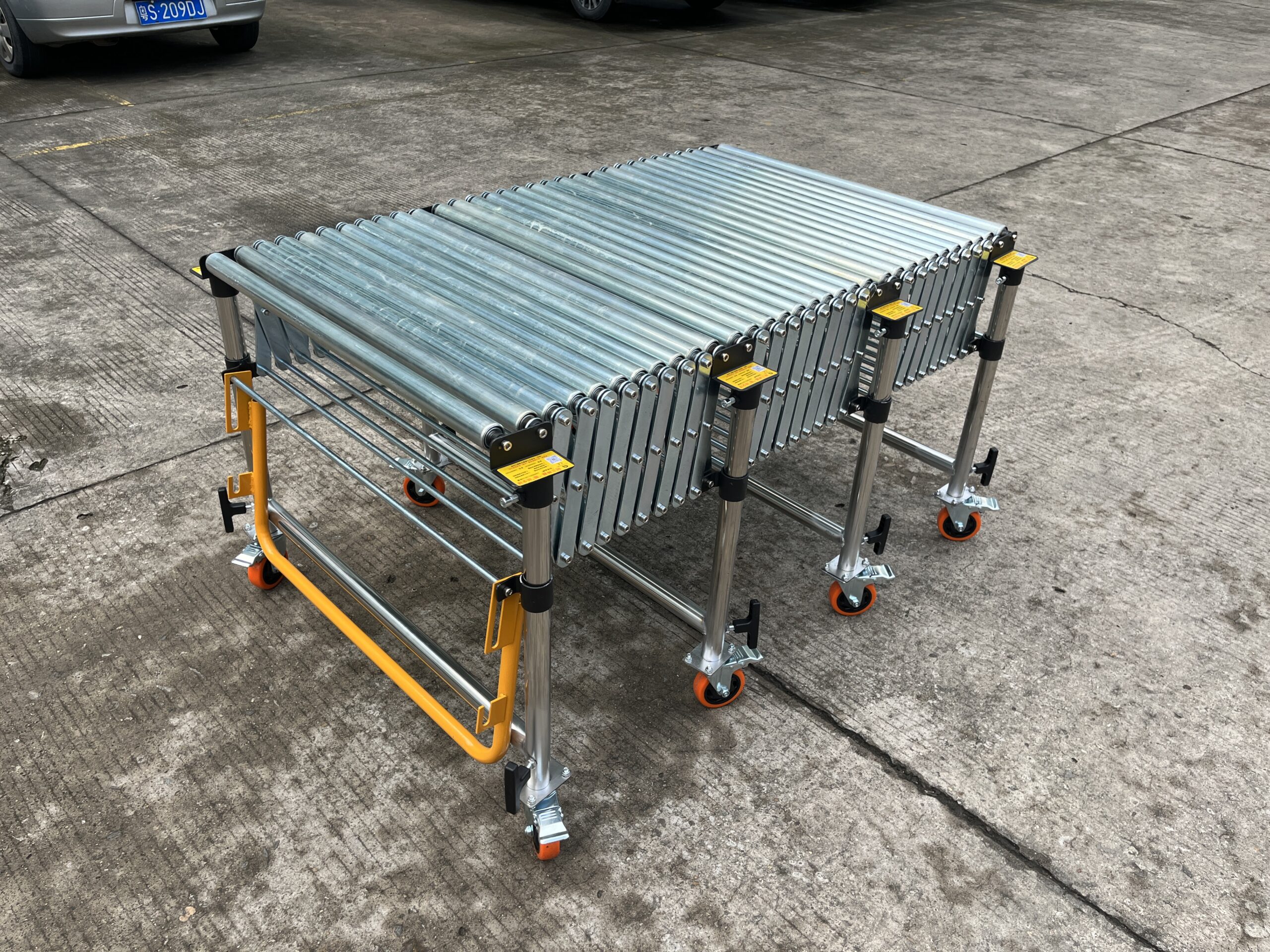
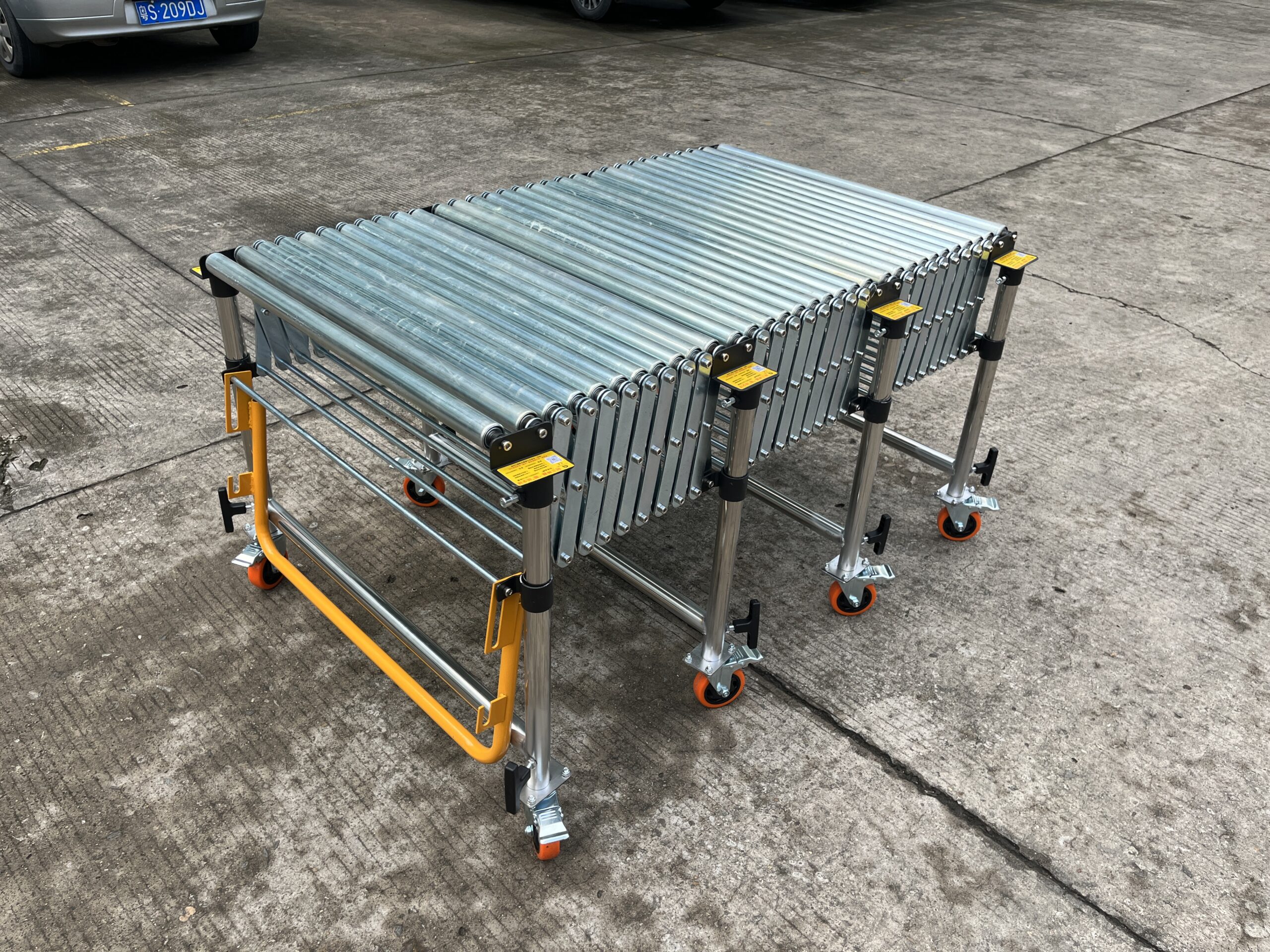
How to Select the Right Gravity Roller Conveyor
When choosing a gravity roller conveyor system for your facility, consider these key factors:
Package Characteristics
Consideration | Recommendation |
---|---|
Small packages or irregular bottoms | 50mm rollers with closer spacing |
Large, flat-bottomed cartons | 38mm rollers with standard spacing |
Mixed package types | 50mm rollers for maximum versatility |
Soft or flexible packaging | Consider alternative conveyor types |
Operational Environment
- Available Incline: Ensure sufficient height differential (typically 2-5 degrees)
- Space Constraints: Measure available space for both extended and collapsed configurations
- Connection Points: Consider how the gravity conveyor will integrate with existing systems
- Mobility Requirements: Determine if fixed installation or portable configuration is needed
Technical Considerations
- Weight Capacity: Assess maximum load requirements against the 50 kg/m capacity
- Roller Spacing: Choose appropriate roller spacing based on package dimensions
- Width Selection: Select conveyor width that exceeds your widest package by 50-100mm
- Support Configuration: Determine optimal height adjustment range for your application
As a professional gravity roller conveyor factory, we can provide customized recommendations based on your specific requirements and operational parameters.
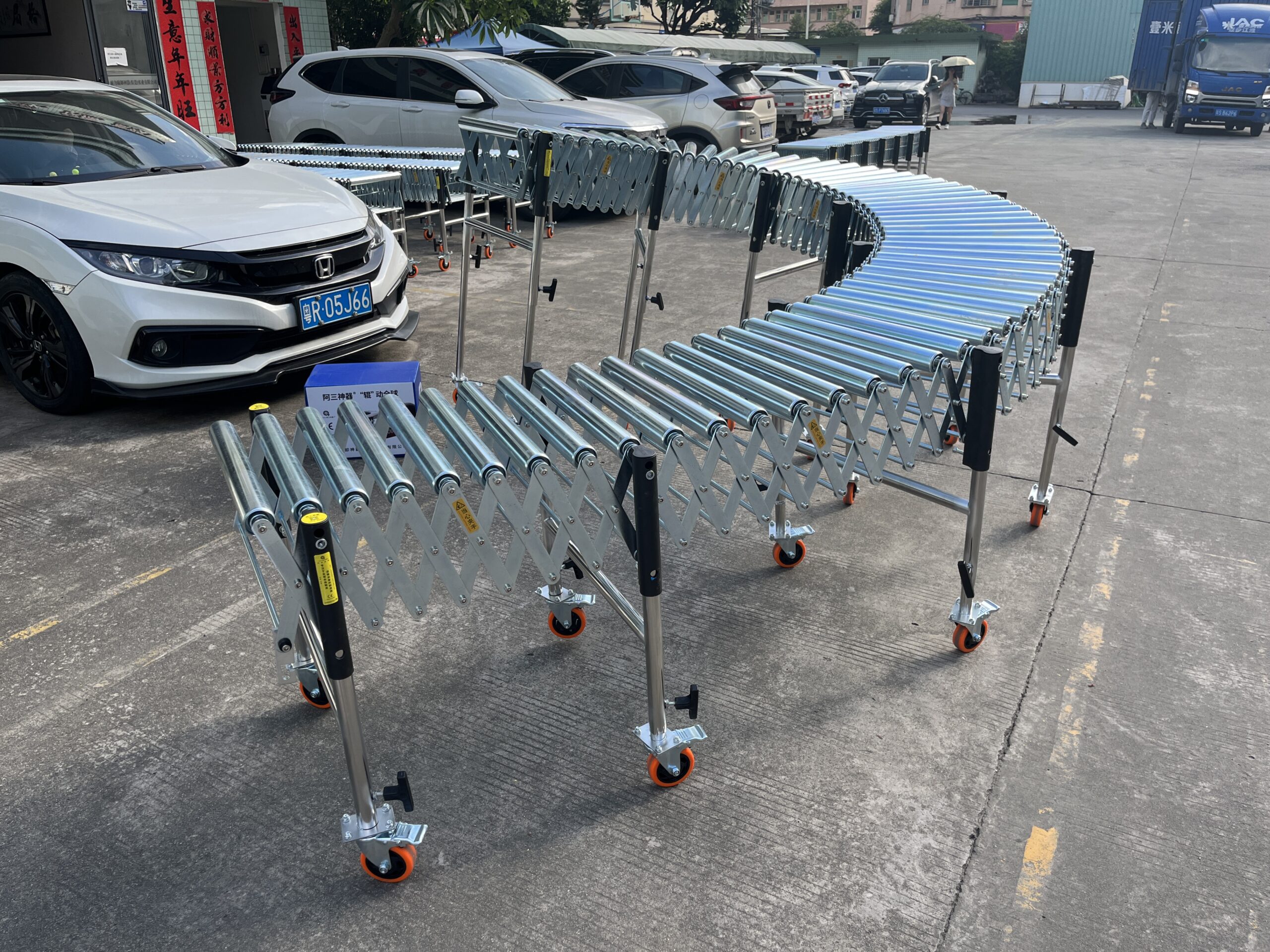
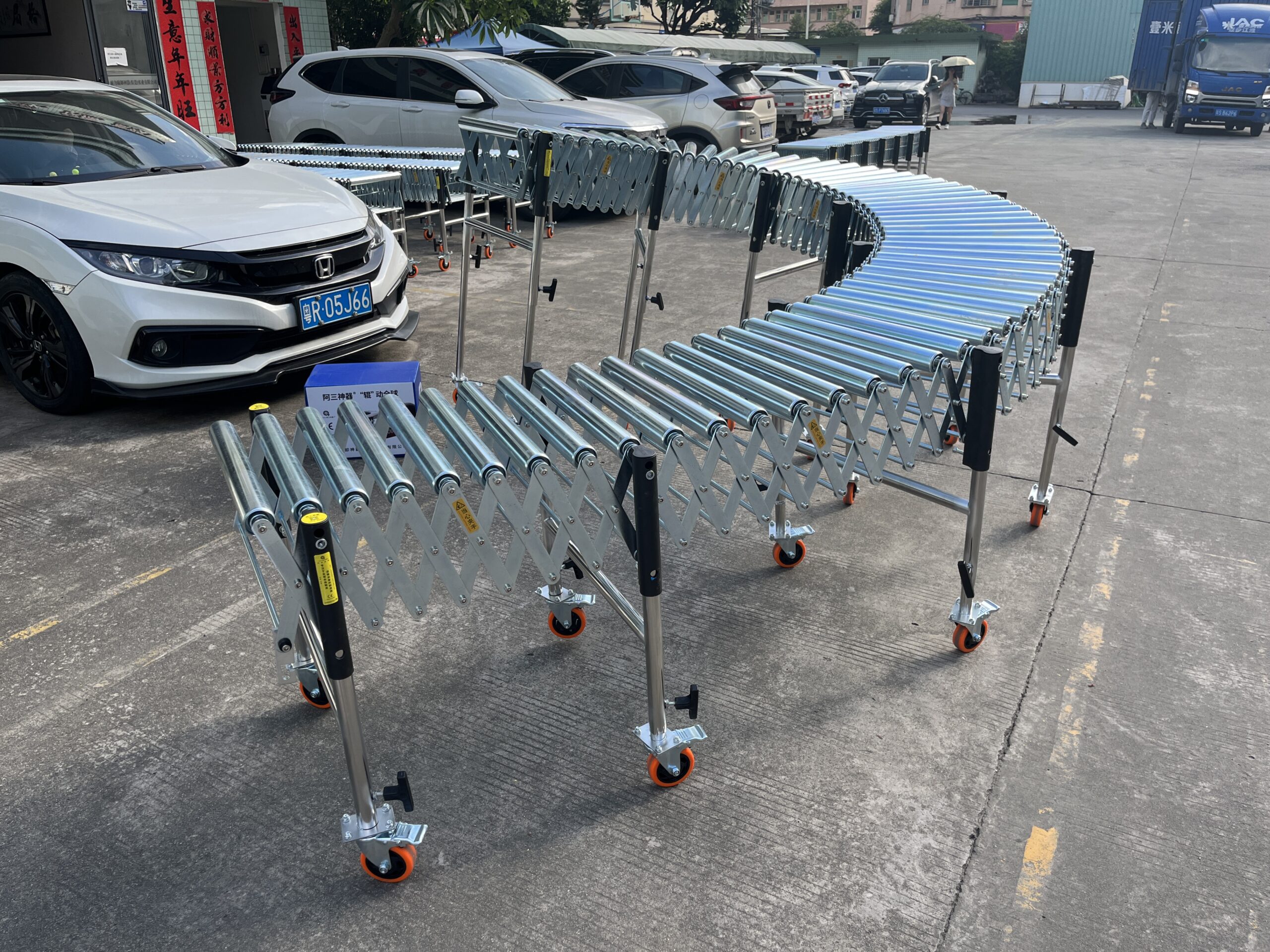
Maintenance and Care
Proper maintenance ensures optimal performance and longevity of your gravity roller conveyor system:
Regular Inspections
- Check rollers weekly for smooth rotation and proper alignment
- Inspect frame connections monthly for stability and tightness
- Verify support leg adjustments remain properly secured
Cleaning Procedures
- Remove debris and dust accumulation from rollers bi-weekly
- Clean frame components as needed to prevent corrosion
- Ensure guide rails remain clear of obstructions
Preventative Maintenance
- Lubricate roller bearings quarterly according to usage intensity
- Inspect and replace any worn components promptly
- Check and adjust conveyor incline as needed to maintain optimal flow
With proper care, our gravity roller conveyors typically provide 5-10 years of reliable service, representing an excellent return on investment for material handling operations of all sizes.
Frequently Asked Questions
What is the optimal incline for a gravity roller conveyor?
The ideal incline typically ranges between 2-5 degrees, depending on package weight and surface characteristics. Heavier items require less incline (closer to 2 degrees), while lighter packages may need steeper slopes (up to 5 degrees) to move efficiently.
Can gravity roller conveyors handle turns or curves?
Yes, gravity roller conveyors can incorporate curves using specialized curve sections. Turns may require additional slope to maintain momentum, and proper side guards should be installed to keep packages on track through curved sections.
What maintenance does a gravity roller conveyor require?
Maintenance is minimal, consisting primarily of regular inspection of rollers for smooth rotation, cleaning of surfaces, occasional lubrication of bearings, and checking frame connections for stability. No electrical maintenance is required.
How do I determine the right roller diameter for my application?
Choose based on product weight and bottom surface characteristics. Heavier items typically require larger diameter rollers (50mm vs. 38mm), while items with small or irregular bottoms need closer roller spacing. The 50mm option provides better support for most applications.
What is the typical return on investment for gravity roller conveyors?
Most operations see ROI within 6-12 months through reduced labor costs, improved throughput, and energy savings. The absence of electrical components also reduces maintenance expenses substantially compared to powered systems.
Conclusion
As a trusted gravity roller conveyor manufacturer, we provide robust, efficient material handling solutions that optimize workflows while minimizing operational costs. Whether you’re streamlining warehouse operations, enhancing manufacturing processes, or improving distribution efficiency, our gravity roller conveyor systems deliver exceptional performance and value.
The combination of durability, flexibility, and cost-effectiveness makes gravity roller conveyors an essential component in modern material handling systems. With proper selection and implementation, these versatile systems will continue to serve as the backbone of efficient material movement for years to come.
Our commitment as a leading gravity roller conveyor supplier extends beyond providing quality products – we offer expert consultation, customization options, and reliable support to ensure your material handling needs are met with precision and care.
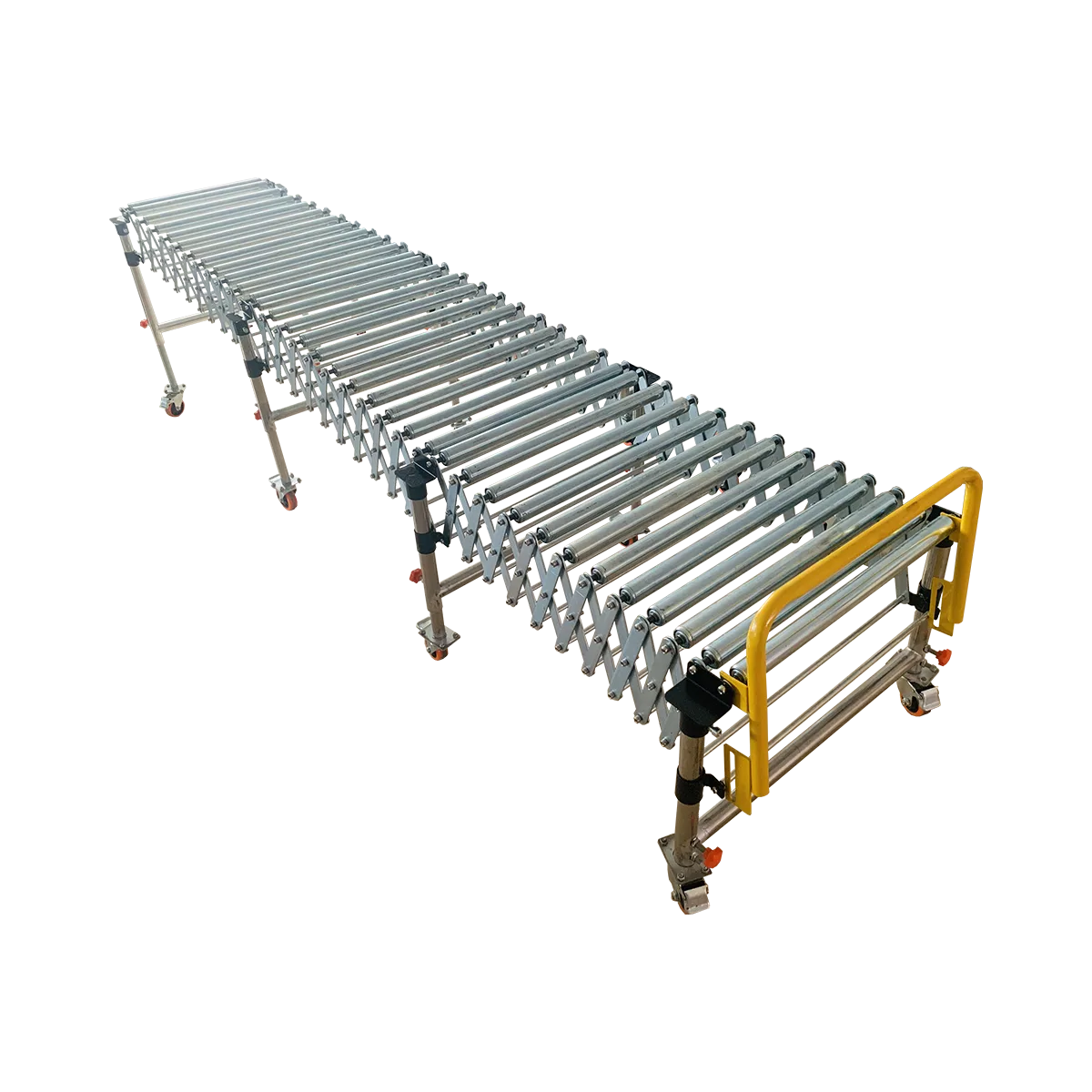
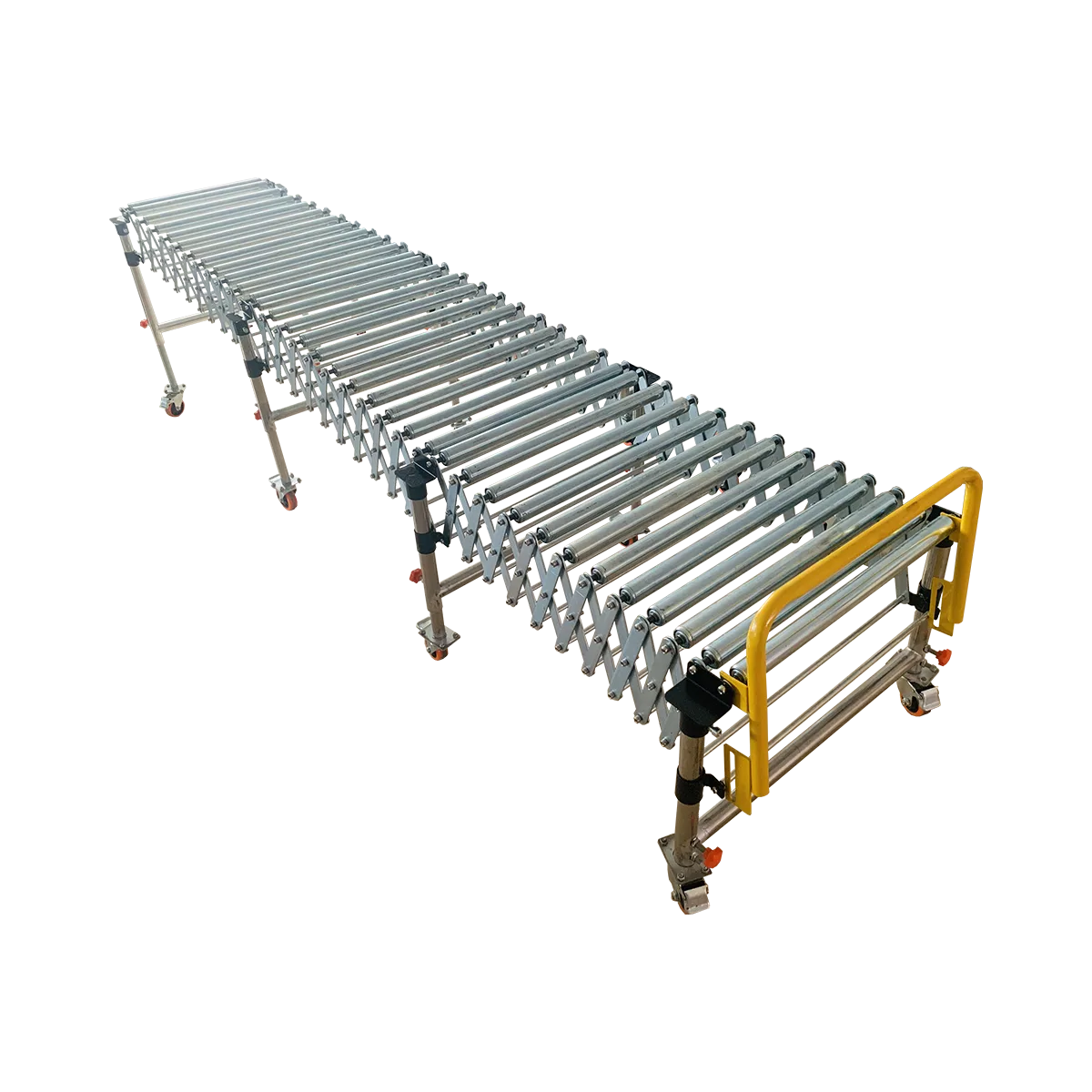