Hydraulic Conveyor Manufacturer
Home > Hydraulic Conveyor
Watch packages travel smoothly from ground level directly into truck beds or upper warehouse levels—hydraulic conveyors make this vertical journey possible through advanced lifting technology.
Our Hydraulic Conveyor Products
7900 mm
80 kg/m
Flat-bottomed Goods
Bagged Goods
7000 mm
80 kg/m
Flat-bottomed Goods
Bagged Goods
5400 mm
80 kg/m
Flat-bottomed Goods
Bagged Goods
3700 mm
50 kg/m
Flat-bottomed Goods
Bagged Goods
Watch packages travel smoothly from ground level directly into truck beds or upper warehouse levels—hydraulic conveyors make this vertical journey possible through advanced lifting technology. Unlike fixed-height alternatives, these versatile systems adjust elevation automatically while maintaining continuous product flow throughout transition zones. Their unique combination of horizontal transport plus vertical adjustment capabilities solves challenging material handling problems where traditional conveyors fall short. Distribution centers, manufacturing facilities, logistics operations—all benefit tremendously from hydraulic conveyors’ ability transporting goods between different elevation points without interrupting workflow or requiring multiple handling steps.
Elevation Versatility Advantage
Facility managers choose hydraulic conveyors when operational workflows involve height transitions. These specialized systems offer several compelling advantages compared with standard material handling equipment:
Seamless Vertical Transitions
Hydraulic conveyors eliminate traditional elevation challenges through integrated lifting capabilities:
- Continuous product flow between different facility levels
- Eliminated manual lifting requirements between height transitions
- Smooth angle adjustments preserving package orientation
- Precise positioning matching exact truck bed or mezzanine heights
- Dynamic adaptation accommodating varying vehicle dimensions
Loading operations particularly benefit from this seamless transition capability. Workers position hydraulic systems precisely matching truck heights where products travel directly from facility floors into waiting vehicles without secondary handling requirements or manual lifting steps.
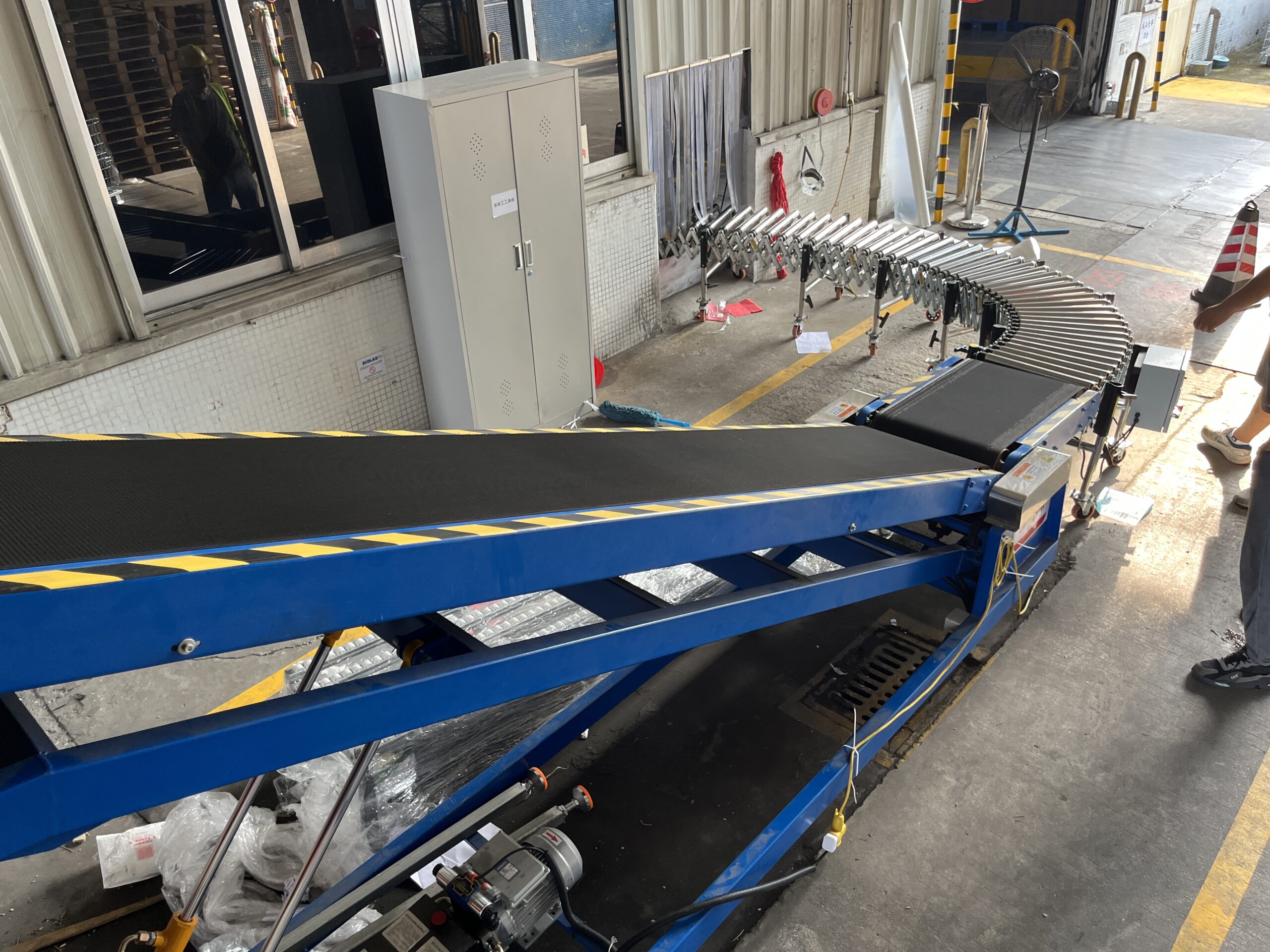
Space Optimization Excellence
Traditional incline conveyors require substantial horizontal distance creating gradual slopes between elevation points. Hydraulic systems dramatically reduce space requirements:
Feature | Space Advantage | Facility Benefit |
Vertical lifting capability | 60-70% less floor space | Increased operational area |
Compact footprint | Minimal installation requirements | Simplified layout planning |
Mobility with heavy-duty casters | No permanent placement needed | Flexible deployment options |
Integrated climbing sections | Self-contained height transition | Eliminated support requirements |
Adjustable positioning | Installation flexibility | Adaptable to facility constraints |
Warehouses with limited floor space particularly value these space-saving characteristics. Their operations maintain efficient material movement between elevations without sacrificing valuable facility square footage normally required for traditional incline conveyor installations.
Operational Flexibility
Few material handling systems match hydraulic conveyor adaptability across changing operational requirements:
- Adjustable incline angles accommodating various elevation needs
- Programmable height settings matching specific transfer points
- Mobile design supporting varying deployment locations
- Integrated controls providing operational customization
- Compatible extensions expanding functional capabilities
This remarkable flexibility makes hydraulic conveyors particularly valuable during variable operational scenarios when equipment must adapt toward changing material handling requirements without permanent infrastructure modifications throughout facilities.
Size Configurations and Applications
Different operational scenarios benefit from specific hydraulic conveyor configurations based on space requirements and performance expectations.
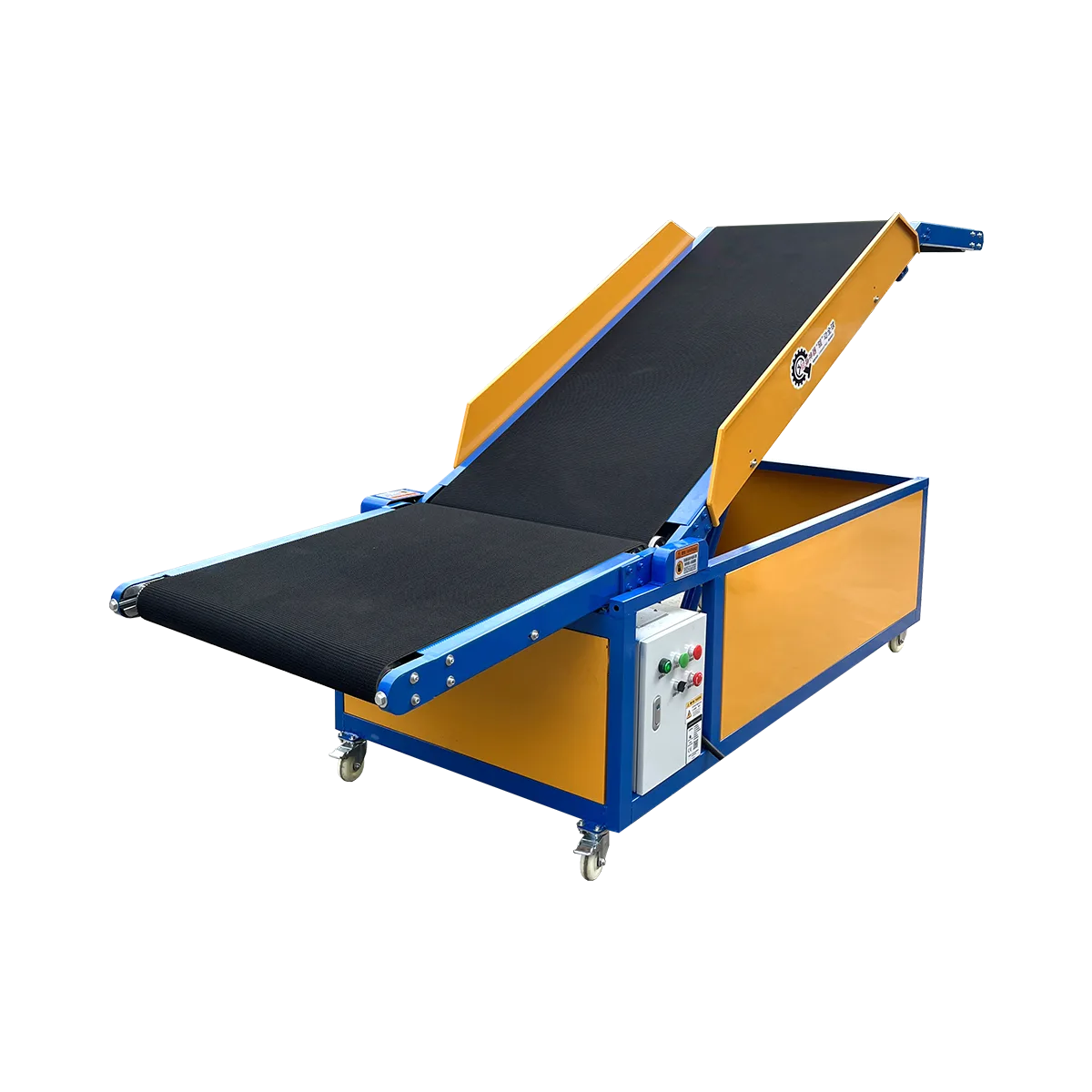
Micro Hydraulic Conveyor (3700mm)
This compact configuration delivers balanced performance within limited spaces:

Key Specifications:
- Overall length: 3700 mm
- Load capacity: 50 kg/meter
- Speed: 30 meters/minute
- Width options: 600/800 mm
- Weight: Approximately 380-480 kg
- Upper platform: 800 mm
- Climbing section: 2000 mm
- Lower platform: 1000 mm
Small distribution operations particularly value this configuration when loading standard delivery vehicles. Its compact dimensions allow deployment within limited spaces while maintaining sufficient capacity handling typical package dimensions throughout loading or receiving operations.
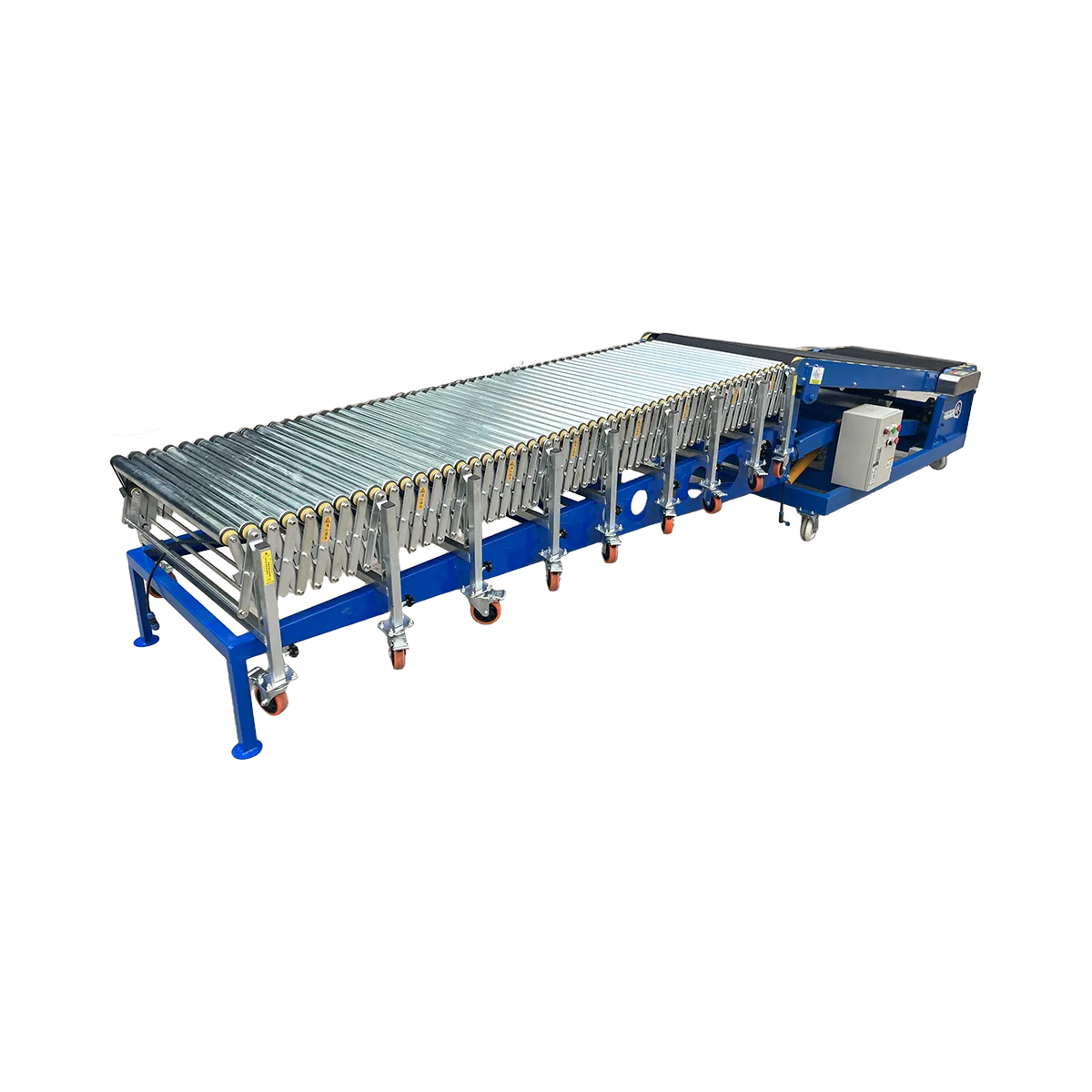
Small Hydraulic Conveyor (4000mm)
This popular mid-range system offers excellent performance balance:
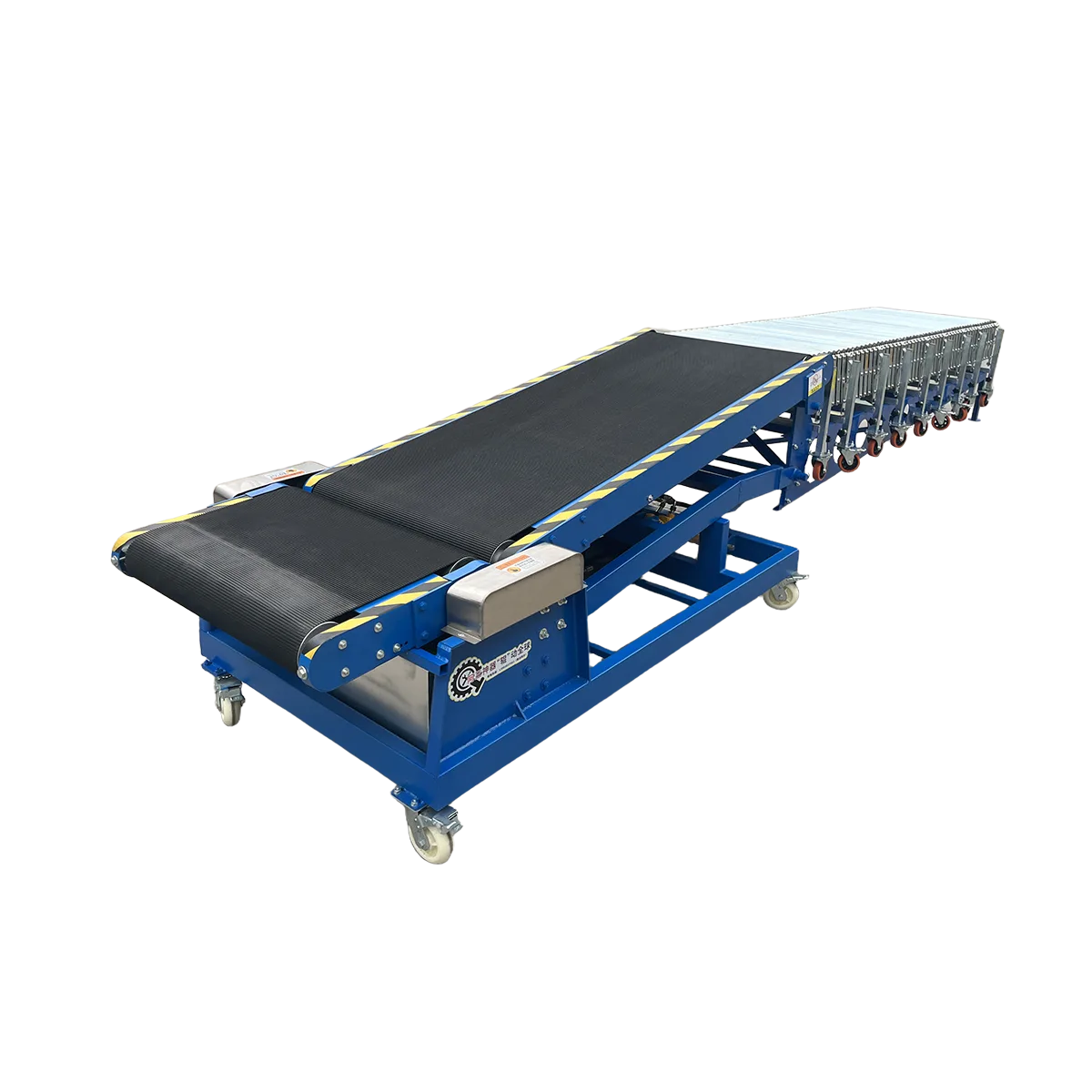
Key Specifications:
- Overall length: 4000 mm
- Load capacity: 80 kg/meter
- Speed: 30 meters/minute
- Width options: 600/800 mm
- Weight: 440-550 kg
- Climbing section: 2000 mm
- Lower platform: 500 mm
Retail operations frequently select this configuration creating flexible connections between storage areas and loading zones. Its balanced dimensions provide sufficient length handling typical transfer requirements while maintaining reasonable space utilization throughout facility deployment locations.
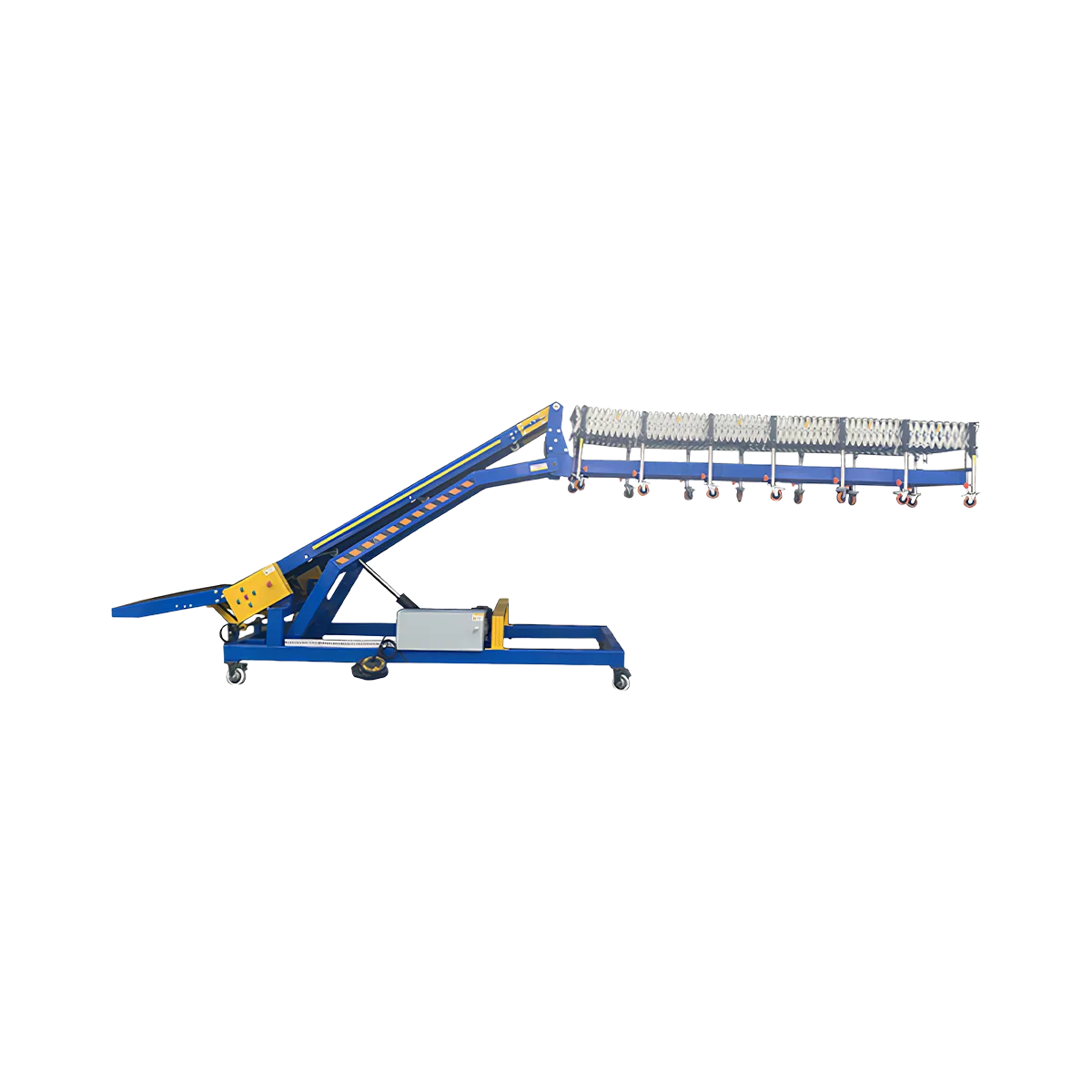
Medium Hydraulic Conveyor (7000mm)
Extended length provides enhanced operational capabilities:
Key Specifications:
- Overall length: 7000 mm
- Load capacity: 80 kg/meter
- Speed: 30 meters/minute
- Width options: 600/800 mm
- Weight: 540-650 kg
- Climbing section: 4000 mm
- Lower platform: 800 mm
Distribution centers benefit from this extended configuration when loading larger vehicles or connecting between separated operational zones. Its additional length creates comprehensive material handling pathways while maintaining vertical adjustment capabilities throughout extended transportation routes.
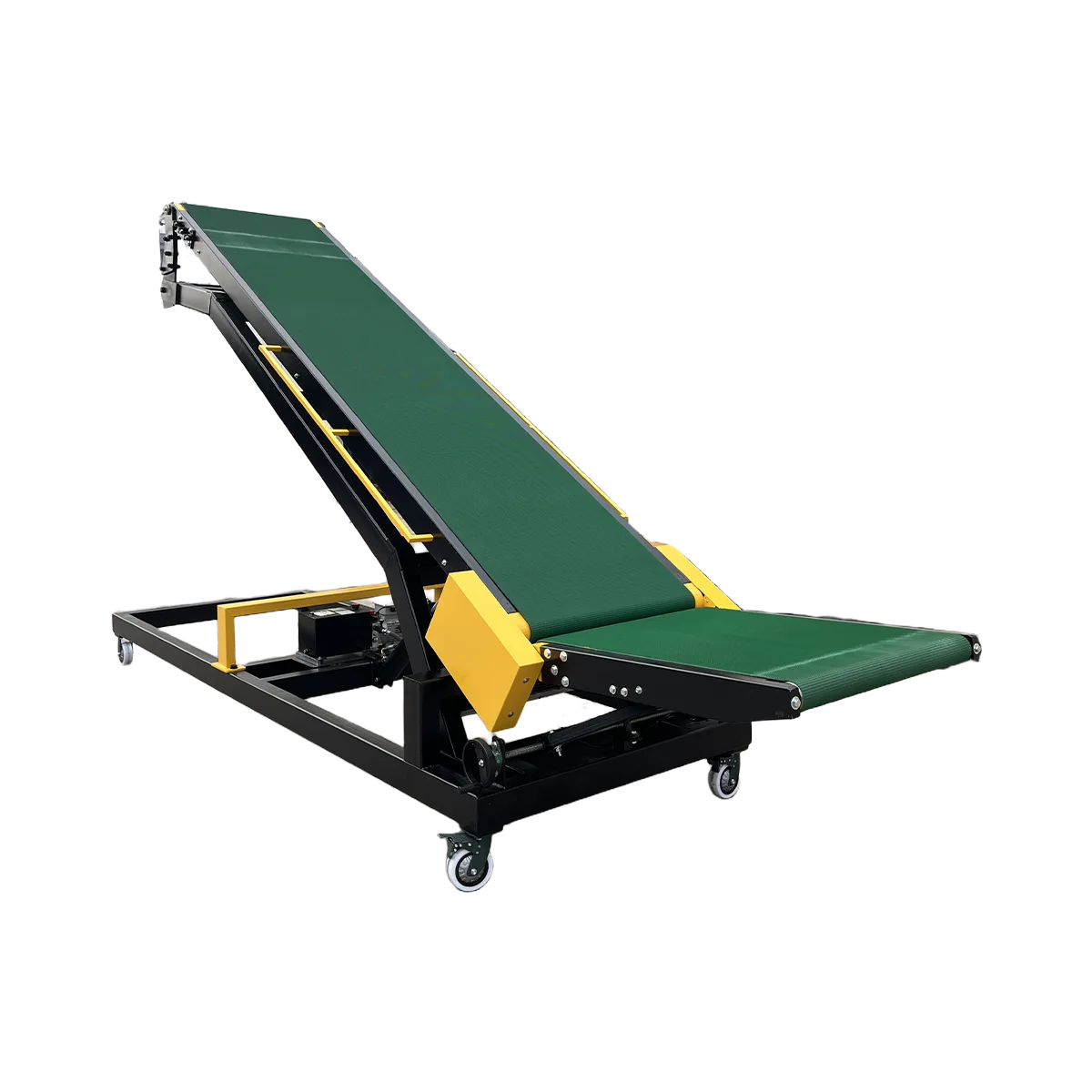
Large Hydraulic Conveyor (7900mm)
Maximum length delivers comprehensive material handling solutions:
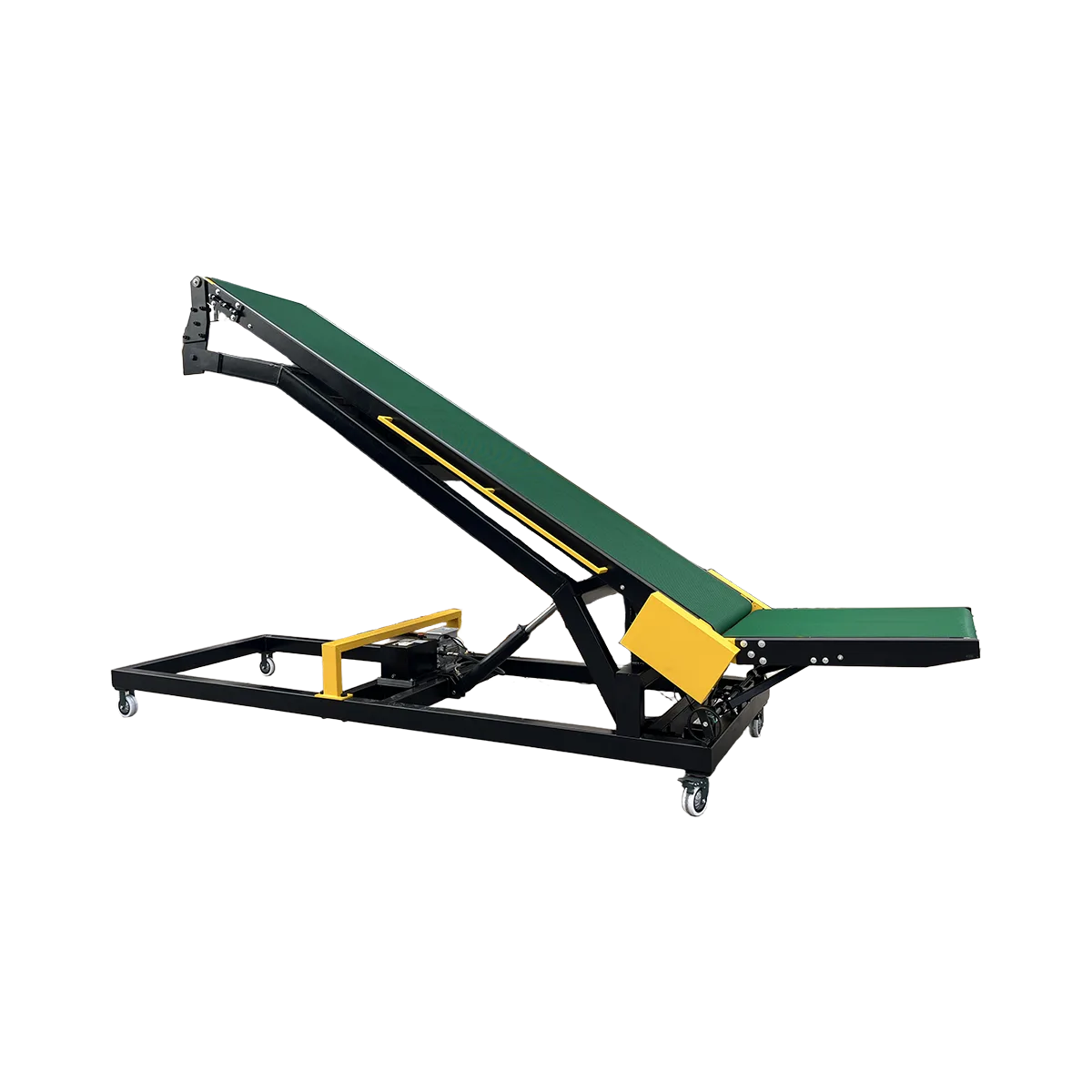
Key Specifications:
- Overall length: 7900 mm
- Load capacity: 80 kg/meter
- Speed: 30 meters/minute
- Width options: 600/800 mm
- Climbing section: 3000 mm
- Lower platform: 1100 mm
- Roller frame: 3500 mm
Logistics operations handling substantial volume requirements select this configuration creating extended transport pathways between processing zones. Its comprehensive dimensions provide maximum operational flexibility while maintaining impressive lifting capabilities throughout extensive facility layouts.
Advanced Technical Features
Hydraulic conveyors incorporate sophisticated engineering elements delivering reliable performance across demanding operational environments.
Powerful Lifting System
Robust hydraulic components ensure reliable height adjustment capabilities:
- Hydraulic cylinders with 5-ton thrust capacity
- Precision hydraulic pumps (YS90L-4 2.2kW)
- High-pressure hydraulic lines (53 MPa pressure resistance)
- Heavy-duty framework supporting elevation transitions
- Reliable control systems ensuring precise positioning
This engineering excellence creates dependable lifting performance regardless of load variations or operational demands. Maintenance teams appreciate component quality delivering consistent functionality throughout extended service periods within demanding material handling environments.
Anti-Slip Belt Technology
Specialized belt design ensures reliable product transport regardless of incline angle:
Technical Specifications:
- Material: PVC 5.0mm black grass pattern
- Surface texture: Anti-slip patterned design
- Durability: High wear-resistance characteristics
- Width options: 600/800 mm matching conveyor dimensions
- Drive method: Gear engagement (#60 chain)
This advanced belt technology prevents product slippage during elevation changes while maintaining consistent transportation speed throughout conveyor pathways. Operations handling diverse package types particularly value this reliable performance regardless of product weight or surface characteristics.
Comprehensive Control Systems
Sophisticated controls deliver precise operational management:
Control Feature | Operational Benefit | Application Example |
Forward/Reverse operation | Bidirectional material flow | Loading/unloading flexibility |
Lift/Lower functionality | Dynamic height adjustment | Vehicle height matching |
Emergency stop capability | Enhanced workplace safety | OSHA compliance |
Frequency converter adjustment | Speed optimization | Process synchronization |
Leakage protection | Electrical safety assurance | Operational protection |
These control elements transform sophisticated machinery into user-friendly material handling solutions. Operators maintain precise equipment management without extensive technical expertise while ensuring safe operational characteristics throughout daily utilization.
Extension Compatibility
Hydraulic conveyors gain additional functionality through seamless connection with complementary conveyor systems extending operational capabilities beyond integrated components.
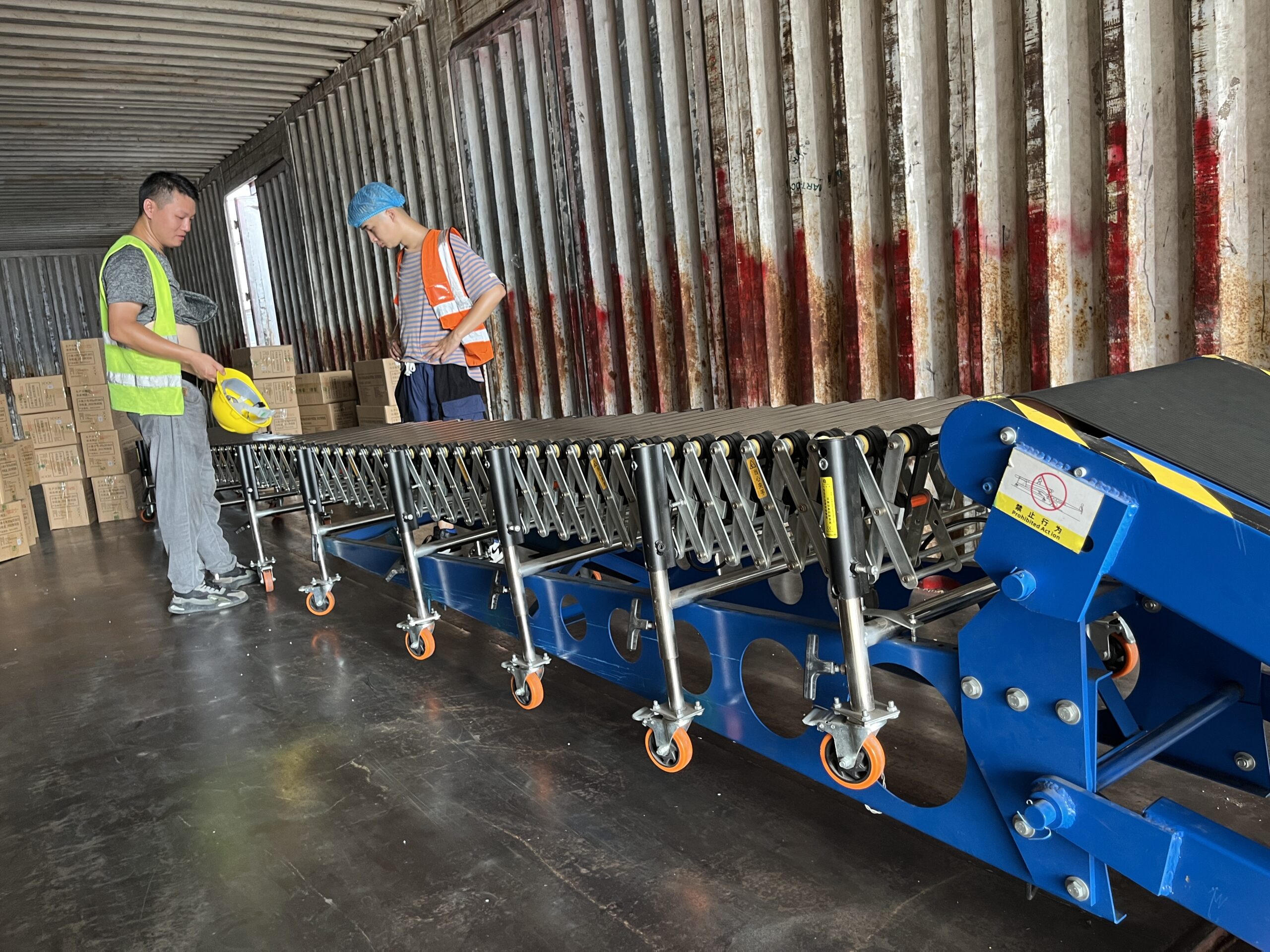
Compatible Extension Options
Various conveyor types connect directly with hydraulic systems creating comprehensive material handling networks:
Compatibility:
- Micro system: Supports up to 5 sections (10.5 meters extension)
- Small system: Supports up to 5 sections (10.5 meters extension)
- Medium system: Supports up to 6 sections (12.6 meters extension)
- Large system: Supports up to 9 sections (18.9 meters extension)
Compatibility:
- 38mm roller systems: 4-7 sections (6.8-13.6 meters extension)
- 50mm roller systems: 3-8 sections (4.5-12 meters extension)
Compatibility:
- Multi-wedge belt systems: 3-5 sections (6-10 meters extension)
- O-shaped belt systems: 4-8 sections (6-12 meters extension)
- Rubber roller systems: 4-7 sections (4.4-7.7 meters extension)
This remarkable integration capability creates comprehensive material handling solutions addressing diverse operational requirements through unified system configurations. Facility managers create custom material movement networks matching specific workflow requirements without compatibility concerns between different conveyor technologies.
Application-Specific Solutions
Different operational scenarios showcase hydraulic conveyor advantages through perfect alignment with specialized material handling requirements.
Vehicle Loading Excellence
Loading operations represent primary application zones for hydraulic conveyors through perfect alignment with operational requirements:
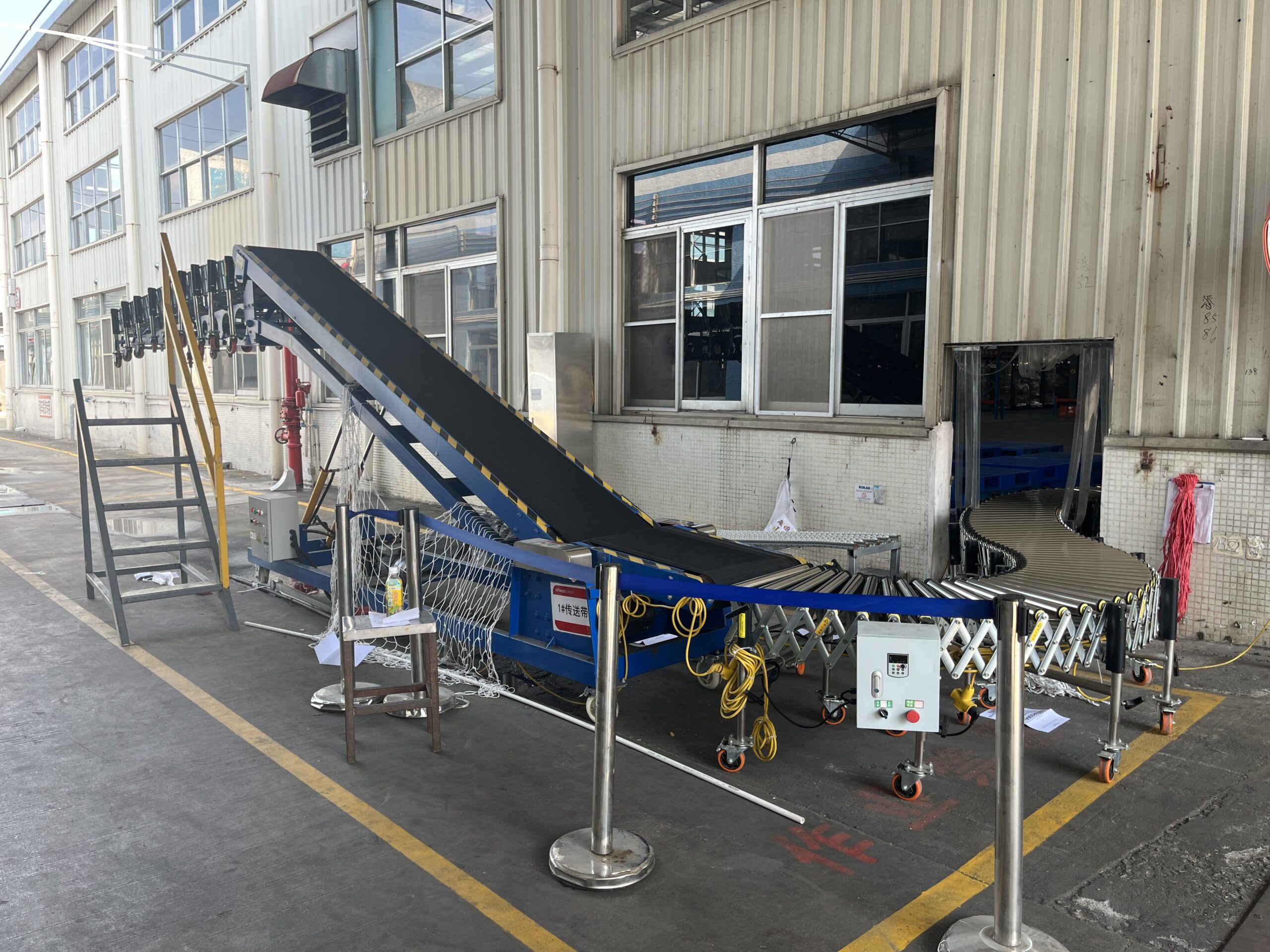
Truck Loading Operations benefit tremendously from hydraulic elevation adjustment. Their dynamic height positioning accommodates varied truck bed dimensions while maintaining continuous product flow throughout loading processes. Distribution centers report loading times reduced 40-50% after implementation compared with traditional methods requiring manual lifting or multiple handling steps.
Parcel Delivery Vehicles present various height requirements handling different vehicle models throughout daily operations. Hydraulic systems adjust precisely matching each specific configuration while maintaining efficient loading procedures regardless of dimensional variations between different vehicle types within delivery fleets.
Container Loading Applications utilize hydraulic positioning capabilities matching exact container floor heights. Logistics operations appreciate precise elevation adjustment ensuring perfect alignment while maximizing loading efficiency throughout international shipping preparation procedures.
Multi-Level Facility Integration
Buildings with vertical space utilization benefit significantly from hydraulic conveyor capabilities:
Mezzanine Connections establish efficient material movement between different facility levels without requiring permanent conveyor installations. Operations utilizing vertical storage space create flexible connections between elevated platforms and ground-level processing areas without dedicated infrastructure requirements.
Production Level Transitions in manufacturing environments maintain continuous product flow between different process elevations. Assembly operations establish seamless connections between varying production heights while preserving product orientation throughout vertical transitions between manufacturing stages.
Warehouse Level Changes become seamless through hydraulic adjustment capabilities. Distribution centers create efficient pathways between storage levels while maintaining product integrity throughout elevation transitions without secondary handling requirements normally associated with level changes.
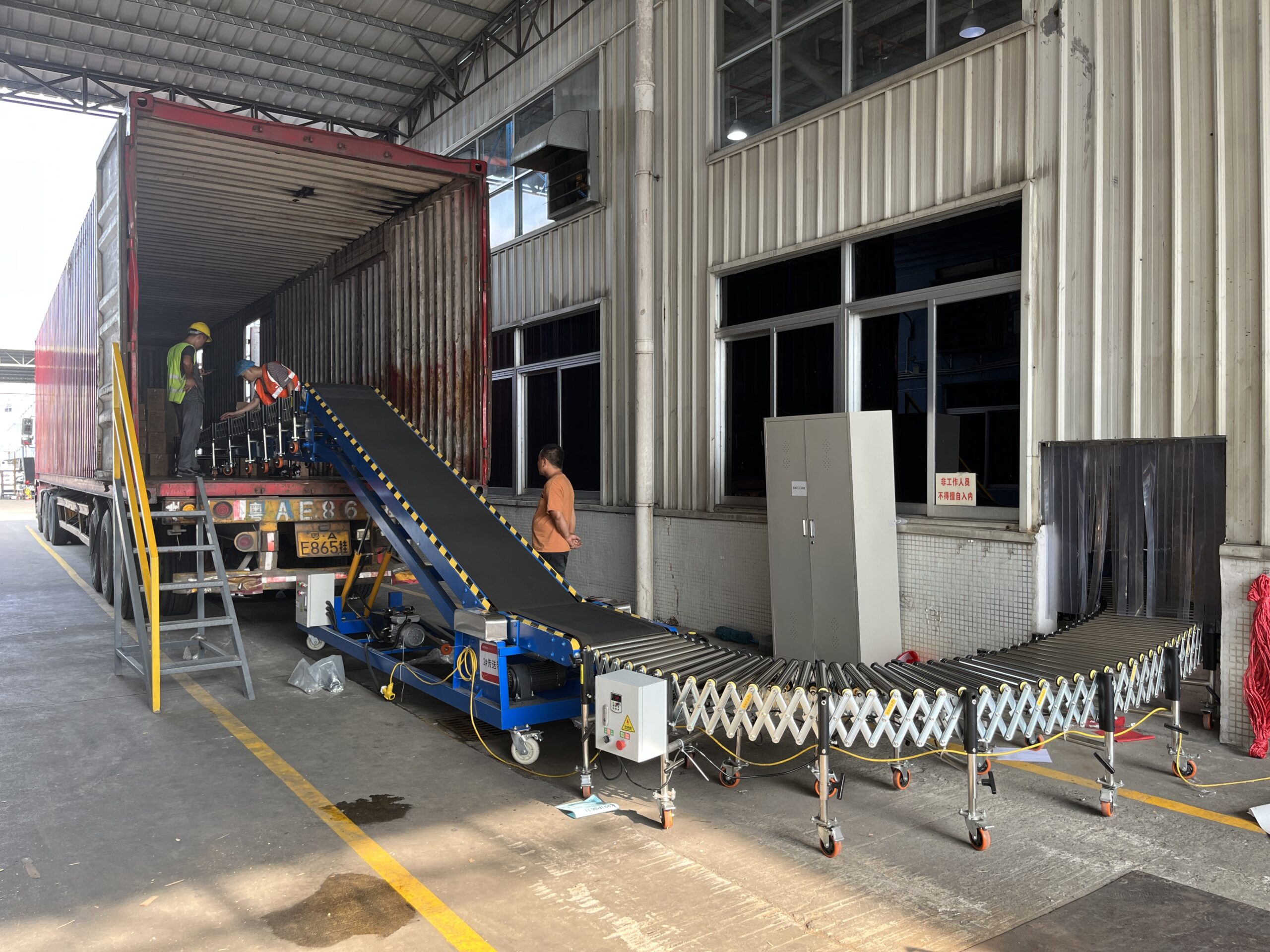
Specialized Material Handling
Certain operational challenges specifically benefit from hydraulic conveyor capabilities:
Heavy Package Handling benefits from robust construction handling substantial weights (80 kg/meter) without operational concerns. Manufacturing operations transport substantial components between production zones while maintaining reliable performance regardless of item weight variations throughout processing sequences.
Mixed Height Destinations become easily manageable through programmable elevation settings. Distribution operations establish efficient workflows between different processing heights while maintaining operational flexibility adapting toward changing facility requirements without equipment reconfiguration needs.
Loading Dock Flexibility accommodates various truck heights despite inconsistent vehicle dimensions. Logistics operations maintain efficient loading regardless of trailer variations while eliminating manual adjustment requirements normally associated with variable vehicle configurations.
Implementation Success Factors
Several key considerations ensure successful hydraulic conveyor implementation across diverse operational scenarios:
Infrastructure Preparation
Proper facility preparation ensures reliable operation throughout equipment lifecycle:
- Adequate electrical service matching specifications (220/380V)
- Sufficient floor reinforcement supporting substantial equipment weight
- Appropriate clearance envelope accommodating full operational movement
- Proper traffic pattern planning ensuring safe operational interaction
- Adequate maintenance access supporting preventative service requirements
These infrastructure elements support reliable operation while preventing implementation delays or operational limitations resulting from inadequate facility preparation before system deployment within material handling environments.
Operational Integration
Connecting hydraulic conveyors within existing workflows requires thoughtful planning addressing several operational factors:
- Process speed alignment coordinating with connected handling systems
- Transfer point optimization ensuring smooth product transitions
- Personnel training establishing proper operational procedures
- Maintenance scheduling preventing unexpected service interruptions
- Safety protocol development ensuring workplace protection standards
Comprehensive operational planning prevents workflow disconnects between different material handling components while ensuring seamless product flow throughout complete system configurations regardless of implementation complexity or technical characteristics.
Performance Optimization
Maximizing hydraulic conveyor benefits requires thoughtful calibration addressing specific operational requirements:
Adjustment Area | Optimization Approach | Performance Outcome |
Belt tension | Proper tension setting | Smooth product movement |
Lifting speed | Matched to workflow needs | Appropriate transition timing |
Incline angle | Application-specific setting | Optimal product handling |
Control response | Task-appropriate configuration | Precise operational management |
Extension integration | Smooth transfer alignment | Seamless material movement |
These adjustments transform standard equipment capabilities into precision-tuned material handling solutions. Operations teams customize system performance matching unique facility requirements while maximizing operational efficiency throughout daily utilization within distribution environments.
Maintenance Considerations
Regular preventative attention significantly extends equipment lifespan while ensuring consistent operational reliability throughout extended service periods.
Hydraulic System Maintenance
Proper hydraulic component care ensures reliable lifting performance:
- Regular fluid inspection verifying appropriate levels
- Filter replacement maintaining system cleanliness
- Cylinder inspection confirming proper operation
- Pressure verification ensuring optimal performance
- Connection examination preventing potential leakage
Most hydraulic maintenance requires specialized technical knowledge ensuring proper system functionality throughout operational lifecycle. Established maintenance schedules typically prevent unexpected failures while maximizing component longevity throughout equipment service periods.
Belt System Maintenance
Transport surface care ensures reliable product movement:
- Proper tension verification maintaining optimal operational characteristics
- Surface cleaning preventing debris accumulation
- Edge alignment confirmation ensuring tracking stability
- Drive component inspection verifying proper engagement
- Connection point examination preventing premature wear development
These maintenance procedures typically require minimal technical expertise while delivering significant performance benefits through consistent preventative attention throughout equipment service periods within material handling environments.
FAQ
What voltage requirements do hydraulic conveyors have?
Standard systems operate using 220/380V electrical service with appropriate circuit protection. Ensure your facility provides adequate power meeting these specifications before equipment deployment preventing electrical compatibility issues during operational implementation.
How quickly can hydraulic conveyors adjust between heights?
Typical systems complete full elevation adjustment within 20-30 seconds depending on specific model and loading conditions. This rapid transition allows efficient operational adaptation without significant workflow interruptions when switching between different height requirements throughout daily operations.
What maintenance do hydraulic conveyors require?
Regular preventative attention includes hydraulic fluid examination, belt inspection, roller verification plus control system testing maintaining optimal performance. Establish monthly inspection routines plus quarterly comprehensive service procedures ensuring reliable operation throughout equipment lifecycle while preventing unexpected operational interruptions.
Can hydraulic conveyors operate outdoors?
While designed primarily for indoor applications, systems function effectively within covered outdoor environments protecting electrical components from direct weather exposure. Consider adding protective covers when deploying within partially exposed locations ensuring reliable operation throughout varying environmental conditions.
What safety features do hydraulic conveyors include?
Standard systems incorporate emergency stop capabilities, leakage protection, mechanical safety locks plus operational warning indicators ensuring workplace safety throughout daily operation. These protective elements maintain operational protection while supporting OSHA compliance requirements throughout material handling applications within distribution environments.
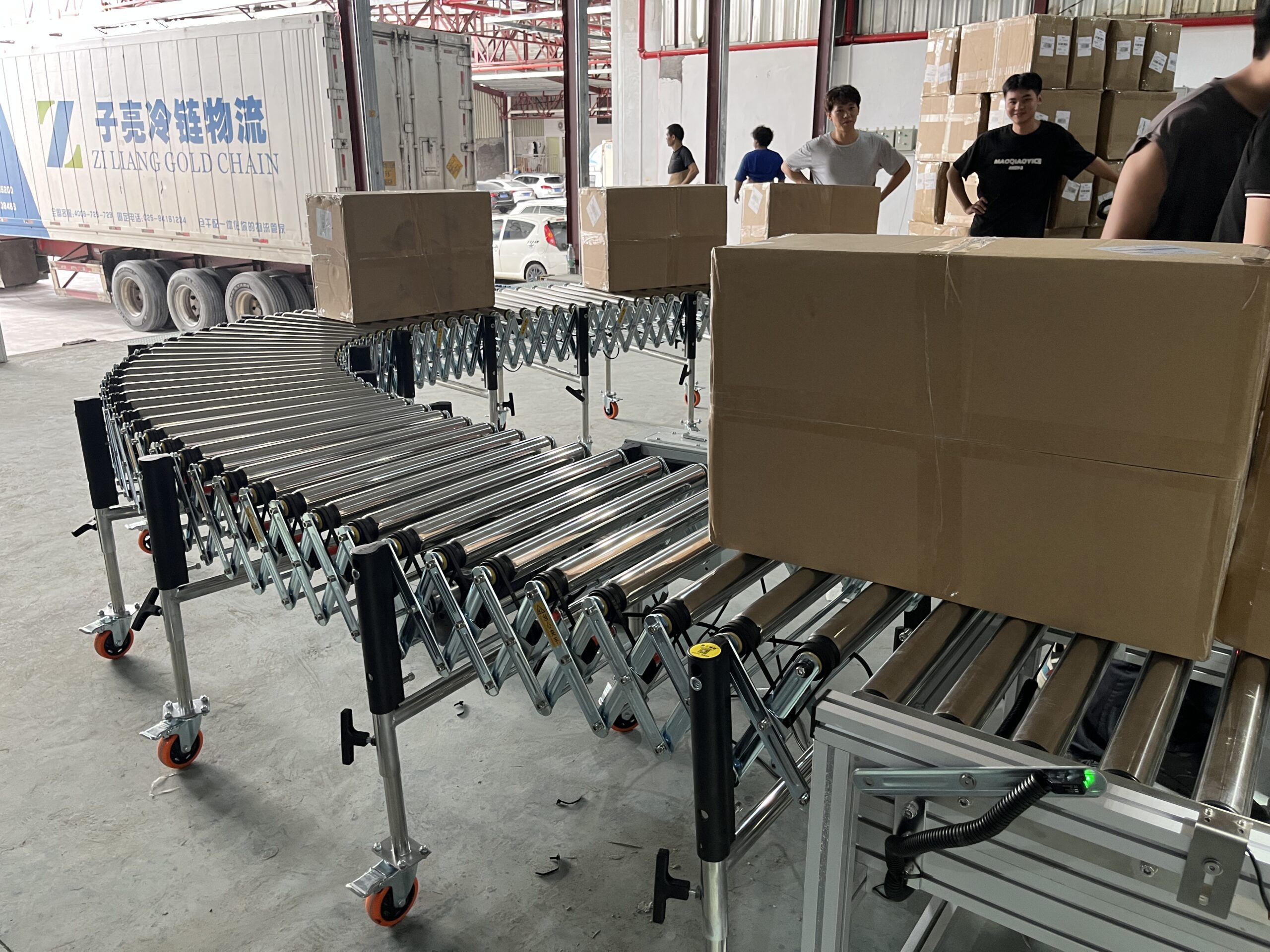