Gravity Conveyor Manufacturer
Home > Gravity Conveyor
Gravity roller conveyors harness Earth’s natural pull for moving products effortlessly across distribution spaces. These ingenious systems collapse for storage but expand dramatically when operations demand coverage.
Our Gravity Conveyor Products
420 mm
2100 mm
50 kg/m
Flat-bottomed Goods
525 mm
1500 mm
50 kg/m
Flat-bottomed Goods
Bagged Goods
485 mm
1700 mm
50 kg/m
Flat-bottomed Goods
Bagged Goods
Imagine products zooming across your warehouse floor without electricity, motors, or complex maintenance schedules! Gravity roller conveyors harness nature’s most reliable force—gravity itself—creating magical pathways where boxes dance effortlessly downhill. These deceptively simple systems transform chaotic warehouses into organized symphonies of movement while slashing operational costs dramatically. Available in various configurations including robust 50mm diameter rollers, sleeker 38mm versions and ultra-efficient skate wheel designs, Naili gravity conveyors deliver exceptional performance across countless applications. Each unit boasts impressive extension ratios—reaching up to 5:1 for skate wheel models—allowing facilities to maximize space utilization during operation yet collapse systems compactly when unused. Smart facility managers worldwide embrace this ancient-yet-modern technology for applications ranging from tiny package sorting through massive pallet transport operations. Each installation demonstrates how brilliantly effective simplicity becomes when thoughtfully applied toward complex material handling challenges.
The Magic Behind Gravity Power
Traditional conveyor systems gulp electricity constantly but gravity rollers demand absolutely nothing beyond proper installation. Their genius lies within thoughtful engineering rather than complicated mechanisms.
Slope Science Secrets
Products race or crawl depending entirely upon your desired setup! Most gravity systems thrive between 1.5° and 4° inclines—steeper angles accelerate boxes dramatically while gentler slopes maintain controlled steady movement. Heavier packages typically require less incline whereas lightweight items might need additional angle assistance. Engineers calculate perfect slopes through complex formulas considering:
- Package weights throughout your operation
- Surface texture interactions between products and rollers
- Distance requirements between workstations
- Speed limitations necessary for worker safety
- Transfer requirements between conveyor sections
Warehouse managers marvel at movement precision following proper installation! Products arrive exactly where needed at precisely calculated speeds without wasting precious energy resources.
Rollers That Rock Your World
Naili gravity systems feature various roller designs optimized for specific applications. The standard 50mm diameter option offers excellent durability while handling loads up to 50kg per meter, perfect for medium-duty applications. Meanwhile, lightweight 38mm rollers strike a brilliant balance between capacity and mobility with sleek profiles yet identical load ratings.
Roller Type | Diameter | Material Options | Best Applications | Unique Advantages |
Standard | 50mm | Galvanized/201 Stainless Steel | General warehousing | Perfect balance of strength and mobility |
Lightweight | 38mm | Galvanized/201 Stainless Steel | Space-constrained areas | Extended reach (1700mm vs 1500mm) |
Skate Wheel | 48mm | ABS engineering plastic | Package handling | Superior extension ratio (1:5) |
Material selection dramatically impacts performance capabilities! Stainless steel options excel within food processing environments requiring frequent sanitation procedures. Standard galvanized finishes provide excellent corrosion resistance at budget-friendly price points. Every configuration includes precision bearings ensuring smooth product flow throughout extended operational lifespans.
Frame Foundations Matter
Behind every successful gravity system stands solid framework supporting everything. Naili conveyors feature robust construction utilizing:
- Q345 steel frames withstanding industrial abuse year after year
- 201 stainless steel options resisting corrosion within harsh environments
- 3.5mm minimum thickness ensuring structural integrity under constant use
- Galvanized surface treatments providing economical protection against moisture damage
Frame design affects far more than durability alone! Thoughtful engineering creates systems accommodating future expansion needs without complete replacement requirements. Smart managers specify Naili’s adjustable leg supports allowing height modifications between 450-1500mm as operational requirements evolve throughout facility lifespans.
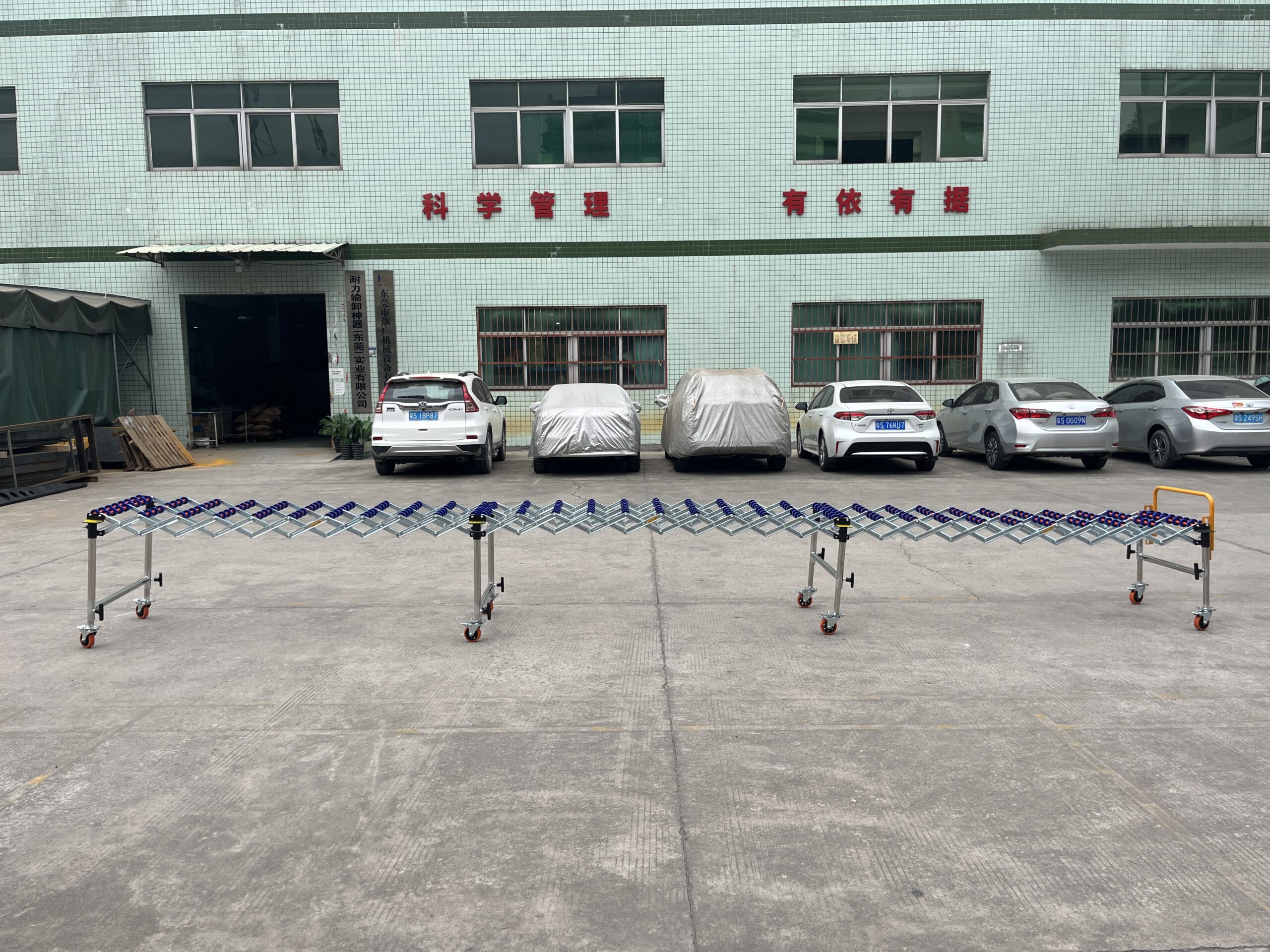
Applications That Transform Industries
Gravity conveyor technology adapts amazingly across numerous industries through thoughtful configuration adjustments. These versatile systems solve unique challenges while maintaining impressive simplicity.
Warehouse Wonders
Distribution centers worldwide revolutionize operations through strategic gravity deployment. Naili telescopic models create smooth connections between picking zones so products flow naturally toward packing stations. Workers accomplish substantially more daily tasks because walking distances shrink dramatically! Facilities report productivity jumps exceeding 40% following installation without hiring additional personnel.
Smart warehouse managers position gravity sections strategically throughout facilities creating “productivity islands” where associates concentrate entirely toward value-adding activities rather than wasteful product movement. This approach maximizes existing staff capabilities while minimizing operational costs dramatically.
Manufacturing Miracles
Factory environments benefit tremendously from controlled product movement between workstations. Gravity systems maintain perfect workflow timing without complex controls! Production managers appreciate how naturally products arrive exactly when needed without complicated scheduling mechanisms.
Assembly operations particularly value gentle handling characteristics preventing component damage during transport stages. Workers focus completely on manufacturing excellence rather than worrying about product transfer challenges. Quality improvements often accompany productivity gains through this enhanced concentration opportunity.
Cross-Docking Confidence
Products shouldn’t languish unnecessarily within distribution networks! Gravity systems create direct connections between incoming and outgoing shipments so merchandise flows continuously without stopping. Major retailers slash transfer times dramatically through thoughtful implementation strategies.
Loading dock operations transform completely following installation! Packages travel directly from receiving doors toward waiting vehicles without intermediate handling steps. Worker satisfaction improves substantially because physical demands decrease significantly while productivity soars simultaneously.
Picking Perfection
Order fulfillment operations thrive when properly equipped with gravity-powered assistance. Strategic zone design featuring inclined sections dramatically reduces walking requirements while maintaining perfect product orientation throughout movement. Facilities regularly report fulfillment rate improvements exceeding 35% following implementation!
- Workers concentrate entirely toward accuracy rather than transportation
- Products arrive naturally at packing stations without complicated controls
- Multiple orders progress simultaneously through parallel channels
- Fatigue factors diminish substantially throughout lengthy shifts
These benefits combine creating extraordinary productivity improvements without sophisticated technology investments. Simplicity delivers impressive results when thoughtfully applied toward operational challenges.
Gravity vs. Powered: Choosing Wisely
Facility managers frequently debate between gravity and powered roller options. Each technology brings unique advantages toward specific applications requiring thoughtful consideration.
Cost Considerations That Matter
Initial investments typically favor gravity systems substantially! Installation expenses generally run 40-60% lower compared with motorized alternatives depending upon specific configuration requirements. This dramatic difference allows smaller operations accessing professional-grade material handling solutions despite limited capital budgets.
Operational expenses reveal even greater contrasts over equipment lifespans! Consider these dramatic differences:
Expense Category | Gravity Systems | Powered Systems |
Electricity | None required | Constant consumption |
Maintenance labor | Minimal attention | Regular servicing |
Replacement parts | Rarely needed | Scheduled replacements |
Downtime costs | Nearly nonexistent | Periodic interruptions |
Training requirements | Extremely basic | Technical knowledge needed |
Lifetime operational savings often exceed initial purchase costs multiple times! Forward-thinking managers calculate total ownership expenses rather than focusing exclusively toward acquisition investments when evaluating options.
Speed Control Secrets
Powered systems allow precise velocity adjustments through simple controller modifications. This capability proves valuable for operations requiring exact timing between various process stages. Gravity alternatives rely upon incline adjustments providing somewhat limited flexibility once installed.
Motion consistency remains another important consideration! Powered rollers maintain identical speeds regardless whether moving empty containers or fully loaded pallets. Gravity alternatives accelerate heavier loads potentially creating workflow challenges requiring thoughtful planning before implementation.
Flexibility Factors
Operational changes sometimes demand equipment modifications addressing evolving requirements. Each technology approaches adaptation differently:
- Gravity systems typically require physical adjustments changing incline angles
- Powered alternatives often accept programming modifications without physical changes
- Section additions integrate more easily within motorized configurations
- Directional changes happen instantly with powered options but demand reconstruction with gravity
Growing operations particularly appreciate powered flexibility when frequent reconfiguration becomes necessary. Stable facilities typically value gravity simplicity because changes rarely occur following initial installation.
Environmental Impact Analysis
Sustainability considerations increasingly influence equipment decisions across industries. Gravity systems shine brilliantly within this category through:
- Zero energy consumption throughout operational lifespans
- Dramatically reduced manufacturing resource requirements
- Minimal maintenance waste generation
- Extended service lifespans often exceeding decades
- Simpler eventual recycling processes
Organizations emphasizing environmental responsibility increasingly favor gravity options when applications permit this technology choice. Their inherent efficiency aligns perfectly with modern sustainability initiatives without sacrificing operational performance.
Technical Specifications: Naili Gravity Conveyor Options
Naili offers multiple gravity conveyor configurations addressing diverse operational requirements across industries. Each model brings unique advantages toward specific applications.
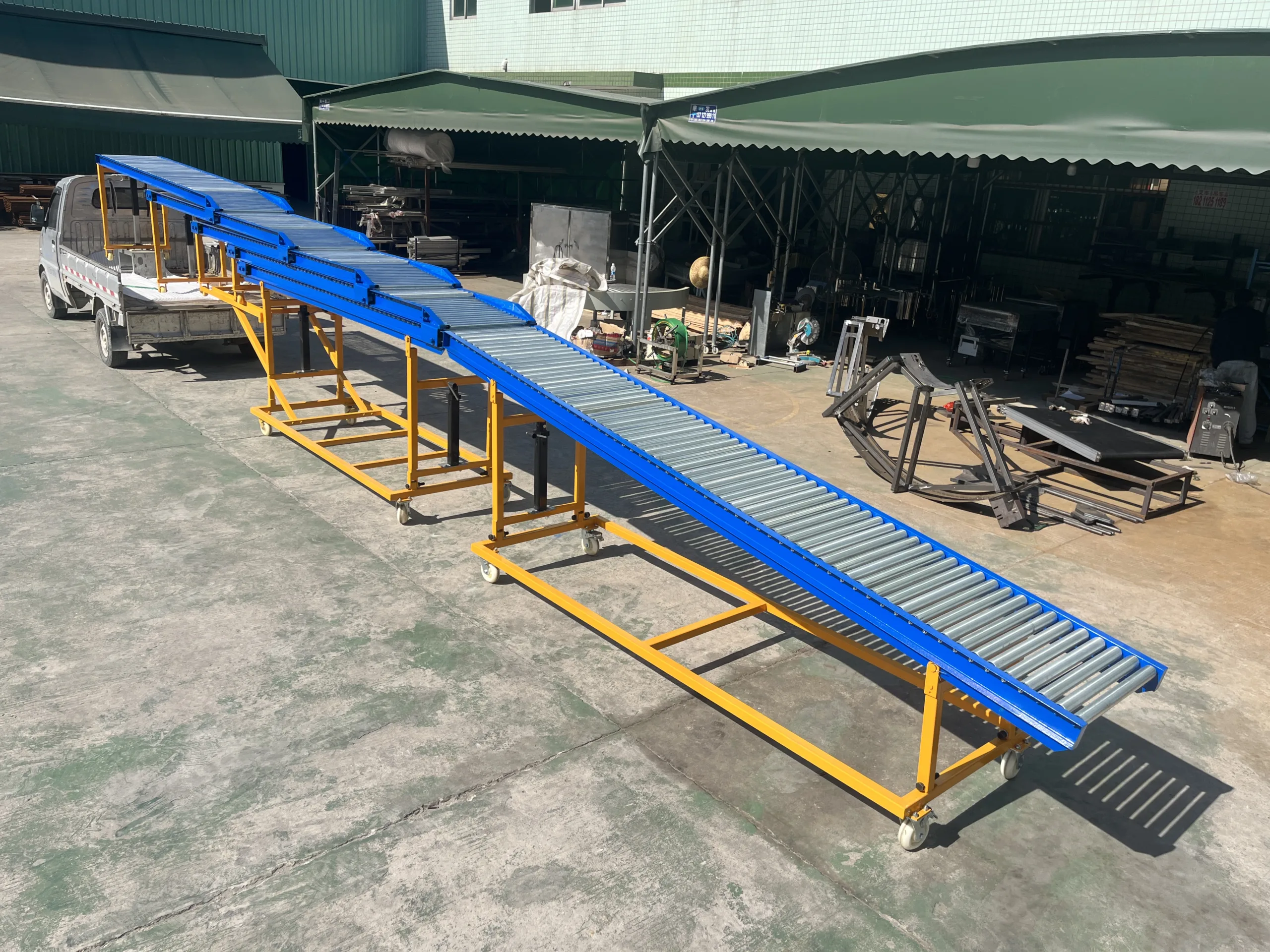
50mm Roller System: Robust Performance
This flagship model delivers exceptional durability through substantial components:
Specification | Details | Benefit |
Roller Diameter | 50mm with ≥1.5mm thickness | Supports heavier items without bending |
Extension | 525mm collapsed to 1500mm extended | 1:3 ratio maximizes space utilization |
Load Capacity | 50kg per meter | Handles medium-duty applications easily |
Frame | 35×35mm stainless steel | Provides excellent structural stability |
Available Widths | 500/600/800mm (custom available) | Accommodates various product sizes |
Weight | 26-39kg depending on width | Substantial without excessive heft |
These heavy-duty systems excel within demanding environments where durability matters most! Their robust construction withstands accidental impacts while maintaining perfect alignment throughout extended operational lifespans.
38mm Roller System: Extended Reach
When additional extension becomes necessary, these lightweight champions deliver impressive results:
Specification | Details | Benefit |
Roller Diameter | 38mm with ≥1.5mm thickness | Lighter profile with excellent durability |
Extension | 485mm collapsed to 1700mm extended | Greater reach within identical footprint |
Load Capacity | 50kg per meter | Matches larger system capacity |
Frame | 38×38mm stainless steel | Excellent rigidity despite lighter components |
Available Widths | 500/600/800mm (custom available) | Flexibility across applications |
Weight | 20-30kg depending on width | Easier handling during installation/reconfiguration |
Operations requiring substantial reach without sacrificing capacity appreciate these versatile systems! Their extended length creates longer transportation paths without additional sections—perfect within space-constrained environments.
Skate Wheel System: Ultimate Extension
When maximum expansion ratio becomes critical, skate wheel configurations deliver unmatched performance:
Specification | Details | Benefit |
Wheel Diameter | 48mm ABS engineering plastic | Smooth movement with minimal maintenance |
Extension | 420mm collapsed to 2100mm extended | Incredible 1:5 ratio maximizes usable space |
Load Capacity | 50kg per meter | Perfect for package handling applications |
Frame | 38mm diameter stainless steel | Excellent strength within lightweight profile |
Available Widths | 500/600/800mm (custom available) | Accommodates various product dimensions |
Weight | 14-22kg depending on width | Easiest handling among available options |
Package handling operations particularly value these ultra-flexible systems! Their extraordinary extension ratio creates impressive transportation spans while occupying minimal storage space when unused. International-standard 608 bearings ensure smooth operation throughout extended lifespans while requiring minimal maintenance attention.
Design Factors Ensuring Success
Effective gravity conveyor implementation demands thoughtful planning addressing numerous factors beyond simple incline calculations.
Space Utilization Mastery
Warehouse square footage costs money constantly! Efficient designs maximize available space through careful pathway planning. Experienced designers create systems flowing naturally around existing obstacles while maintaining perfect product movement throughout facilities.
Vertical space utilization offers particular advantages through multi-level configurations. Spiral segments connect different elevations beautifully while maintaining controlled descent speeds naturally. This approach dramatically increases throughput capabilities without expanding building footprints.
Ergonomic Excellence
Worker comfort translates directly toward productivity enhancements! Thoughtful conveyor positioning eliminates awkward reaching requirements while maintaining perfect working heights throughout processes. These seemingly minor considerations prevent repetitive strain injuries while simultaneously improving operational efficiency.
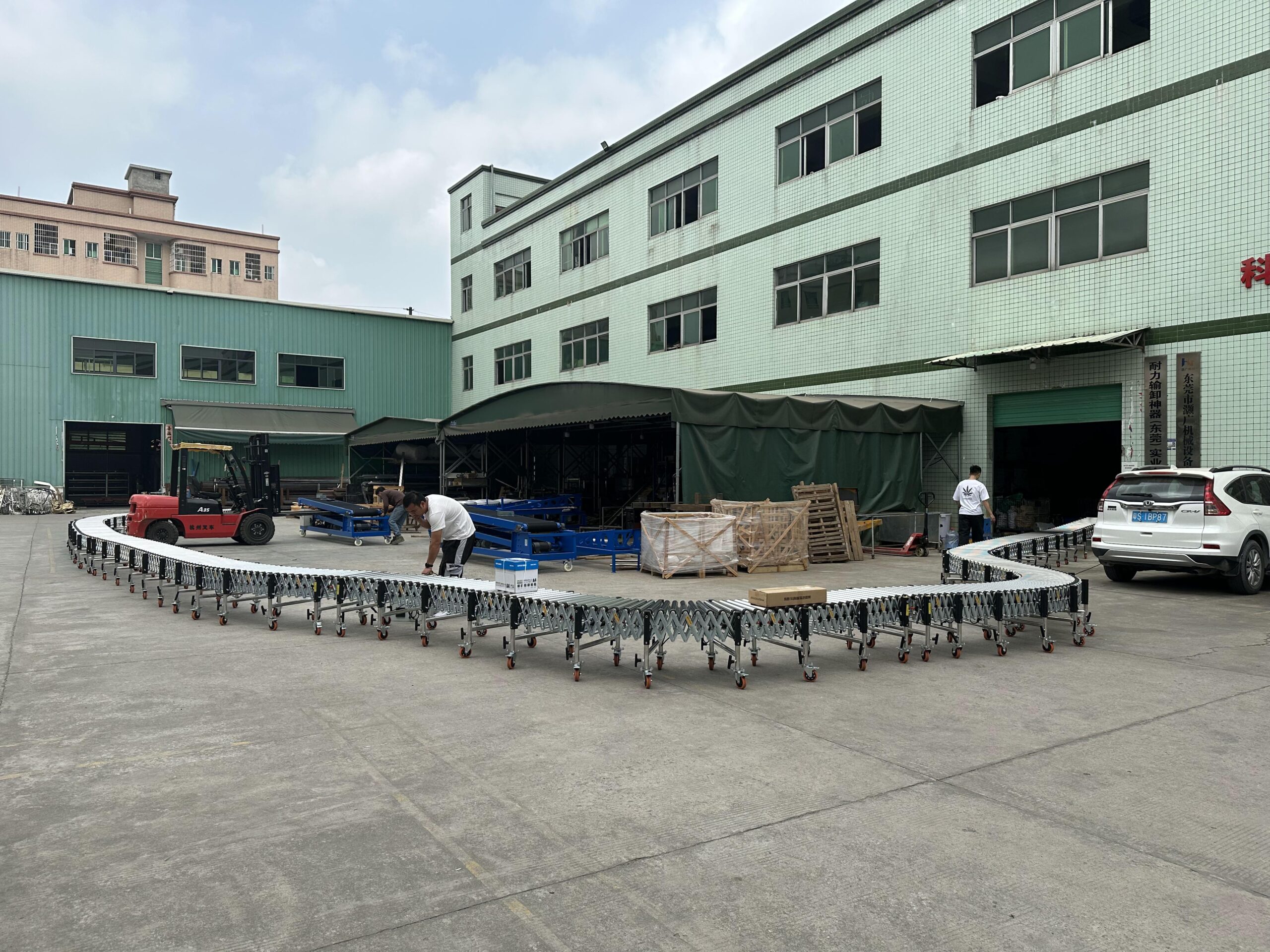
Height-adjustable sections accommodate various worker requirements without complicated mechanisms. Naili systems feature multiple adjustment ranges between 450-1500mm ensuring comfortable operation regardless of individual physical characteristics—an increasingly important consideration within diverse workforces.
Safety Considerations
Material handling equipment must prioritize operator protection above everything else! Gravity systems feature numerous safeguards preventing potential injuries:
- End stops prevent runaway packages reaching unprotected areas
- Side guards maintain product alignment preventing falls
- Braking sections control descent speeds within steeper applications
- Transfer plates eliminate dangerous gaps between conveyor segments
- Guarded rollers prevent accidental finger entrapment possibilities
These protective features combine creating remarkably safe operational environments despite continuous material movement throughout facilities. Management teams appreciate reduced incident rates following proper implementation.
Specialized Applications Showcasing Versatility
Beyond general warehousing, gravity conveyors adapt toward numerous specialized requirements through thoughtful configuration adjustments.
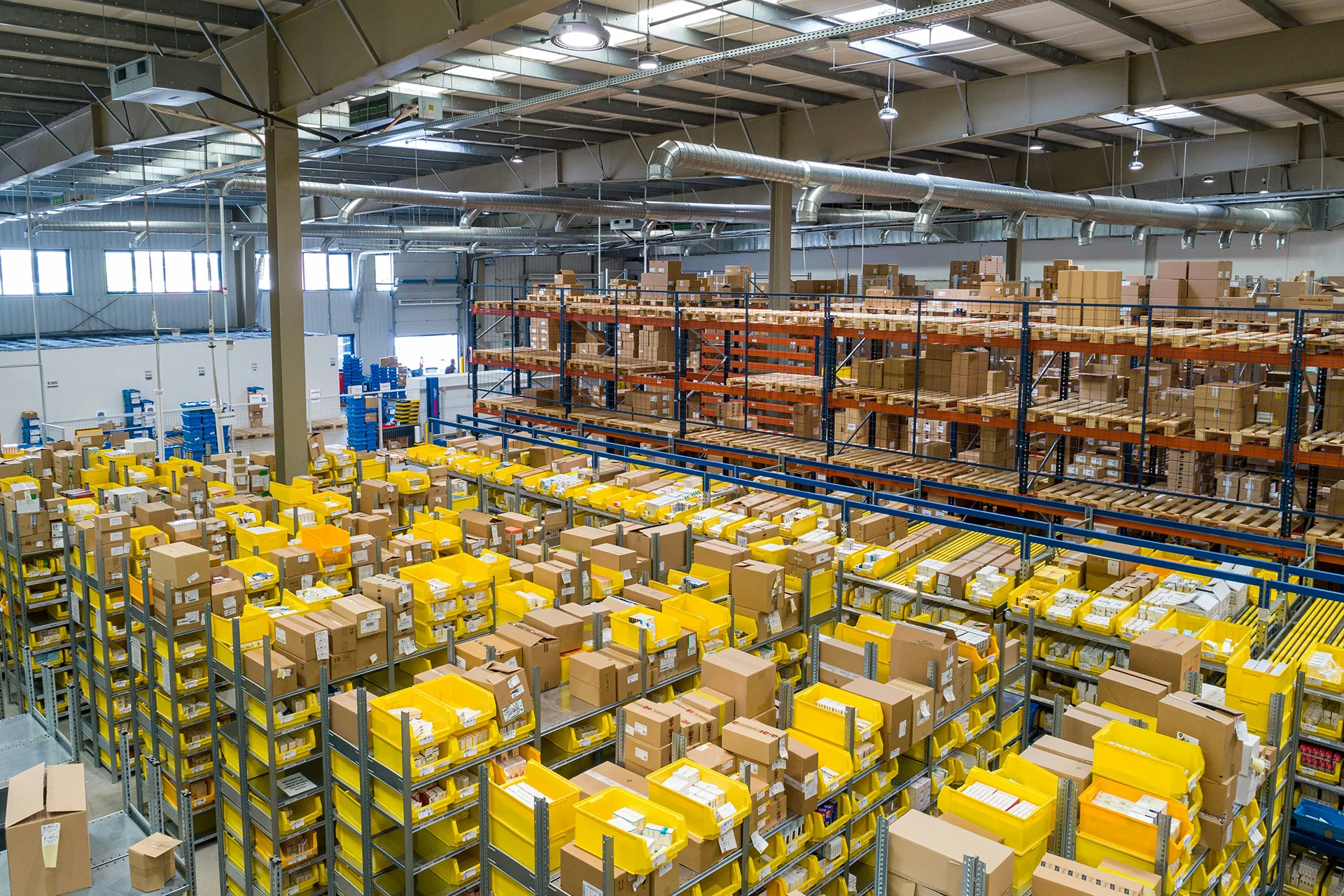
Food Processing Friendliness
Sanitation standards create unique challenges within food handling environments. Specialized gravity systems feature:
- Stainless steel components resisting corrosion during washing procedures
- Tool-free roller removal allowing thorough cleaning access
- Solid surfaces replacing open frames preventing debris accumulation
- FDA-approved materials throughout food contact zones
- Sloped frames facilitating complete drainage following sanitization
Processing facilities appreciate how quickly these systems return toward operation following cleaning procedures. Minimal components translates directly toward reduced contamination risks throughout production processes.
Cold Storage Champions
Freezer environments punish equipment mercilessly! Standard conveyors surrender quickly but specialized gravity systems thrive through:
Feature | Benefit |
Low-temperature lubricants | Maintains smooth operation at -30°F |
Sealed bearings | Prevents moisture infiltration during temperature changes |
Corrosion-resistant materials | Withstands condensation challenges beautifully |
Minimal moving parts | Reduces potential failure points dramatically |
No electrical components | Eliminates condensation-related shorts entirely |
Cold storage operators report exceptional longevity following proper installation! These specialized systems frequently deliver decades reliable service despite punishing environmental conditions challenging lesser equipment daily.
Retail Ready Solutions
Store environments demand equipment balancing functionality against aesthetic considerations. Gravity conveyor options specifically designed for retail applications feature:
- Clean architectural finishes matching store décor elements
- Quiet roller designs eliminating disrupting operational noise
- Compact configurations maximizing available selling space
- Mobile options allowing overnight repositioning flexibility
- Customer-friendly protective features preventing accidents
Back-room operations particularly benefit through receiving configurations efficiently processing deliveries without excessive space requirements. Stock rooms transform from chaotic storage areas toward organized processing centers through thoughtful implementation strategies.
Maintenance Magic: Almost None Required!
Unlike complex motorized alternatives demanding constant attention, gravity systems provide refreshingly minimal maintenance requirements throughout impressive operational lifespans.
Simple Service Schedules
Most gravity installations thrive with remarkably basic attention schedules:
- Monthly visual inspections checking alignment stability
- Quarterly roller cleaning removing accumulated debris
- Semi-annual bearing lubrication ensuring smooth operation
- Annual frame inspection verifying structural integrity
- Occasional roller replacement addressing eventual wear patterns
These minimal requirements typically consume less than four hours annually per hundred feet installed! Maintenance teams appreciate this efficiency particularly compared against motorized alternatives demanding weekly service attention throughout smaller installations.
Troubleshooting Simplicity
When occasional challenges arise, gravity systems present refreshingly straightforward diagnostic opportunities. Most performance issues stem from just three potential causes:
- Alignment shifts creating unwanted resistance points
- Debris accumulation between roller components
- Bearing lubrication depletion following extended operation
Technicians appreciate how quickly normal operation returns following simple adjustments! Complex diagnostic equipment becomes completely unnecessary throughout typical service procedures—another substantial advantage compared against powered alternatives requiring specialized tools and training.
Longevity That Impresses Everyone
Quality gravity systems frequently deliver decades reliable service despite minimal maintenance attention! Facilities regularly report 15-20 year lifespans following installation—sometimes exceeding building renovation cycles completely. This extraordinary durability creates remarkable return-on-investment calculations when evaluated against shorter-lived alternatives.
Frame components typically outlast roller elements completely! Thoughtful designs allow selective component replacement addressing wear patterns without complete system replacement requirements. This modular approach minimizes lifetime operational costs while maximizing sustainability advantages simultaneously.
Integration Excellence Across Operations
Modern facilities rarely rely upon single technology solutions addressing complex material handling requirements. Gravity conveyors integrate beautifully across diverse equipment ecosystems through thoughtful planning.
Powered System Partnerships
Hybrid configurations combine gravity and powered sections creating optimized material flow throughout facilities. These intelligent combinations position powered components exclusively where absolutely necessary while utilizing gravity everywhere else possible. This approach minimizes energy consumption while maintaining operational efficiency throughout processes.
Transfer sections create seamless connections between different technologies so products flow naturally throughout facilities without manual intervention requirements. These integration points eliminate traditional bottlenecks while maximizing throughput capabilities across diverse system components.
Sortation System Connections
Distribution operations frequently require product routing toward various destinations based upon specific characteristics. Gravity systems create perfect feeding mechanisms delivering products consistently toward automated sorting equipment. This partnership approach maximizes expensive sortation investments while minimizing overall system costs effectively.
Manual sorting operations benefit similarly through multi-lane gravity configurations. Simple diverter mechanisms allow operators routing products toward appropriate channels without complicated controls or extensive training requirements. Throughput capabilities frequently double following implementation compared against previous manual methods.
Workstation Integration
Assembly operations thrive when components arrive precisely when needed within perfect orientation. Gravity sections deliver materials directly toward workstations maintaining ideal positioning throughout movement. Workers accomplish tasks substantially faster because parts positioning eliminates wasteful reorientation requirements before processing begins.
Adjustable height sections accommodate diverse workstation designs without complicated mechanisms. This flexibility ensures perfect ergonomic integration regardless of application requirements or worker characteristics throughout facilities.
FAQ
Does gravity conveyor work for every material handling application?
Nope! Works brilliantly for most boxed products, containers with flat bottoms and many palletized loads but struggles with extremely light items, round objects without containment or products requiring precise speed control throughout movement.
What maintenance headaches should I expect?
Almost nothing! Occasional bearing lubrication, periodic roller cleaning and alignment checks about covers everything. Most systems run trouble-free for years with minimal attention.
Can gravity systems handle oddly shaped packages?
Usually! Proper roller spacing accommodates most irregular shapes. Naili offers models with gaps ranging from 110-150mm addressing various product dimensions. Very unusual items might need containment trays which then travel smoothly across rollers beneath.
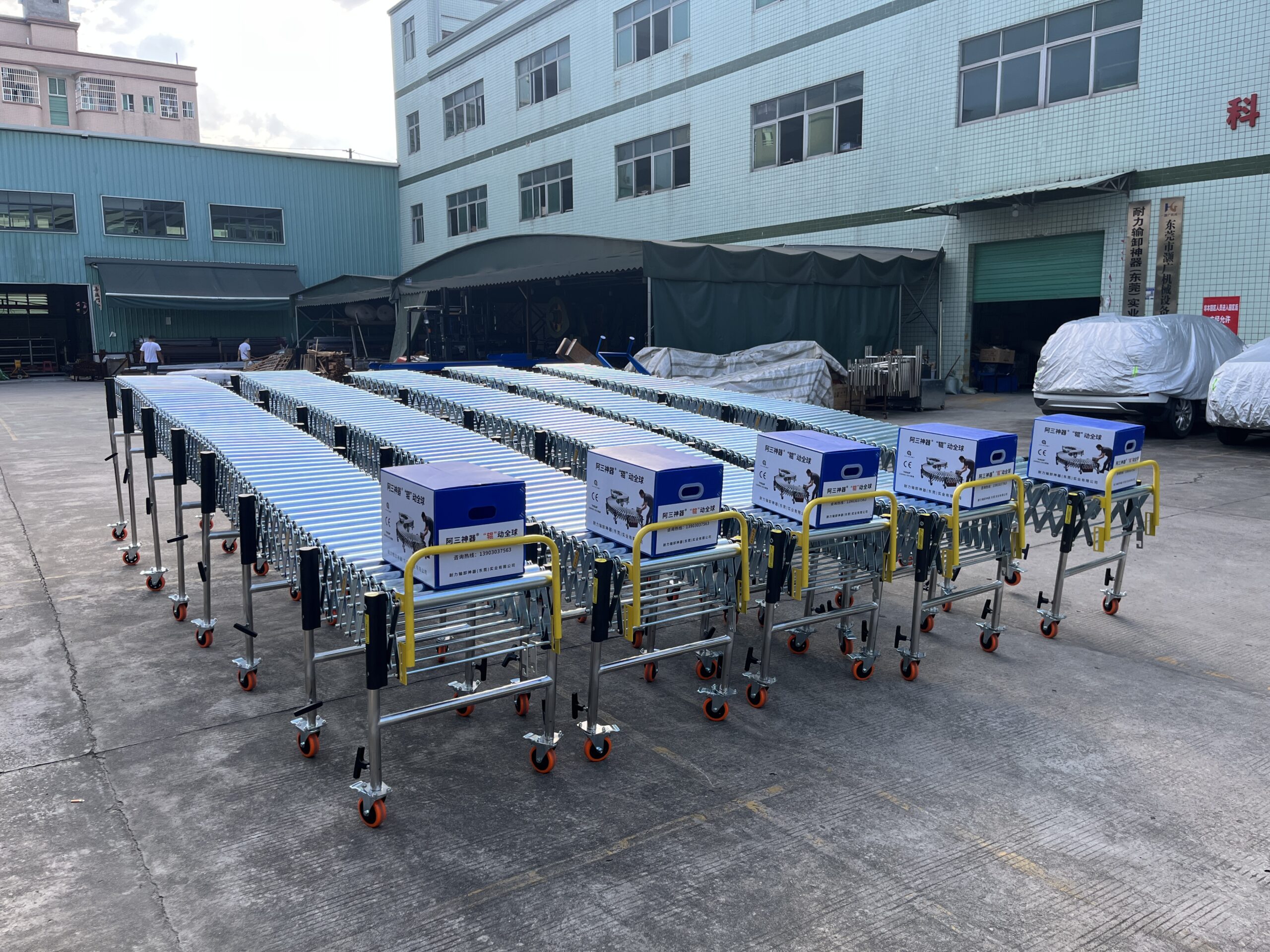
How long do gravity conveyors typically last?
Impressively long! Quality systems frequently deliver 15-20 years reliable service with minimal component replacement needs. Naili provides 12-month warranty coverage but most customers report substantially longer operational lifespans under normal conditions.
Will gravity conveyor speed work for my specific application?
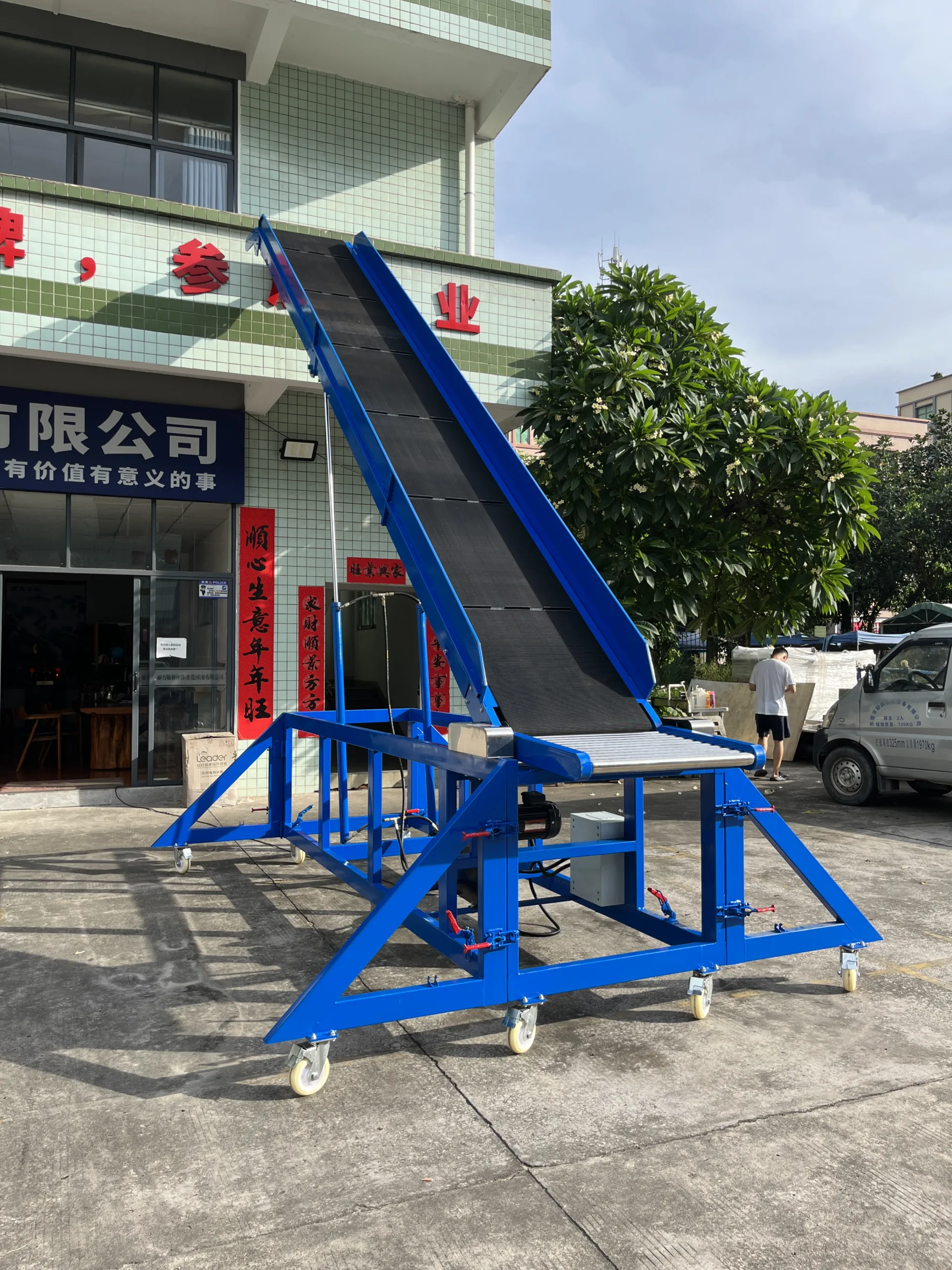
Probably! Incline adjustments create velocity ranging from crawling speeds through surprisingly swift movement. Testing with your specific products determines perfect angle requirements ensuring ideal flow characteristics.
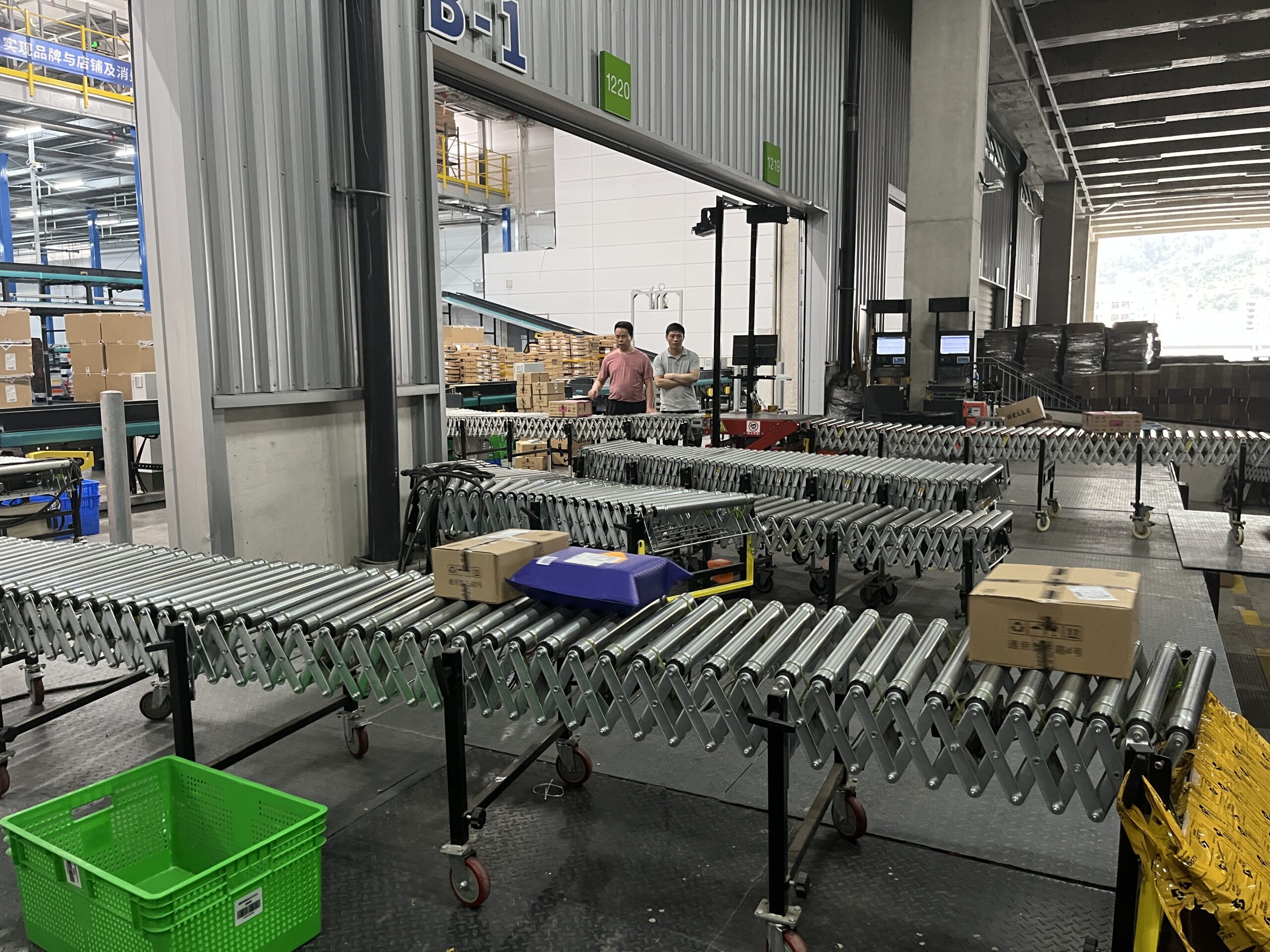