Manual Conveyor Manufacturer
Home > Manual Conveyor
Unlike powered alternatives requiring complex electrical components and ongoing energy consumption, manual conveyors harness simple physical principles to move products effortlessly throughout your facility.
Our Manual Conveyor Products
420 mm
2100 mm
50 kg/m
Flat-bottomed Goods
525 mm
1500 mm
50 kg/m
Flat-bottomed Goods
Bagged Goods
485 mm
1700 mm
50 kg/m
Flat-bottomed Goods
Bagged Goods
Optimize your material handling processes with efficient, cost-effective manual conveyor systems! Unlike powered alternatives requiring complex electrical components and ongoing energy consumption, manual conveyors harness simple physical principles to move products effortlessly throughout your facility. Naili’s comprehensive manual conveyor lineup includes precision-engineered gravity roller systems in multiple diameter configurations, innovative skate wheel designs, and telescopic options providing extraordinary extension capabilities. These versatile solutions deliver exceptional performance across warehouse, distribution, manufacturing, and retail applications while dramatically reducing operational costs. Each manual conveyor system features thoughtful engineering focused on durability, operational reliability, and seamless integration with existing material handling equipment—creating sustainable material flow pathways maximizing productivity without unnecessary complexity.
Gravity Roller Technology: Simple Engineering, Remarkable Results
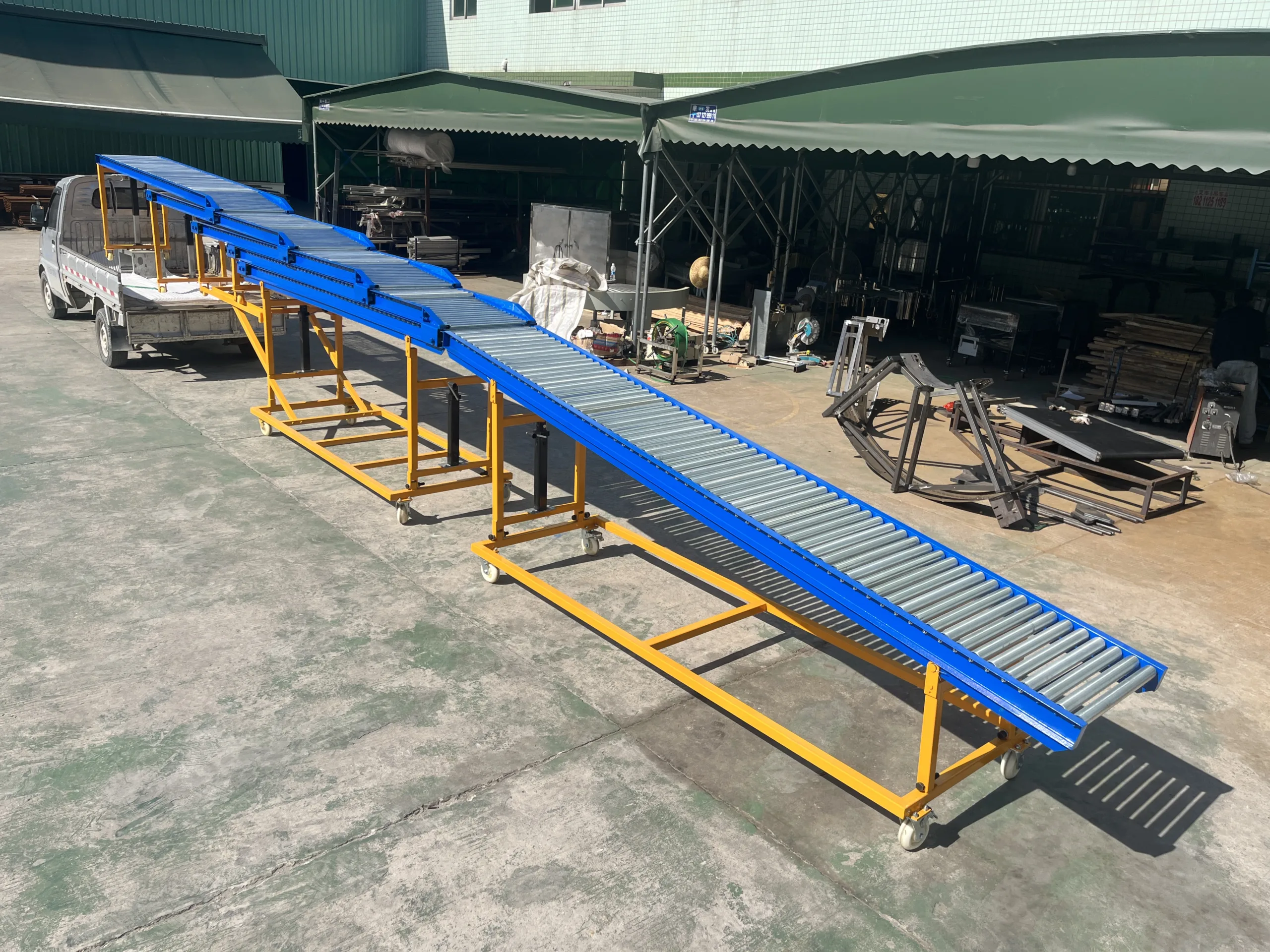
Gravity conveyor systems represent material handling’s perfect balance between simplicity and effectiveness. Their elegantly straightforward design delivers exceptional functionality through minimal components.
38mm Diameter Roller Systems: Extended Reach Excellence
Naili’s 38mm diameter gravity roller conveyors provide impressive extension capabilities through lightweight yet durable components:
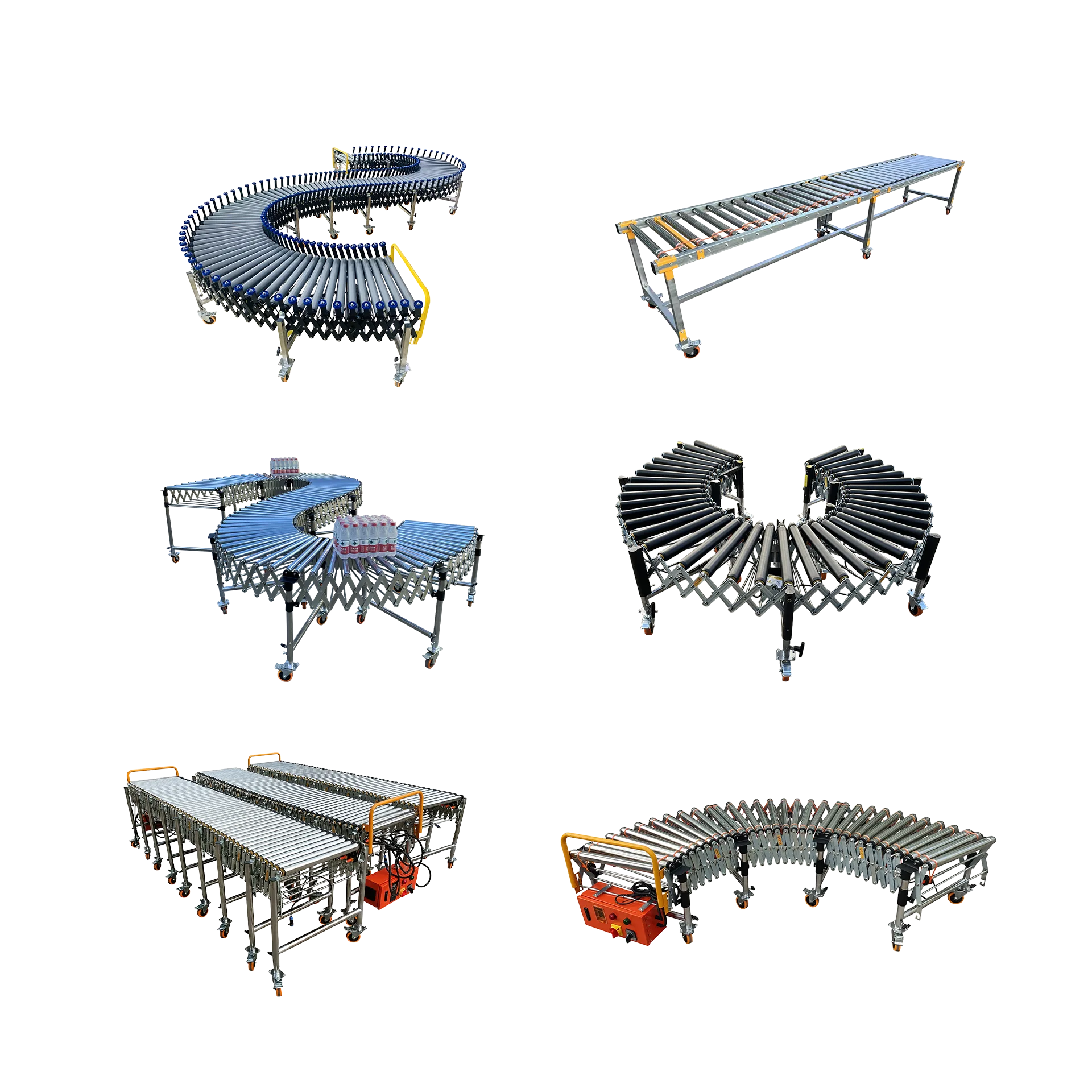
Feature | Specification | Benefit |
Extension Ratio | 1:3 (485mm collapsed to 1700mm extended) | Creates substantial operational reach from minimal storage footprint |
Load Capacity | 50 kg/m | Handles typical package transport requirements efficiently |
Roller Construction | 38mm diameter, ≥1.5mm thickness | Balances weight reduction with structural integrity |
Frame Construction | 38×38mm stainless steel | Provides excellent stability despite lightweight profile |
Roller Spacing | 150mm standard gap | Allows smooth transport for most package sizes |
These versatile manual conveyors excel within operations requiring maximum extension capabilities from minimal storage space. Their lightweight construction facilitates easy repositioning between workstations while maintaining necessary durability for daily operation.
Facility engineers appreciate the thoughtful design elements including adjustable height support legs (450-1500mm range) accommodating diverse operational requirements! This flexibility ensures perfect integration within existing processes regardless of specific facility characteristics.
50mm Diameter Roller Systems: Robust Performance
When durability becomes the priority, Naili’s 50mm diameter gravity roller conveyors deliver exceptional performance through substantial components:
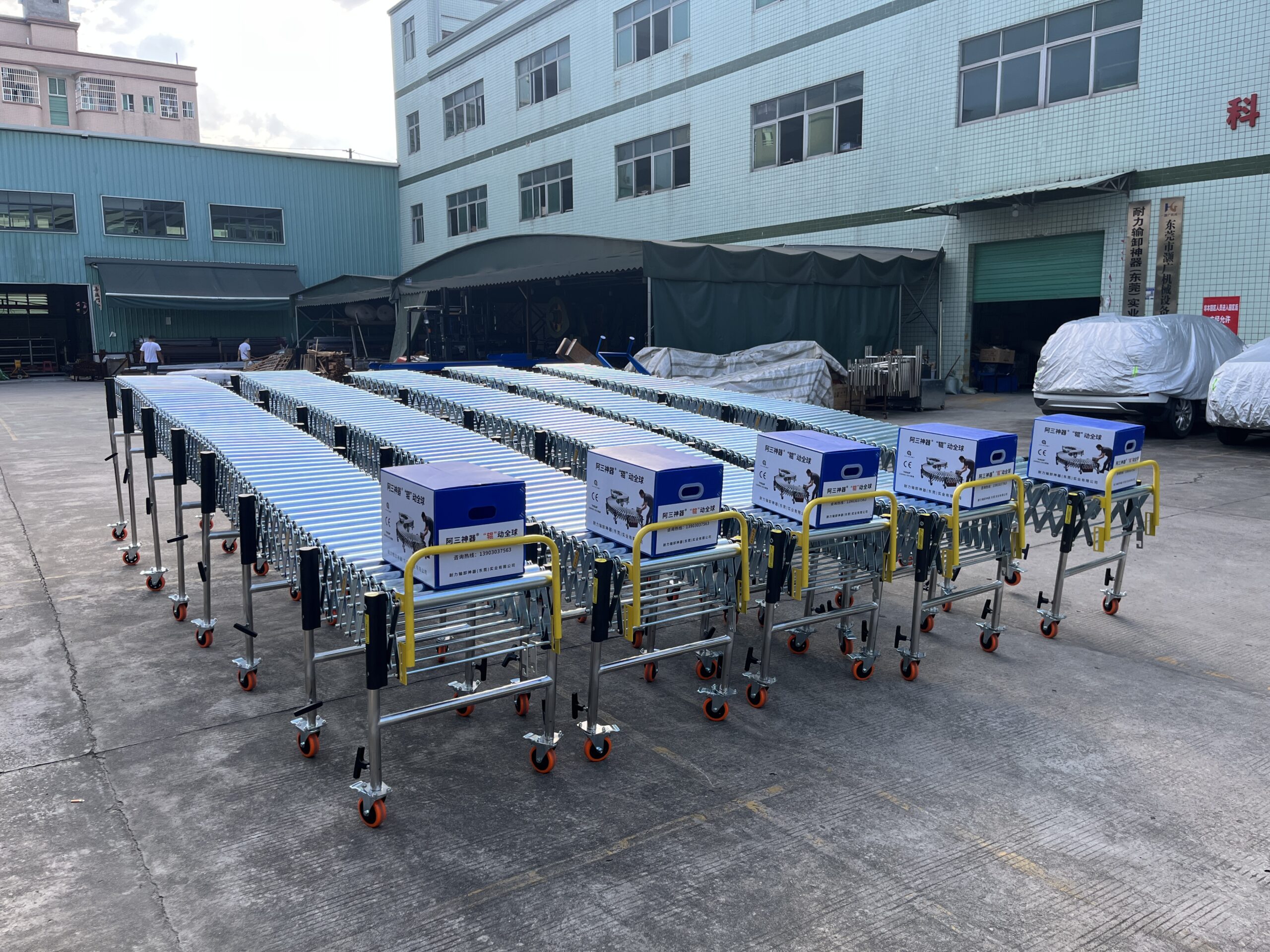
Feature | Specification | Benefit |
Extension Ratio | 1:3 (525mm collapsed to 1500mm extended) | Provides significant operational length from compact storage |
Load Capacity | 50 kg/m | Manages standard distribution requirements effectively |
Roller Construction | 50mm diameter, ≥1.5mm thickness | Offers improved durability for continuous operation |
Frame Construction | 35×35mm stainless steel | Delivers excellent stability during operation |
Roller Spacing | 110mm standard gap | Ensures smooth transport for smaller package sizes |
Operations handling continuous material flow particularly value these robust manual conveyors! Their substantial roller diameter provides excellent durability while maintaining optimal product transport characteristics throughout extended operational lifespans.
Warehouse managers report exceptional reliability following implementation! The minimal component design virtually eliminates maintenance requirements while delivering consistent performance throughout demanding operational environments.
Skate Wheel Conveyor Systems: Ultimate Extension Capability
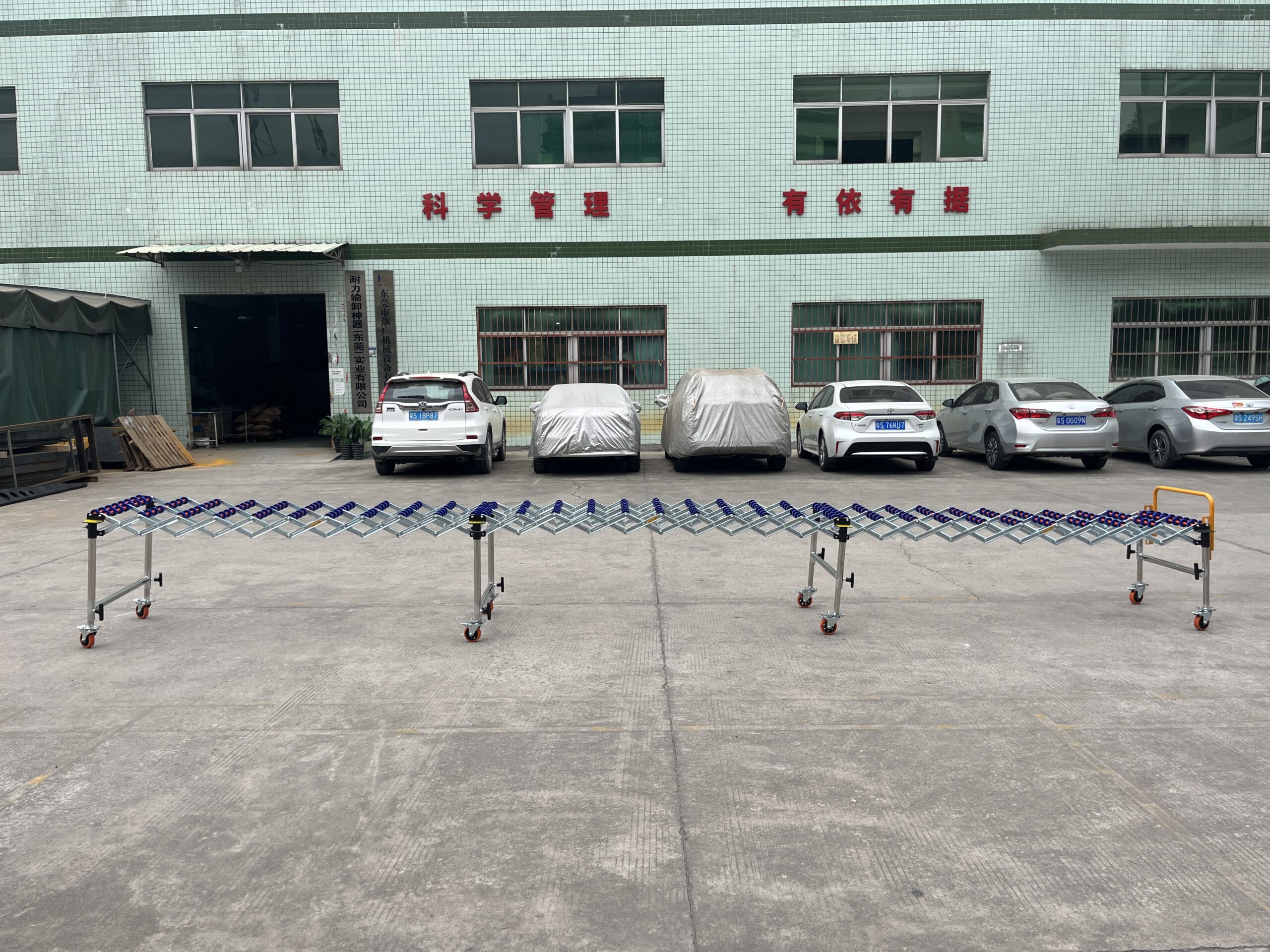
For applications requiring maximum extension from minimal storage footprint, Naili skate wheel manual conveyors provide unmatched performance through innovative design.
Impressive Engineering Efficiency
These remarkable manual conveyors transform compact storage configurations into extensive transportation pathways through intelligent engineering:
Feature | Specification | Benefit |
Extension Ratio | 1:5 (420mm collapsed to 2100mm extended) | Provides industry-leading extension from minimal storage requirements |
Load Capacity | 50 kg/m | Handles typical distribution center package weights |
Wheel Construction | 48mm ABS engineering plastic with 608 bearings | Provides smooth operation with minimal maintenance |
Frame Construction | 38mm diameter stainless steel | Ensures structural integrity despite lightweight design |
Wheel Spacing | 11 axles per section, 150mm spacing | Accommodates diverse package dimensions |
Distribution centers particularly value these ultra-compact manual conveyors when temporary material flow pathways become necessary! Their extraordinary extension ratio creates impressive operational reach while requiring minimal storage space during inactive periods.
Specialized Wheel Design
Behind skate wheel manual conveyor performance stands thoughtful component design optimized for specific operational requirements:
- ABS engineering plastic construction providing excellent durability with minimal weight
- 608 international standard bearings ensuring smooth rotation with extended service life
- One-piece injection-molded spacers maintaining perfect wheel alignment
- Galvanized steel axles preventing corrosion in variable environments
- 150mm standard spacing accommodating diverse package dimensions
These specialized components combine creating remarkably effective material handling systems despite mechanical simplicity. The elegant engineering approach demonstrates deep understanding regarding real-world application requirements within modern distribution environments.
Adaptable Configuration Options
Modern material handling frequently requires equipment adaptability addressing diverse operational requirements. Naili skate wheel manual conveyors accommodate these needs through numerous options:
- Multiple width configurations (500/600/800mm) handling various product dimensions
- Adjustable height support legs (450-1500mm) ensuring ergonomic positioning
- Stainless or carbon steel frame options addressing specific environmental requirements
- Custom section lengths available matching unique facility dimensions
- Brake accessories providing controlled product flow on inclines
These configuration capabilities ensure perfect alignment between equipment specifications and operational requirements. This tailored approach maximizes productivity improvements while minimizing implementation challenges throughout deployment processes.
Integration Excellence Across Operations
Effective material handling rarely relies upon single equipment types throughout entire processes. Naili manual conveyors integrate seamlessly with complementary systems creating comprehensive material movement solutions.
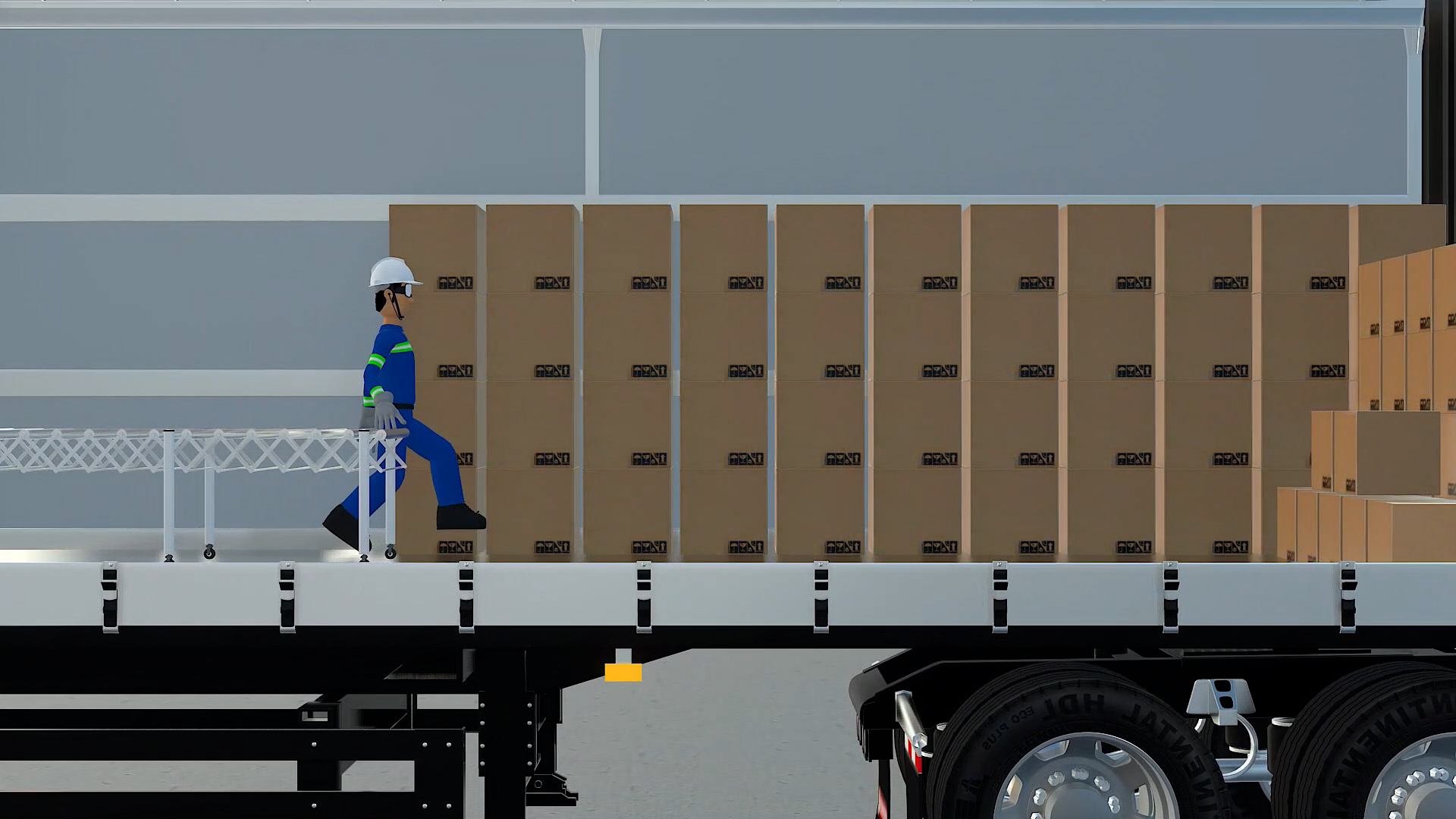
Powered System Compatibility
Strategic combinations utilizing manual sections where appropriate while implementing powered components where necessary optimize operational efficiency while minimizing energy consumption. Manual conveyors feature connection compatibility with:
- Hydraulic loading/unloading bridges providing dock-to-trailer transitions
- Powered roller sections creating hybrid transport systems
- Belt conveyor interfaces allowing smooth transfers between technologies
- Telescopic powered extensions reaching deep within trailers or containers
- Sortation system feeding providing economical product delivery toward automated equipment
These integration capabilities transform individual conveyor sections into comprehensive material handling solutions addressing entire process requirements. Their implementation frequently yields productivity improvements substantially exceeding expectations based upon individual component specifications alone.
Facility Layout Optimization
Effective material handling system implementation demands thoughtful planning aligning equipment capabilities with physical constraints and process requirements. Naili manual conveyors include numerous features facilitating optimal integration:
- Adjustable support legs accommodating various height requirements
- Multiple width options matching specific product dimensions
- Standardized connection points ensuring smooth transfers between sections
- Brake accessories controlling product flow on inclines
- Telescopic capabilities navigating around facility obstacles
Facility engineers appreciate these considerations during implementation planning! Their flexibility allows creating optimized material flow pathways without expensive building modifications frequently required with less adaptable equipment alternatives.
Durability Factors for Continuous Operation
Distribution environments represent material handling’s ultimate durability challenge—continuous usage in demanding conditions. Naili manual conveyors excel through robust construction engineered for extended service lifespans.
Premium Material Selection
Component quality dramatically impacts equipment reliability within demanding applications. Naili manual conveyors feature thoughtfully selected materials appropriate for specific operational requirements:
- 201 stainless steel frames providing exceptional structural integrity
- Q345 high-strength steel components ensuring reliable performance
- Industry-standard 608 bearings delivering smooth operation throughout extended lifespan s
- Galvanized surface treatments protecting against environmental factors
- ABS engineering plastic wheels offering durability without excessive weight
Maintenance managers report significantly reduced component replacement requirements compared with alternative solutions! These quality differences translate directly toward improved uptime statistics—a critical factor within continuously operating distribution environments where equipment reliability directly impacts operational profitability.
Simplified Maintenance Requirements
Even exceptional equipment eventually requires service attention ensuring continued optimal performance. Naili manual conveyors feature numerous design elements simplifying these requirements:
- Minimal moving components reducing potential failure points
- Standard bearing sizes simplifying replacement parts inventory
- Tool-free roller/wheel removal expediting cleaning procedures
- Modular construction allowing selective component replacement
- Corrosion-resistant materials extending service intervals
These thoughtful design considerations minimize service time requirements while maximizing equipment availability throughout operational lifespans. Distribution operations particularly appreciate these characteristics within high-volume environments where throughput interruptions create significant business impacts.
Return on Investment Analysis
Equipment acquisition decisions increasingly rely upon comprehensive financial analysis beyond initial purchase considerations. Naili manual conveyors deliver exceptional return metrics through multiple impact areas.
Capital Investment Efficiency
Manual conveyor systems represent material handling’s ultimate cost-effectiveness through minimal acquisition investment:
- Simplified mechanical design reducing manufacturing costs
- No electrical component requirements eliminating expensive controls
- Modular construction allowing selective implementation
- Minimal installation requirements reducing deployment expenses
- Extended service lifespan maximizing investment utilization
Operations implementing manual conveyor systems typically report acquisition costs 60-80% lower than comparable powered alternatives! This dramatic reduction creates immediate financial advantages while simultaneously delivering necessary material handling capabilities throughout facilities.
Operational Cost Elimination
Beyond acquisition advantages, manual conveyor systems deliver ongoing operational savings through multiple factors:
- Zero energy consumption throughout entire operational lifespans
- Minimal maintenance requirements reducing service labor costs
- Reduced component replacement minimizing ongoing expenses
- Simplified operator training decreasing workforce development investments
- Extended equipment lifespan maximizing initial capital investment
managers report dramatic operational cost reductions following implementation! These ongoing savings continue delivering financial benefits throughout equipment lifespans—often exceeding a decade within normal usage environments.
Sustainability Advantages
Modern organizations increasingly emphasize environmental responsibility throughout operations. Manual conveyor systems deliver significant sustainability benefits through:
- Zero energy consumption reducing carbon footprint
- Minimal lubricant requirements decreasing chemical usage
- Extended service lifespans reducing manufacturing resource consumption
- Simplified component recycling improving end-of-life environmental profile
- Durable construction minimizing replacement frequency
These environmental advantages increasingly influence acquisition decisions as organizations implement comprehensive sustainability initiatives! The inherent efficiency of manual conveyor technology aligns perfectly with these objectives while simultaneously delivering operational performance improvements.
FAQ
How steep an incline can manual conveyors handle?
Most gravity conveyors operate effectively between 2-5° inclines depending on package characteristics. Heavier items generally require less angle while lighter products typically need steeper slopes ensuring consistent movement. Brake accessories can control descent speeds on steeper declines when necessary.
What’s the maximum length possible for a manual conveyor line?
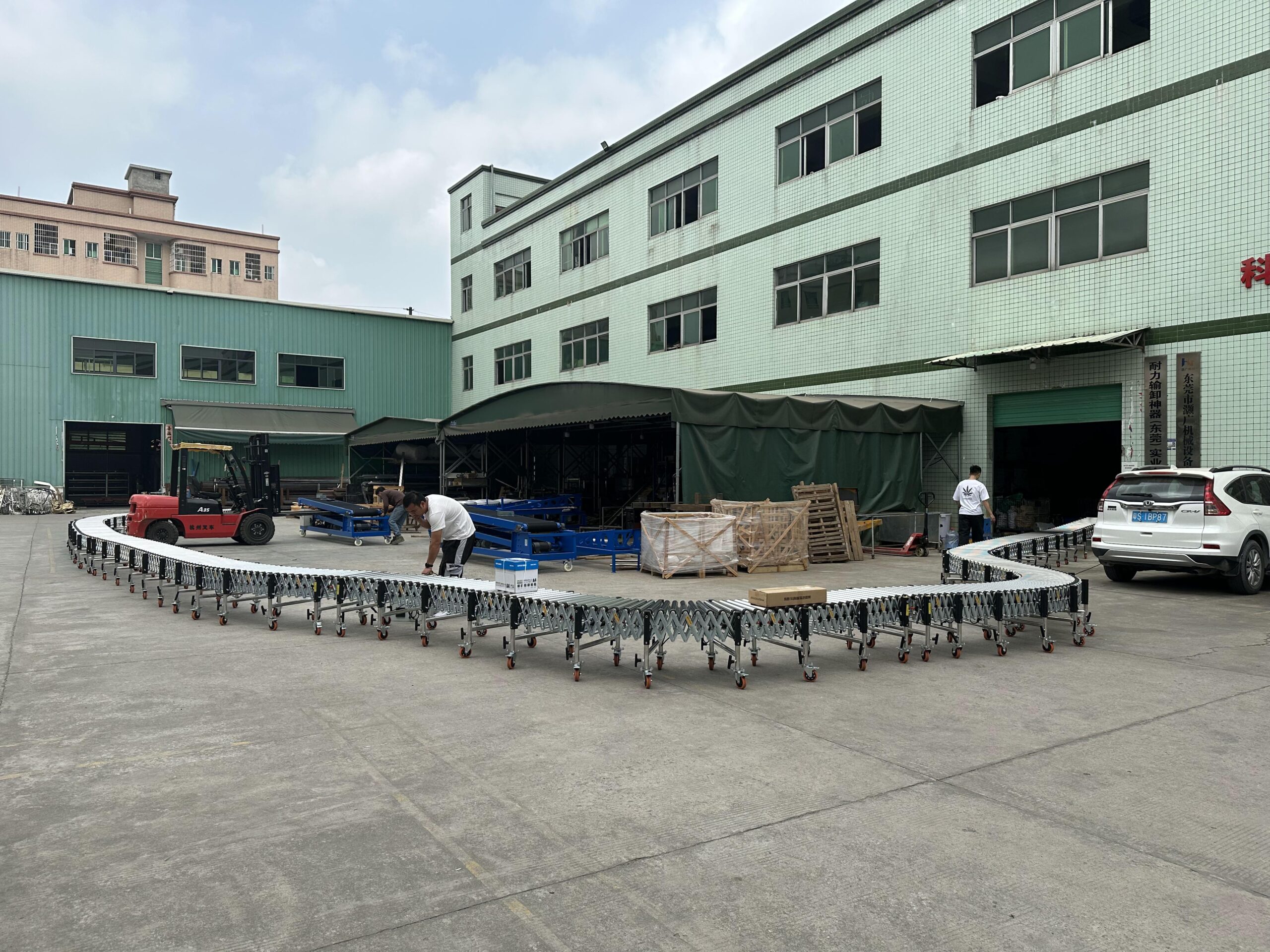
Practical limits depend primarily on package characteristics rather than equipment capabilities. Most operations successfully implement continuous lines reaching 15-25 meters through multiple connected sections. Longer configurations may require occasional powered sections maintaining product momentum throughout extended distances.
Can manual conveyors handle irregular package shapes?
Absolutely! Roller spacing accommodates most irregular items effectively. Particularly challenging shapes perform better on skate wheel versions providing additional contact points. Very unusual items might benefit from shallow trays ensuring stable transport throughout conveyor paths.
What maintenance does a manual conveyor system require?
Almost nothing! Occasional visual inspection checking alignment and component condition typically suffices. Semi-annual bearing lubrication maximizes operational smoothness though many installations operate years without attention. The minimal component design virtually eliminates maintenance requirements compared with powered alternatives.
How quickly can manual conveyors be reconfigured between different operations?
Remarkably fast! Most sections feature simple connection mechanisms allowing single-worker reconfiguration within minutes. The lightweight design facilitates easy repositioning throughout facilities without specialized equipment requirements. Operations frequently reconfigure entire systems within 15-30 minutes addressing changing process requirements.
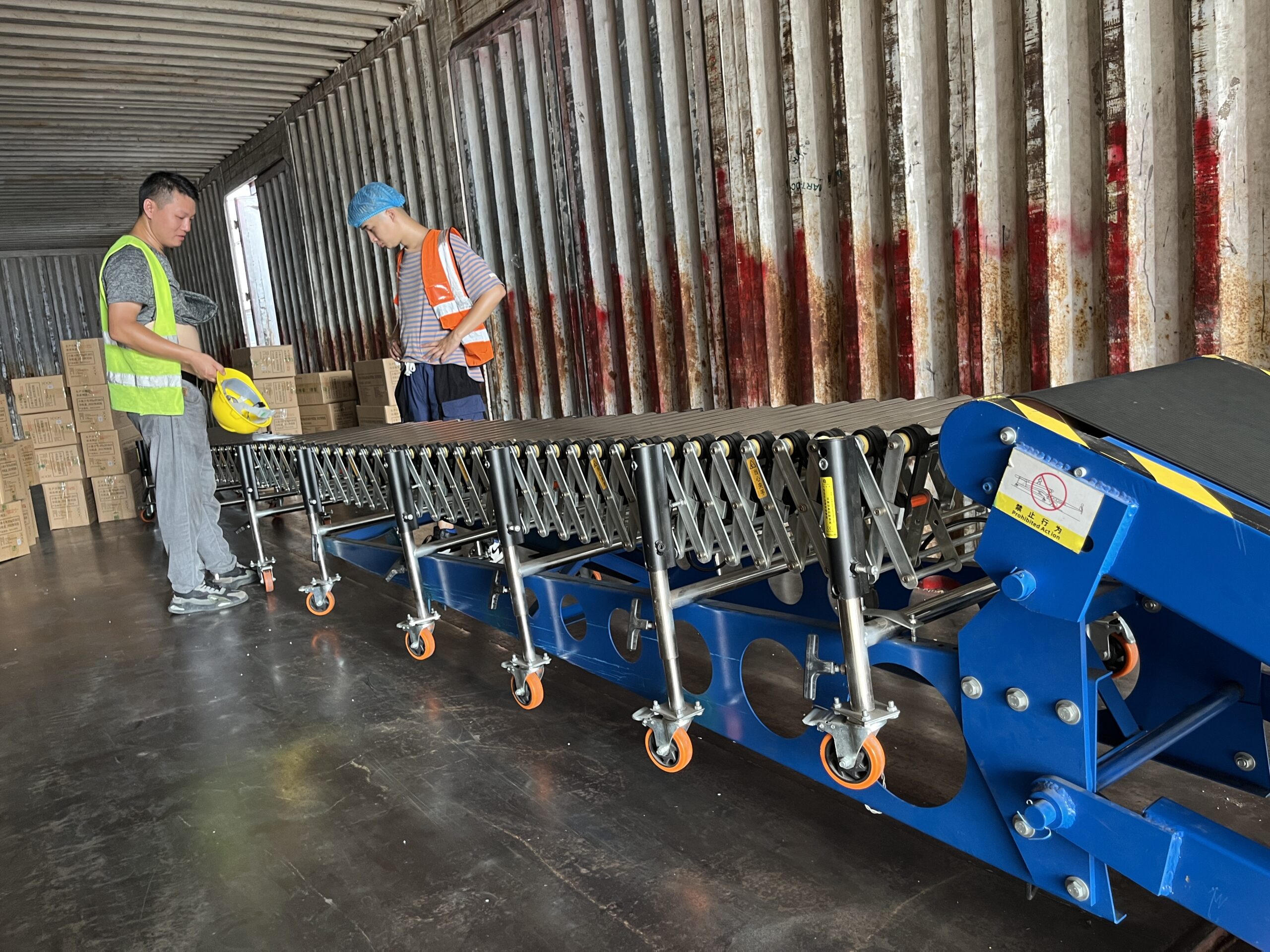