Unloading Conveyor Manufacturer
Home > Unloading Conveyor
Watch as boxes travel effortlessly from truck beds straight to warehouse floors—unloading conveyors transform receiving operations through simple yet brilliant design features.
Our Unloading Conveyor Products
420 mm
2100 mm
50 kg/m
Flat-bottomed Goods
525 mm
1500 mm
50 kg/m
Flat-bottomed Goods
Bagged Goods
485 mm
1700 mm
50 kg/m
Flat-bottomed Goods
Bagged Goods
Watch as boxes travel effortlessly from truck beds straight to warehouse floors—unloading conveyors transform receiving operations through simple yet brilliant design features. These specialized non-powered systems extend directly into vehicles where products glide smoothly along inclined pathways purely through gravitational force. Distribution centers value their operational simplicity while workers appreciate dramatic reduction in physical strain throughout demanding unloading sessions. When operations require efficient truck-to-facility product movement without power consumption or complex mechanical components, gravity-based unloading conveyors deliver impressive performance through elegantly simple engineering approaches.
Perfect Tools for Receiving Operations
Unloading conveyors excel specifically within receiving environments where their unique characteristics align perfectly with operational requirements:
Streamlined Truck Unloading
These specialized systems dramatically transform vehicle unloading processes:
- Direct vehicle access through expandable designs
- Continuous product flow without manual carrying requirements
- Reduced worker fatigue eliminating repetitive lifting motions
- Accelerated unloading times (typically 30-40% faster than manual methods)
- Minimized product damage through controlled descent pathways
Distribution centers report substantial efficiency improvements after implementing dedicated unloading conveyors within receiving areas. Their operations process more vehicles daily while maintaining higher worker productivity throughout demanding unloading cycles without increasing staffing requirements.
Energy-Free Operational Advantages
Non-powered design creates significant operational benefits:
Feature | Operational Advantage | Cost Benefit |
No motors or controls | Simplified deployment | Reduced initial investment |
Zero electricity usage | Energy-free operation | Eliminated utility costs |
Mechanical-only function | Minimal maintenance | Lower service expenses |
No power connections | Installation flexibility | Simplified implementation |
Gravity-powered movement | Continuous availability | Operational independence |
Warehouse managers appreciate these advantages delivering immediate operational cost benefits while supporting broader sustainability initiatives throughout logistics operations. Their energy-free functionality maintains continuous availability regardless of power availability or infrastructure limitations throughout receiving areas.
Space-Optimized Design
Expandable configurations maximize space utilization within receiving zones:
- Compact storage position when vehicles absent
- Extended operational length during unloading cycles
- Quick reconfiguration adapting to changing requirements
- Mobility features supporting flexible deployment
- Adjustable height options matching various vehicle dimensions
This adaptability makes unloading conveyors particularly valuable within space-constrained receiving areas where permanent equipment installations prove impractical. Operations reclaim valuable floor space during non-unloading periods while maintaining full capability during active receiving cycles throughout distribution facilities.
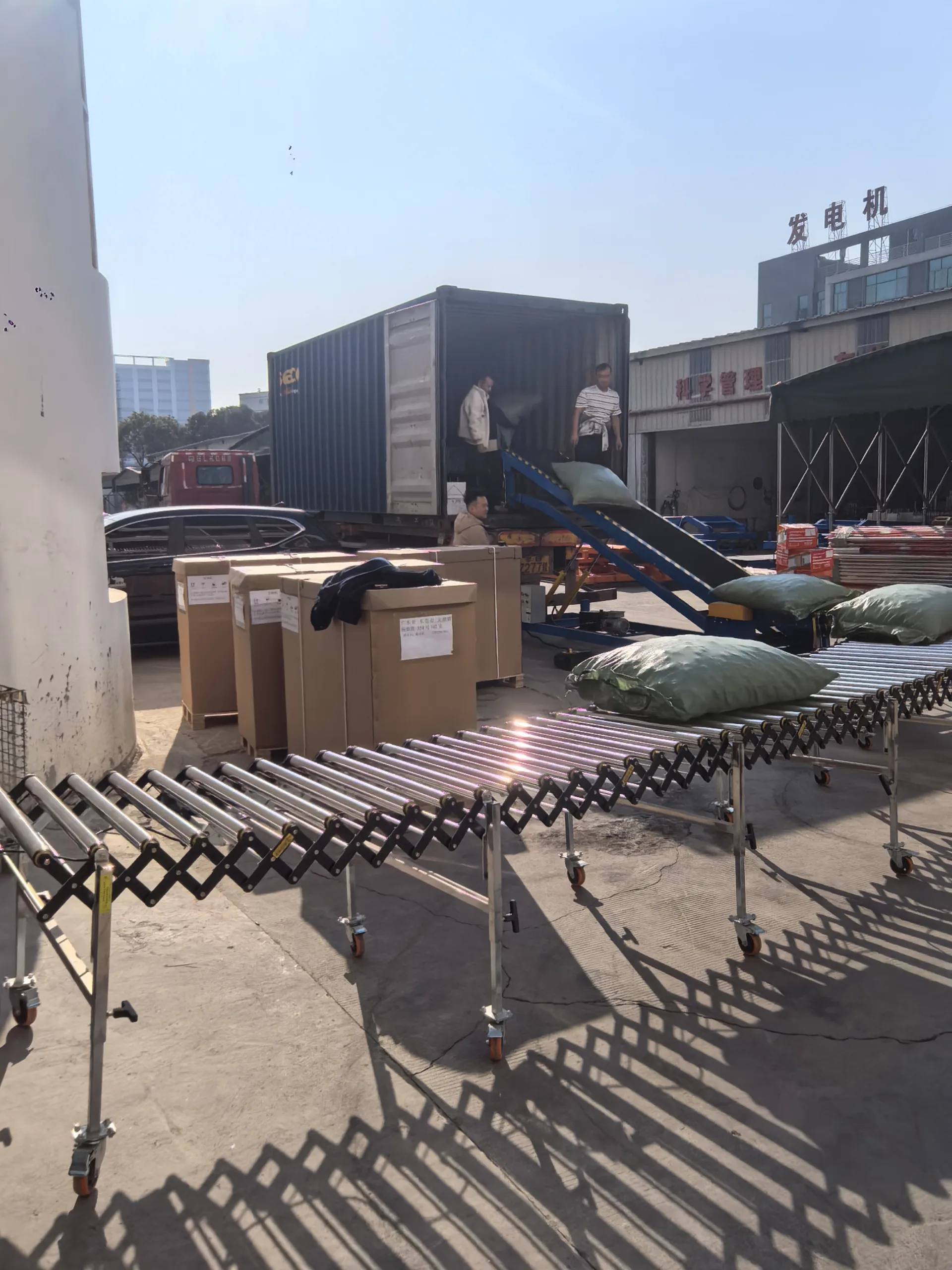
Non-Powered Systems for Unloading Applications
Different gravity-powered conveyor types address specific unloading requirements through varying performance characteristics.
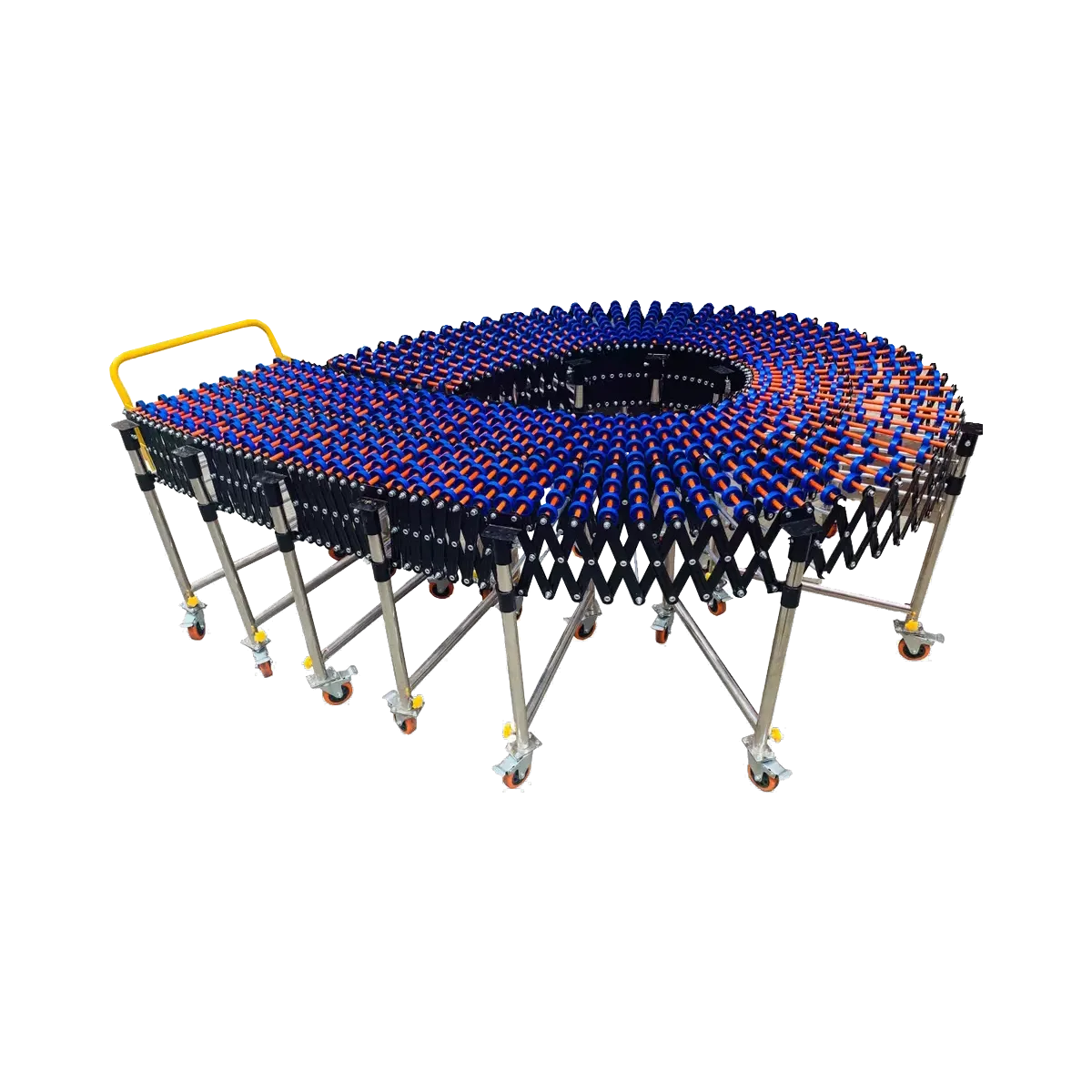
Gravity Skate Wheel Conveyors
Skate wheel systems offer exceptional flexibility for unloading applications:
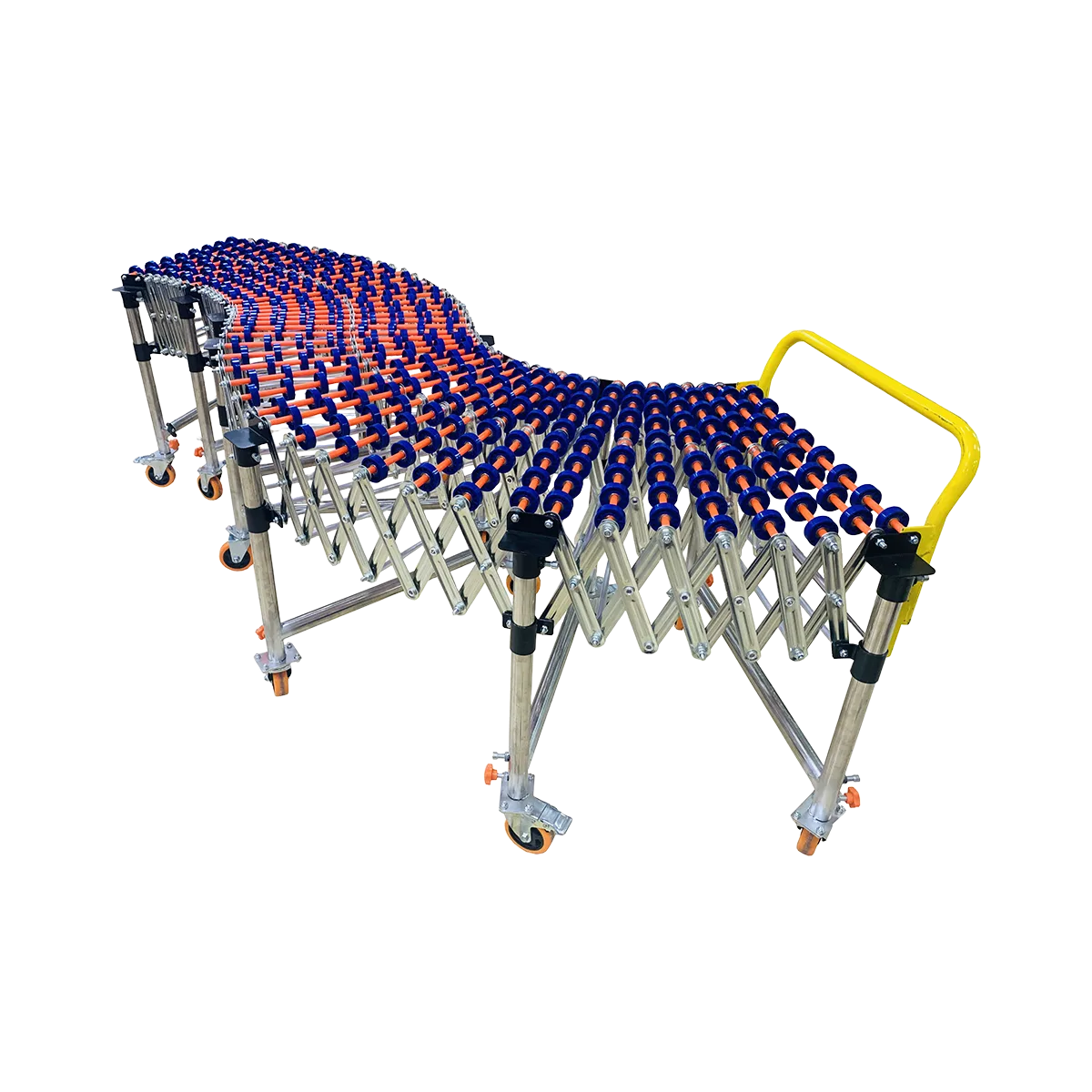
Key Advantages:
- Ultra-lightweight construction (14-22 kg per section)
- Superior mobility for quick repositioning
- Impressive expansion ratio (1:5 from collapsed to extended)
- Modest initial investment compared with alternatives
- Minimal maintenance requirements through simple design
Their expandable design (from compact 420 mm storage length to impressive 2100 mm reach) provides remarkable flexibility during truck unloading operations. Workers position these nimble systems directly into vehicle interiors where packages travel effortlessly along wheel pathways toward receiving areas without powered assistance.
Optimal Unloading Applications:
- Boxed products with flat, regular bottoms
- Standardized shipping containers
- Moderate weight packages (under 50 kg/meter)
- Operations requiring frequent system repositioning
- Budget-conscious facilities seeking maximum value
Distribution centers particularly value skate wheel systems when unloading standardized parcels with consistent dimensions. Their impressive weight-to-capacity ratio makes repositioning exceptionally easy between different dock doors throughout receiving operations.
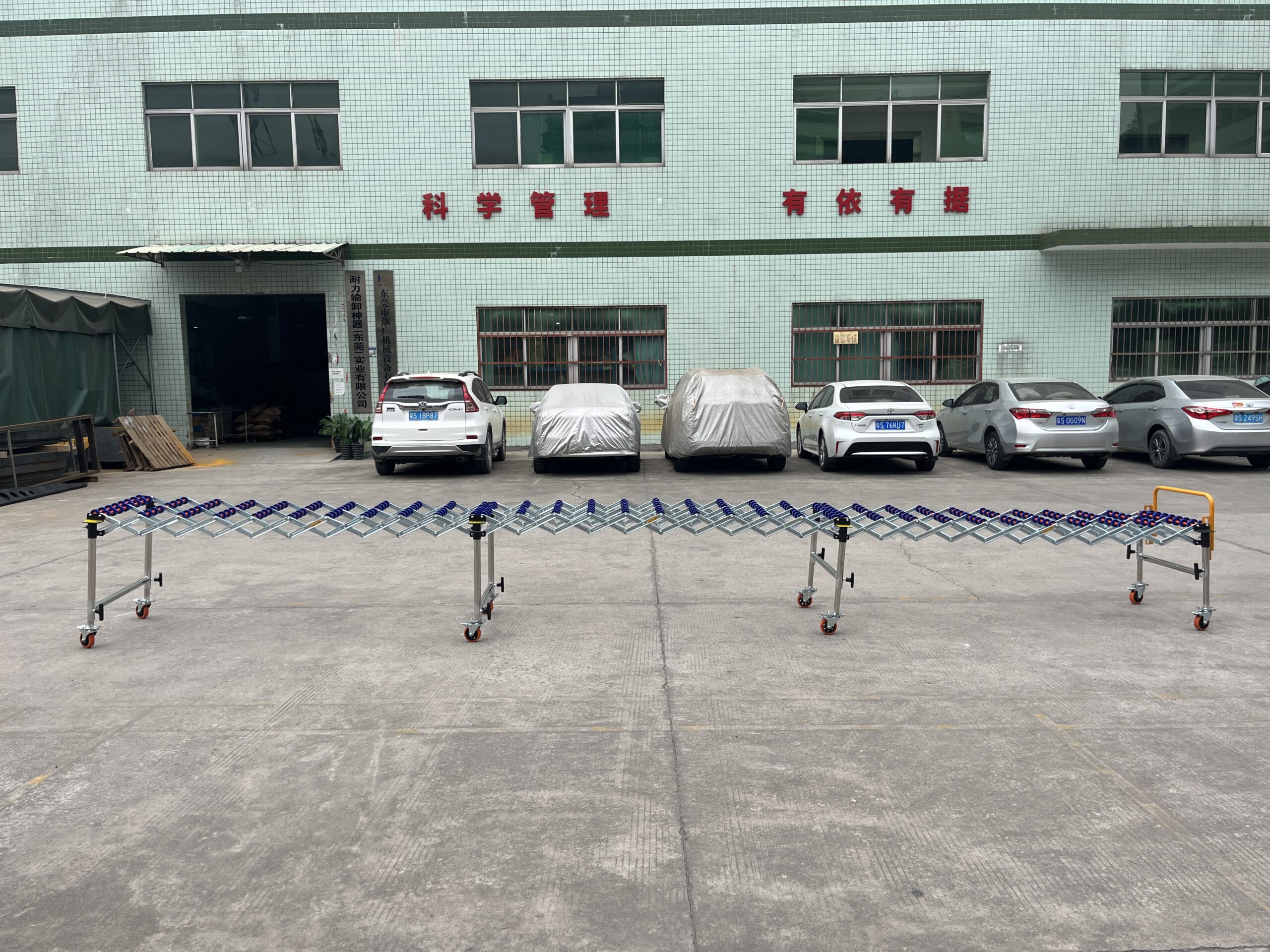
Gravity Roller Conveyors
Roller systems provide enhanced capability handling diverse package types:
Key Advantages:
- Superior weight distribution through continuous roller contact
- Excellent handling of irregular packages or varied dimensions
- Enhanced durability for demanding environments
- Consistent performance across wider package variety
- Stable product transport without directional wandering
Their expandable configurations (extending from 485-525 mm to 1500-1700 mm) deliver excellent unloading functionality while maintaining robust construction handling demanding operational requirements. Distribution centers select roller systems when unloading mixed package types requiring superior support throughout transportation paths.
Optimal Unloading Applications:
- Mixed package dimensions within single shipments
- Products with irregular bottom surfaces
- Heavier items requiring additional support (up to 50 kg/meter)
- Operations processing diverse product types
- Facilities prioritizing durability over maximum mobility
Available in both 38 mm and 50 mm roller diameter configurations, these systems balance operational flexibility with robust construction supporting various unloading requirements throughout distribution environments.
Key Differences for Unloading Scenarios
Understanding performance variations helps operations selecting appropriate unloading systems:
Feature | Gravity Skate Wheel | Gravity Roller |
Weight | Significantly lighter | Moderately heavier |
Package Contact | Point contact only | Continuous surface contact |
Irregular Items | Limited effectiveness | Excellent performance |
Weight Capacity | Good (50 kg/m) | Better (50 kg/m with superior distribution) |
Mobility | Exceptional | Very good |
Initial Investment | Lower | Moderate |
Both systems effectively address unloading requirements while offering different performance characteristics matching specific operational needs. Many facilities maintain both types deploying appropriate solutions based on particular unloading scenarios throughout receiving operations.
Strategic Implementation for Maximum Efficiency
Maximizing unloading conveyor benefits requires thoughtful implementation addressing specific operational requirements and facility characteristics.
Optimal Deployment Strategies
Strategic positioning dramatically improves overall unloading efficiency:
Vehicle Integration Techniques:
- Position conveyor end precisely at truck bed height
- Extend system adequately into vehicle interior
- Ensure proper angle creating appropriate product flow
- Stabilize extended section preventing unwanted movement
- Maintain sufficient side clearance preventing product catches
Receiving Area Configuration:
- Create adequate accumulation zone at conveyor discharge
- Position inspectors strategically along product flow path
- Ensure proper lighting supporting visual inspection requirements
- Maintain clear pathways around conveyor systems
- Establish ergonomic workstations near conveyor discharge
These configuration elements transform standard equipment capabilities into optimized unloading solutions. Operations teams customize deployment matching unique facility requirements while maximizing efficiency throughout daily receiving cycles.
Slope Angle Optimization
Incline configuration represents critical success factor determining appropriate product flow characteristics:
- 2-3° slope – Ideal for standard cardboard boxes with moderate weight
- 3-4° slope – Appropriate for lightweight plastic containers or totes
- 1.5-2° slope – Best for heavier products preventing excessive speed
- 4-5° slope – Sometimes necessary for items with high friction resistance
Finding perfect balance between insufficient movement (products stalling mid-journey) versus excessive speed (creating potential damage or safety concerns) requires thoughtful implementation planning. Adjustable support legs facilitate proper slope configuration with height options accommodating specific operational requirements throughout receiving areas.
Safety Considerations
Proper implementation includes essential safety elements protecting both workers and products:
- Secure braking systems preventing unwanted conveyor movement
- Clear operational zones around equipment preventing collisions
- Appropriate guard rails on elevated sections preventing falls
- Proper training ensuring correct operational procedures
- Regular inspection routines maintaining safe working conditions
These safety elements maintain workplace protection while supporting regulatory compliance requirements throughout unloading operations. Comprehensive safety planning prevents potential injuries while maintaining operational productivity throughout distribution environments.
Operational Best Practices
Maximizing unloading conveyor effectiveness requires proper operational techniques addressing specific handling requirements and performance characteristics.
Effective Unloading Techniques
Proper methods dramatically improve operational efficiency:
Worker Positioning Strategies:
- Station personnel strategically along conveyor length
- Position skilled workers inside vehicle guiding initial placement
- Locate quality inspectors along pathway identifying potential issues
- Place packers or processors at conveyor discharge point
- Maintain clear communication between team members throughout process
Product Handling Approaches:
- Place items consistently on conveyor surface
- Orient packages properly preventing potential jams
- Space items appropriately preventing collisions or pile-ups
- Monitor flow rate adjusting placement timing accordingly
- Direct damaged or problematic items toward separate handling paths
These operational approaches maximize throughput while maintaining product integrity throughout unloading processes. Well-trained teams develop efficient rhythms dramatically improving overall receiving productivity throughout distribution operations.
System Maintenance
Simple preventative attention significantly extends equipment lifespan:
Maintenance Activity | Frequency | Personnel Requirements |
Debris removal | Daily | Basic operator |
Wheel/roller inspection | Weekly | Basic operator |
Frame examination | Monthly | Basic technician |
Support leg verification | Monthly | Basic technician |
Connection assessment | Quarterly | Basic technician |
These straightforward maintenance procedures typically require minimal technical expertise while delivering significant performance benefits through consistent preventative attention. Most activities integrate easily within standard operational routines without requiring specialized skills or extensive downtime periods.
Application Success Stories
Real-world implementations demonstrate exceptional unloading conveyor value across diverse operational scenarios.
Distribution Center Transformation
Major online retailer transformed receiving operations through strategic unloading conveyor implementation. Their challenge: processing 35+ delivery vehicles daily while minimizing labor requirements and reducing worker fatigue. Their solution: deploying combination of skate wheel and roller gravity conveyors creating flexible unloading stations throughout receiving docks.
Results proved remarkable:
- Unloading times decreased 42% compared with manual methods
- Worker fatigue reduced substantially throughout shifts
- Product damage incidents declined nearly 60%
- Receiving capacity increased without staffing additions
Management particularly appreciated equipment flexibility—systems expanded during active unloading then contracted during vehicle changeovers, preserving valuable dock space while maintaining operational capabilities throughout receiving cycles.
Manufacturing Component Receiving
Industrial equipment manufacturer streamlined parts receiving through dedicated unloading conveyor implementation. Their specialized solution incorporated gravity roller systems handling diverse component shapes while maintaining controlled descent throughout unloading processes.
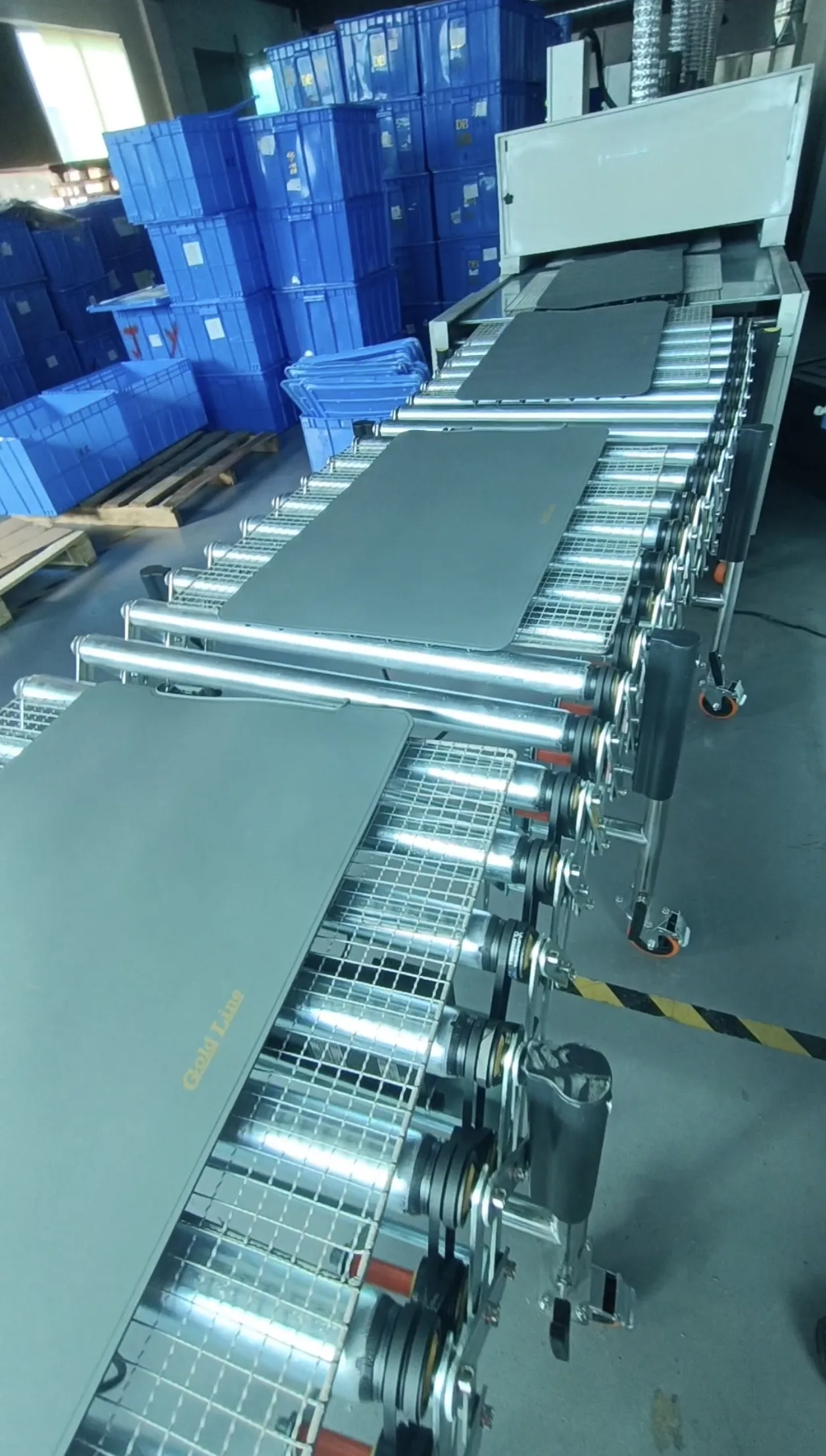
Performance metrics revealed substantial improvements:
- Component processing time improved 37%
- Labor requirements decreased significantly
- Employee satisfaction increased through reduced physical demands
- Receiving accuracy improved through controlled handling processes
This success encouraged additional implementations throughout other facility areas, creating comprehensive gravity-powered material handling networks maximizing efficiency while minimizing operational expenses throughout manufacturing operations.
FAQ
Which conveyor type works best for unloading operations? Gravity skate wheel systems excel handling standard boxes with flat bottoms while offering maximum mobility between dock positions. Gravity roller conveyors provide superior performance with irregular packages or heavier items requiring additional support. Many operations maintain both types deploying appropriate solutions based on specific unloading scenarios.
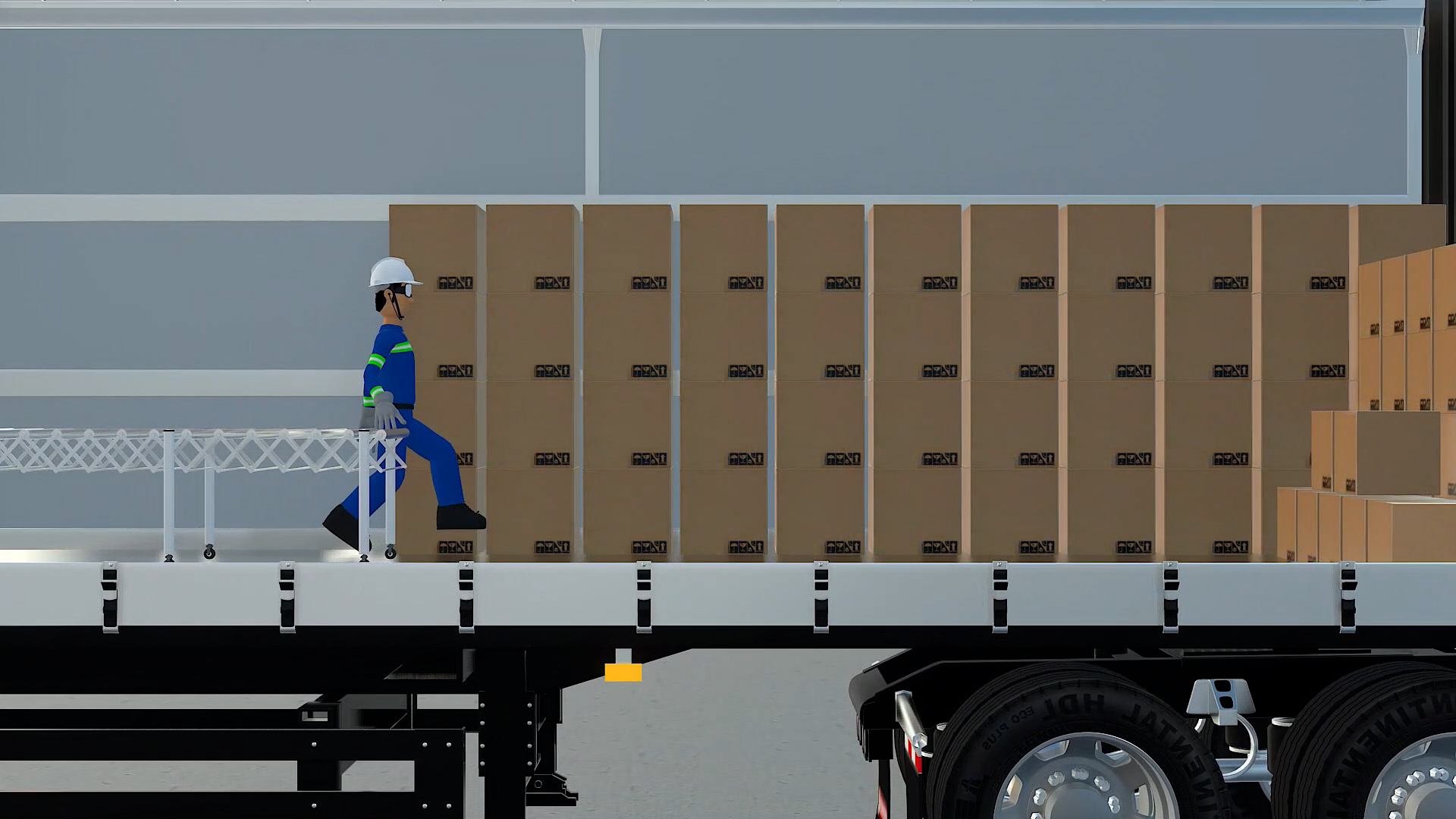
What slope works best for unloading conveyors? Most applications perform optimally between 2-4° incline depending on package characteristics. Lighter items typically require less slope (2-3°) while heavier packages need minimal incline (1.5-2°) preventing excessive speed. Testing with actual products before permanent implementation ensures proper flow characteristics throughout specific operational environments.
How quickly can unloading conveyors be repositioned? Typical systems require only 1-2 minutes for complete redeployment between dock positions. Their lightweight construction combined with mobility features allows quick reconfiguration matching changing operational requirements throughout receiving areas without specialized equipment or excessive effort.
What maintenance do unloading conveyors require? Minimal attention keeps systems performing optimally. Daily debris removal, weekly wheel/roller inspection checking free rotation, plus monthly frame examination confirming proper alignment typically suffices maintaining excellent performance. Most maintenance activities require basic tools without specialized expertise—another significant advantage compared with powered alternatives.
Can unloading conveyors handle heavy items? Yes, though weight limitations vary by system type. Gravity roller conveyors typically handle up to 50 kg/meter with excellent weight distribution while skate wheel systems manage similar capacities requiring wider contact surfaces supporting heavier items. Both system types include cautions regarding dynamic impact forces during movement requiring thoughtful operational practices handling substantial weights.
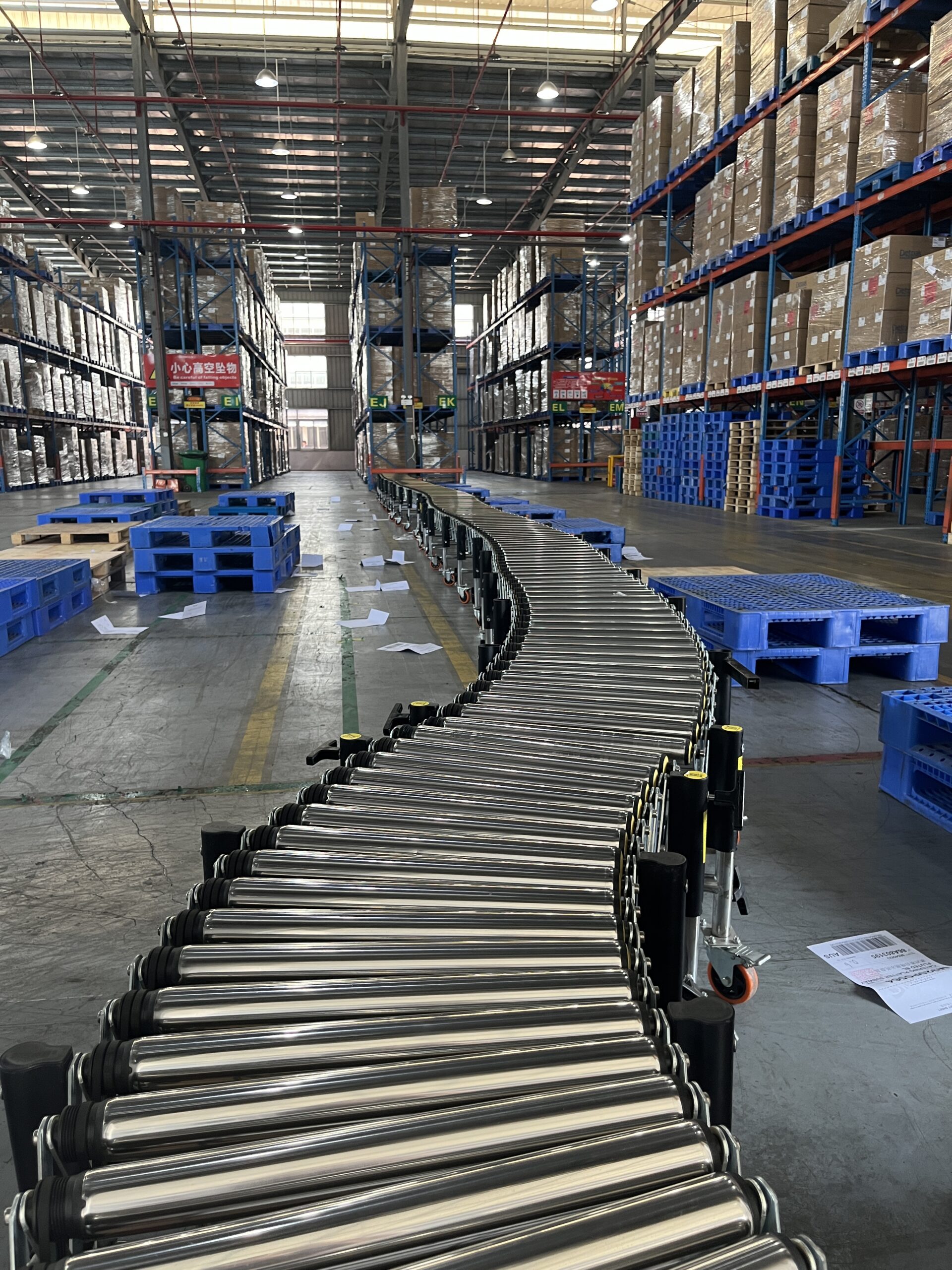